![Keith Cox, Senior Business Manager, Additive Manufacturing, SABIC looks at a part 3D printed in ULTEM and made using the new breakaway support material at formnext 2018 [Image: Fabbaloo]](https://fabbaloo.com/wp-content/uploads/2020/05/IMG_20181115_105950_img_5eb0a1a8342af.jpg)
Global chemistry giant SABIC shares a look into its strategic focus in 3D printing.
At formnext, I was pleased to sit down with Keith Cox, SABIC’s Senior Business Manager, Additive Manufacturing, to catch up on the latest. Over the last year or so, he explained, “Our focus has really been on expanding applications for 3D printing materials.”
“We have filament materials compatible with the [Stratasys] Fortus, and have been making a conscious effort to expand those to other systems,” he continued, noting that companies such as 3ntr and Apium have used their materials. “It’s a pretty significant change for us, opening up availability to drive innovation.”
Driving innovation is just what SABIC is looking to do in additive manufacturing, and the company welcomed the opportunity to highlight existing materials and new introductions alike alongside showcase pieces made on a variety of well-known systems.
“From a product standpoint, we’re proud that our EXL AMHI240F filament was selected by TCT as material innovation of the year; it’s important to us as recognition from the industry is positive reinforcement that the industry wants differentiated materials,” Cox noted.
With many global materials companies now entering the additive manufacturing space with gusto alongside 3D printing-focused materials companies, standing out — especially in polymers — is becoming more of a challenge. The recognition at this year’s TCT Awards underscores that SABIC is on to something with their approach.
Among the materials we walked through at the SABIC booth were a new breakaway support material for the ever-popular ULTEM 9085. The company had heard a lot of feedback that supports proved a difficulty in working with ULTEM, and the new breakaway support material allows for a much easier release and “eliminates more need for secondary post-processing,” Cox noted. Now in final validation with market availability set for January, the material has been receiving “positive feedback as it enables significant cost savings.”
![[Image: Fabbaloo]](https://fabbaloo.com/wp-content/uploads/2020/05/IMG_20181115_105942_img_5eb0a1a8990bc.jpg)
While we chatted about ULTEM, Cox pointed as well to a polycarbonate FST product similar to ULTEM in terms of low smoke and toxicity properties. The FST filament, still in development and set for commercialization next year, “opens up applications without the high-temperature needs of ULTEM and can be used on more systems,” he noted. Another concept material, EXTEM, can be a fit in applications that need a higher-temperature performance than ULTEM. Directly in the ULTEM family, new ULTEM 1010 products include one specified for healthcare usage that “adheres to internal healthcare requirements, and is higher-temperature than ULTEM 9085,” Cox added.
SABIC is also active on the SLS side, where they are moving into proof-of-concept parts.
“These materials have the ability to be recycled; the material can be collected after sintering and used. We have done this after four sintering cycles. There’s an ability for significant cost savings,” Cox said.
“We’re taking our technology to produce amorphous parts, and have demonstrated the ability to produce fully amorphous parts. SLS is still on a progressive path toward commercialization.”
Looking at the literal bigger picture, SABIC is also working with large-format 3D printing. In this area, Cox noted, they have “been quite active.”
“We have a history with Cincinnati Inc. and their BAAM, and with Local Motors. Similar to the filament side, we’re becoming more printer agnostic. We’re working with the LSAM, with Titan Robotics, with CNC Bárcenas,” he explained. “Focus has primarily been on tooling on the large-format side… We really see tooling as the sweet spot for this technology.”
They do also, though, look at direct part production. While this represents a smaller focus at present than does tooling, a wheel well for Local Motors’ Olli showed off capabilities of end-use part production with SABIC’s materials, in this case a THERMOCOMP compound 3D printed on a BAAM.
