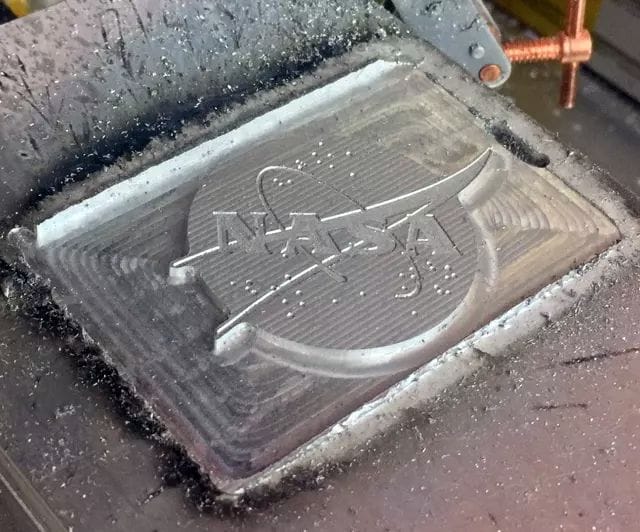
The New Space space is heating up as an increasing number of private companies leverage 3D printing to push next-generation space technology.
Already well-known in the industry is Made In Space, which earlier sent two 3D printers to the International Space Station (ISS). Now, the company has won a NASA contract to continue developing its hybrid metal manufacturing system, VULCAN.
Whereas the commercial Additive Manufacturing Facility currently aboard the ISS is designed for plastic parts, the VULCAN is meant for printing with both polymers and metals, like titanium and aluminum, or multiple materials at once. The VULCAN combines additive manufacturing (AM) with traditional machining, fabricating a near net-shaped part before machining it to its final shape.
The system also features an automated quality check sensor system for automatic quality control. The plan is for the VULCAN to produce parts that require the strength and durability possible with aerospace-grade materials, such as housing for life support systems.
“The VULCAN hybrid manufacturing system allows for flexible augmentation and creation of metallic components on demand with high precision,” explained Mike Snyder, Made In Space chief engineer and principal investigator. “VULCAN is an efficient, safe capability that utilizes the minimum amount of resources during manufacturing processes.”
Read more at ENGINEERING.com