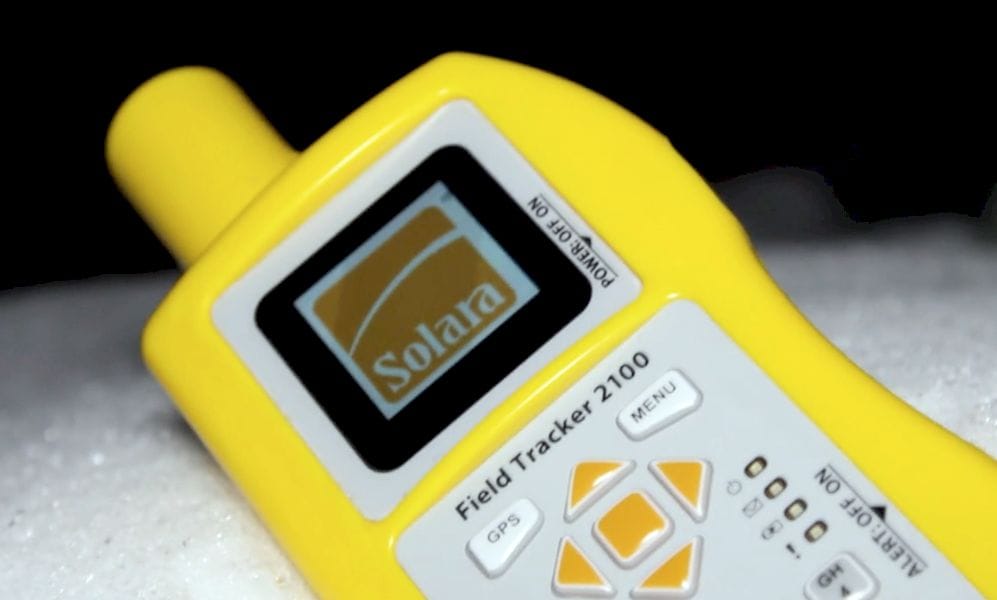
How do you choose your 3D printer filament?
While some may simply buy the cheapest product available, professionals have more interesting concerns with the materials they use to produce parts.
In a great many cases the primary concern would be part strength, as the designs for parts very typically require them to function within a specific engineering situation. If the part is not sufficiently strong, then it will fail with potentially catastrophic results.
Another key property of interest is heat. Each material has a specific range of temperatures between which it provides the desired strengths and other properties. If a part, for example, is exposed to its heat deflection point temperature, it’s going to deform and likely fail. Part strength is usually associated with temperature.
Everyone performing 3D printing knows these things. But there are other engineering properties of materials that are, in some cases, of critical importance. One that is frequently forgotten and ignored by materials providers are the electrical properties.
Imagine you’re designing a radio device, where the radio elements are embedded within your 3D printed prototype case. How well does your radio send emissions through that case? Are those waves affected by the material? Does the device’s resulting radio power diminish significantly because of the case’s material? Did you just destroy your product’s usability because you chose the wrong material to make a case from?
Few materials providers recognize this is a specification that is sometimes required by their users, and thus it’s nearly impossible to figure out the electrical properties of a material without tedious, expensive and delaying trial and error approaches.
But now it turns out that Stratasys has published the electrical properties for at least some of their materials, and radio product designers can now purposefully design prototype cases knowing exactly how their product will perform.
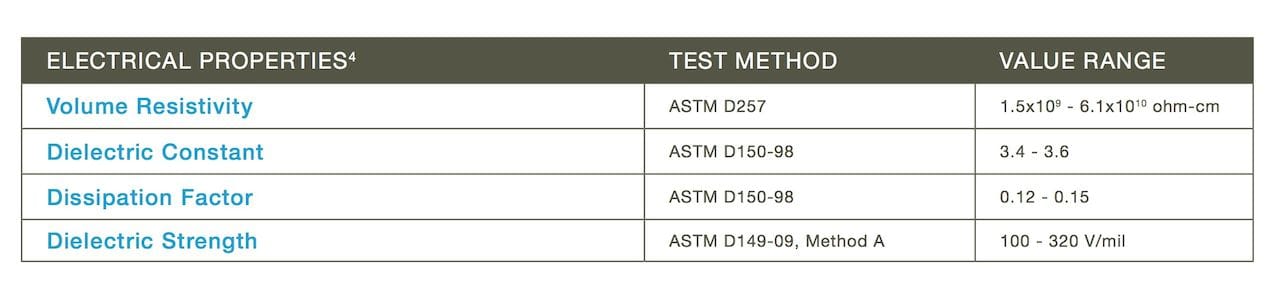
This is a significant development for radio product designers, and it efficiently opens up the world of 3D printing to their projects. We spoke with Tom Tessier, CEO of Solara Remote Data Delivery, a firm that manufactures interesting portable data devices that communicate by satellite from the most extremely remote locations on the planet. He says:
Antennas that actually work in testing makes my life MUCH easier. It has been a BIG headache trying to correlate 3D printed case materials to actual injection moulded plastics.
Now we can actually test with something predictable. Before 3D printing, you basically machined your injection mould, shot the plastic and crossed your fingers on it working. Usually it didn’t, so you would spend another $15,000 and a month or two of time re-machining the mould and trying different material, tuning antennas, etc. Having this predictability in our test material is a big deal.
What’s the moral of this story? Simply this: ALL 3D printer material vendors should publish electrical specifications for their products. If so, they may gain some additional customers.
Via Stratasys