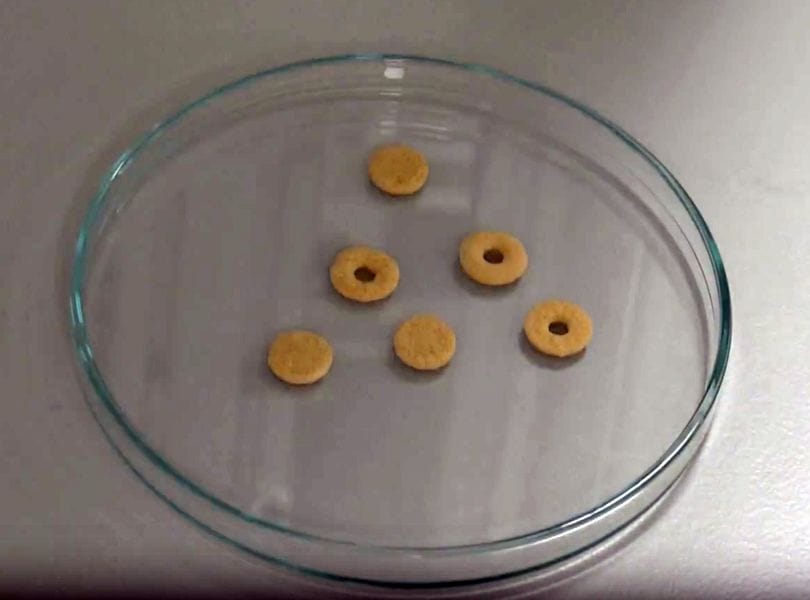
Sintratec published an interesting story of how one of their clients has been using their 3D printer in a very different manner.
The Swiss-based company produces a couple of inexpensive SLS-style 3D printers that are capable of producing strong nylon parts, and more recently a flexible material as well.
At first glance, one might think SLS 3D printing is easy: simply blast a laser at a flat surface of thermoplastic powder, fusing it into the desired shape. But it turns out it’s far more complex, as there are a number of challenges to achieve optimum printed results.
Like other 3D printing processes, speeds, feeds and temperatures are of tremendous importance to get the best prints possible. This is also true in Sintratec’s systems.
Some SLS machine vendors tackle this problem by spending considerable time in their labs discovering the best settings, which they then deploy with their systems and materials. It’s for this reason some companies insist on use of proprietary materials in their products: it’s a kind of quality guarantee. Well, that and increased profits, in some cases, too.
But the nature of SLS systems often allows use of third party materials; you simply load in a different powder. Thus, it could be an advantage to permit the operator to tweak the printing parameters to match whatever material is being printed.
That’s absolutely the case with Sintratec’s concept, as their printing software allows considerable “play” in the multiple 3D printing parameters. It allows their customers to perform deep experiments with different materials and printing scenarios, presumably in an effort to squeeze out even better results.
However, this wide control capability was leveraged in a rather different manner by one Sintratec customer.
UCL-spin off startup FabRx intends on developing systems for fabricating medicines. They took possession of a Sintratec Kit, the company’s lowest cost SLS 3D printer option, and leveraged those highly flexible printing options to enable the production of what they call “Printlets”, a 3D printed pharmaceutical tablet. They explain:
Some time ago we included a Sintratec Kit SLS printer in our armamentarium. We choose to buy a Sintratec Kit because of its open parameters. In order to print medicines, very specific parameter settings are required since drug and excipients would be completely degraded otherwise. With the Sintratec Kit the parameters like laser speed and material temperature could be finely adjusted to exactly meet our requirements.
The idea here is to enable the production of custom drugs, with perhaps unique ingredients and dosages, all of which would be possible with 3D printing technology, just like it is done for industrial parts.
These pills are in fact agglomerations of medicinal materials and bio-harmless binder, just like the ones you’d find in a drugstore. The 3D printer was used to form them into pill-shapes and fuse them together.
This is an interesting problem. Normal pills are typically made by compression, but the SLS process involves blasting a high-power laser at the material, something common pills obviously don’t experience. FabRx must have done some material research to ensure that the laser exposure did not affect the medicinal functionality of the material.
Another interesting aspect is that the input material must be a single type of powder. It can be pre-mixed with whatever ingredients are desired, of course, but the printer handles only one powder at a time. This means that the inside and outside surface of the Printlet must be made from the same material. It’s not clear whether the powder is continuously sintered throughout the pill, or if merely the outside surface is fused, capturing the loose medicine powder inside. It’s also possible to take the output from the Sintratec machine and follow on with additional post-printing processes to, for example, add an external surface.
This is nothing like 3D printing industrial parts, the original intention of this device. Here we have inventive researchers twisting a machine into a purpose it was surely not designed for, and apparently successfully.
One wonders what other unexpected uses can be made from 3D printing technology?
Via Sintratec (PDF) and FabRx