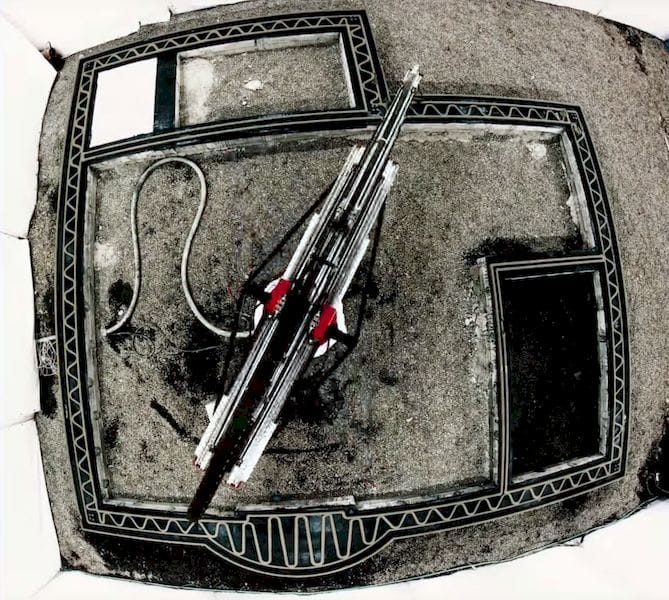
Apis Cor says they are the first company to produce a mobile construction 3D printer, and they may in fact be right.
We’ve heard of a few other companies attempting this type of device, but the offering from Apis For appears to be implemented and working.
The device is essentially a “CNC Concrete Pump”, to use an analogy similar to that used for desktop 3D printers as a “computer controlled glue gun”.
Apis Cor’s system involves a large hopper in which material can be mixed. They say they can extrude different mixes of concrete, geopolymer and fiber concrete. This mix is then fed by a pump system to the extruder, which is a carefully balanced rotating mechanism that accesses the build volume in a circular manner.
By adjusting the “reach” of the extruder, the Apis Cor system can create arbitrary geometries that emerge as structural building walls.
Like virtually all 3D construction printers, this system prints only the vertical walls and does not do floors, ceilings or roofs.
Similarly, a completed structure requires not only the 3D printed segments, but also plenty of manual work supplied by traditional workers. As you can see in this image from their video, the 3D printer has created the shell for the foundation, while workers manually install reinforcing metal and pour in bulk concrete to complete the foundation.
One interesting advantage is to print walls with captured air cells to provide additional free insulation – while saving material at the same time. This is similar to the lattice approach used by many manufacturers these days.
Sorry, this is not a system that completely 3D prints a usable structure; it creates only some of the components, and key ones at that. A completed structure would definitely require much work by traditional contractors.
However, Apis Cor says they do provide an ability to save on the costs of the segments they do produce. They say:
Foundation works — minus 15% Printer prints a retained framework for foundation, in which reinforcing armatures are installed and heavy concrete is poured in.
Building frame construction — minus 25% Machine builds a retained framework for a ferroconcrete base, self bearing walls and partitions. With ferroconcrete as its core the building has all the engineering calculations methods readily available.
Outer and inner finishing – minus 60% Printer prints walls with machine precision and makes them even and smooth. Roughing stage can be skipped straight to final finishing.
Services — minus 20% We plan the layout of electrical junctions, engineering systems and nodes within the house in advance. Then we upload the project in the software and get a ready blueprint for laying down inner services.
Logistics — minus 20-30% By reducing a considerable amount of additional work there is no need for extra tools and materials. 3D printing technology lowers general material consumption of construction.
These are not spectacular savings, but certainly very welcome. There are other benefits as well, such as the ability for the machine to work without much human intervention, which leads to increased quality and more rapid completion. Apis Cor says their system can extrude 1 to 10m of linear material per minute, which is pretty quick.
What I like about this system is that it doesn’t pretend to “do everything” and “3D print houses in 24 hours”, like some others in this space. Instead, they seem to be focusing on their specific capabilities as part of a larger building project.
The other aspect I like about this project is that it seems quite feasible. The base technologies employed seem either already in use at building sites, or are simply scaled up versions of techniques employed by smaller 3D printers. It should work.
Where they will have to pioneer is in the environment, which is quite different from most 3D printers. The Apis Cor system is intended to work outdoors, where they must contend with temperature, precipitation and wind. They say they cannot deploy in winds greater than 15m/s, and that rain can “blur” the print definition.
If this company can make a go of this project, then it could lead to much bigger things. Imagine combining this approach with similar automated concepts, like a bulk concrete filler, for example, or a rebar-placement system. One could see the process of building a structure gradually be automated, step by step.
Via Apis Cor (Hat tip to Morgan)