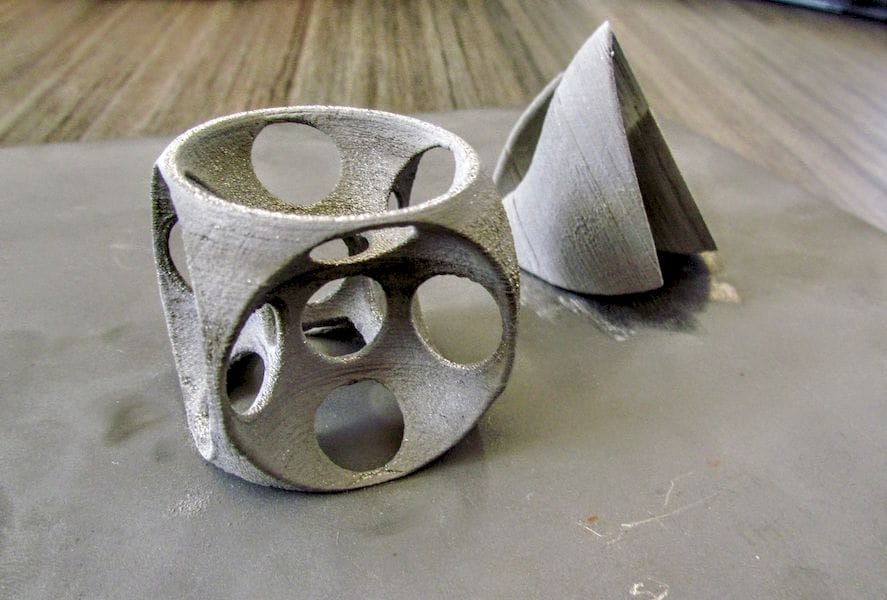
There’s a dark secret about 3D metal printing that few want to talk about: print optimizations.
This phenomenon exists to some degree in thermoplastic 3D printing, but it is far less important. The idea is to find the answer to the question: “what is the best way to 3D print this object to maximize my objectives for part quality, part cost and part speed?”
In the thermoplastic world, part quality matters only in terms of strength, as you want to orient the part to ensure the major stresses occur along the layer lines, not between them. Part cost is not much of an issue as thermoplastic is cheap, and part speed is about the same: slow.
But in 3D metal printing it’s quite a different story. Metal parts are very often used as production pieces, so their quality requirements are far stronger than for the typical prototypes made in thermoplastic.
That quality depends a lot on the thermal profiles encountered during 3D metal printing, as the energy required to melt metal powder are quite intense.
If you get it wrong, the part may slightly deform as thermal stresses flowing through the part and its support structures. You may also compromise the strength of the part as the cooling profile affects the crystallization of the metal.
Of course, if you pick a weird orientation, you could end up using far more support material than in other orientations. And that’s truly important when you are paying USD$500/kg for titanium powder, for example.
Mistakes in this area are expensive, as the cost of re-doing a 3D metal print is always high, simply due to the material costs and machine time. You really don’t want to re-print metal objects. The worst case is a trial-and-error approach where you repeatedly 3D print an object to find the optimum result.
These questions have been traditionally answered by squads of engineers who painstakingly examine each proposed print in multiple dimensions before committing to the print. That’s an expensive and time consuming process that can plug up a workflow and burn holes in your budget.
Now there may be an automated answer to this dilemma with new services from Atlas 3D, an Indiana-based startup.
Atlas 3D is a spin off of the America Makes program, where very significant research was undertaken in this area. The company is now commercializing the results of the research with the release of their Sunata system.
Atlas 3D calls the current approach to the issue a “black art”, and we don’t doubt it. It’s a highly manual process that may or may not result in the best results. Atlas 3D explains:
Sunata answers the optimal orientation and support structure question for the user! Sunata allows users to turn their designs into successful prints, the first time, every time! Users will appreciate the ability to download their designs directly into Sunata and receive the optimal orientation and associated support structures, automatically. No expensive simulation and orientation tools. No guessing. No trial and error. Simply import the .STL CAD file directly, and Sunata does the rest!
Exactly how does Sunata do this? They explain further:
Sunata’s accuracy and speed comes from its patent pending Thermal Circuit Network (TCN.) The TCN scientifically parses the print design into thermally similar layers, which are then grouped into thermally similar segments. The TCN applies its thermal modeling algorithm to arrive at the optimal orientation and support structure for that design. Simulation and orientation solutions allow users to “guess” at the optimal orientation and/or support structures and then simulate that particular “guessed” solution, but they do NOT identify the optimal orientation and support structures for the user. Sunata scientifically determines optimal orientation and support structure to yield a successful print the first time, every time, guaranteed!
But you may be thinking that there are actually different solutions depending on the goals of the operator, and that’s true. Sunata takes this into account by providing “dials” to indicate the priority of each aspect that is under analysis. Currently you can specify a balance between:
- Minimal Print Time
- Minimal Support Structure
- Minimal Support Removal
- Minimal Distortion
That should be sufficient for almost all cases.
At present they’re only optimizing for DLMS systems, but I imagine with some work they could expand this style of solution to other 3D metal printing approaches.
Sunata is implemented in a cloud service, where you pay a subscription fee to gain access. It was explained to us that they offer both pay-as-you-go and monthly volume subscription options, so there should be a solution for everyone. There’s also a free trial for those of you who’d like to test Sunata.
I’m very impressed with this solution, as it should be another piece in the puzzle whose solution would lead to much higher usage of 3D printing by industry. The traditional approaches to using 3D metal printing technologies have been immense, affordable by only the largest and richest companies. This has been a barrier to adoption, among many others.
But if a company didn’t have to hire as many engineers to perform pre-printing analysis, and instead used an automated solution, it might make the business case for smaller operations. That’s a good thing.
Now if they could also provide this solution for thermoplastic, that would be great!
Via Atlas 3D