![[Image: Fabbaloo]](https://fabbaloo.com/wp-content/uploads/2020/05/IMG_20181115_105911_img_5eb0a1a90656d.jpg)
Other showcase pieces included a thermoforming tool for an aircraft interior panel made with THERMOCOMP AM EC004XXAR1 (based on ULTEM with a 20% carbon fiber reinforcement) on an LSAM from Thermwood, as well as high-temperature autoclave tooling for aerospace and a shipping vessel ventilation grill made with CNC Bárcenas’ Super Discovery.
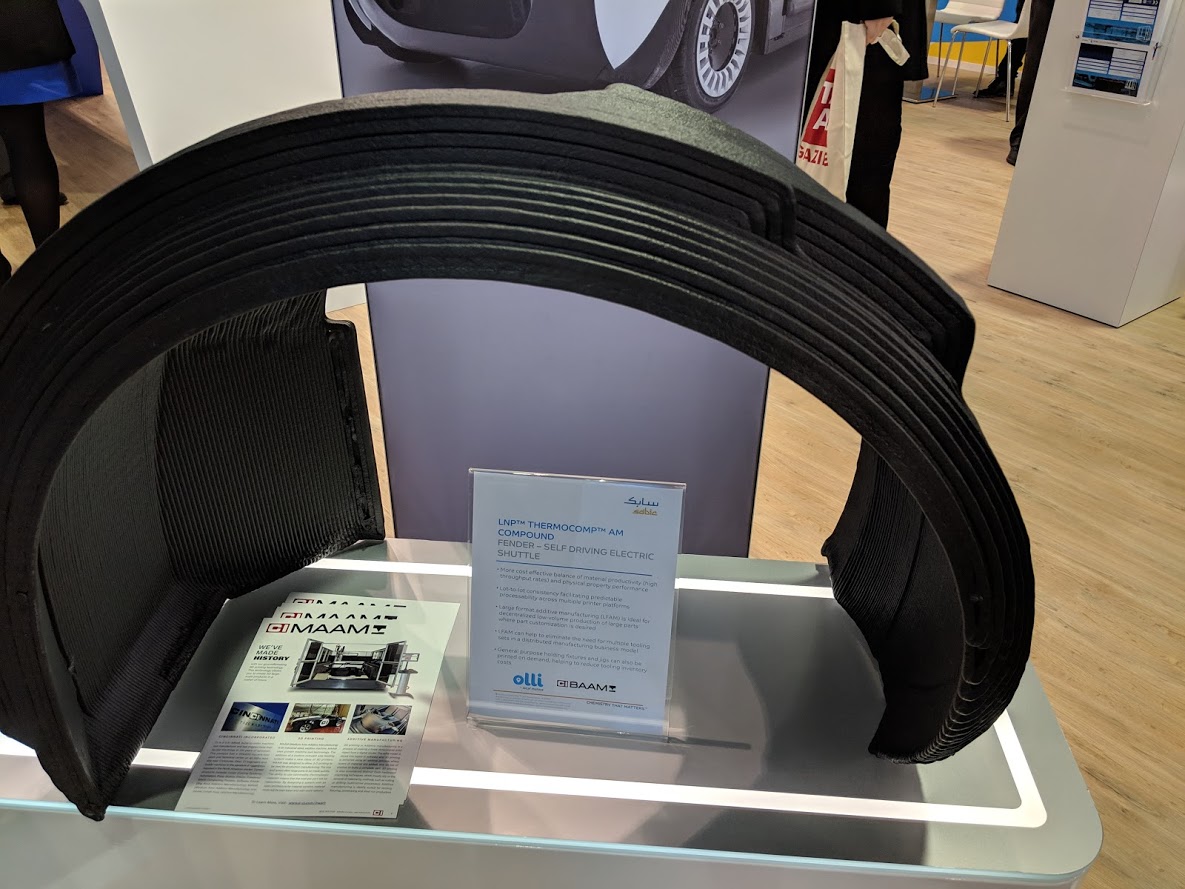
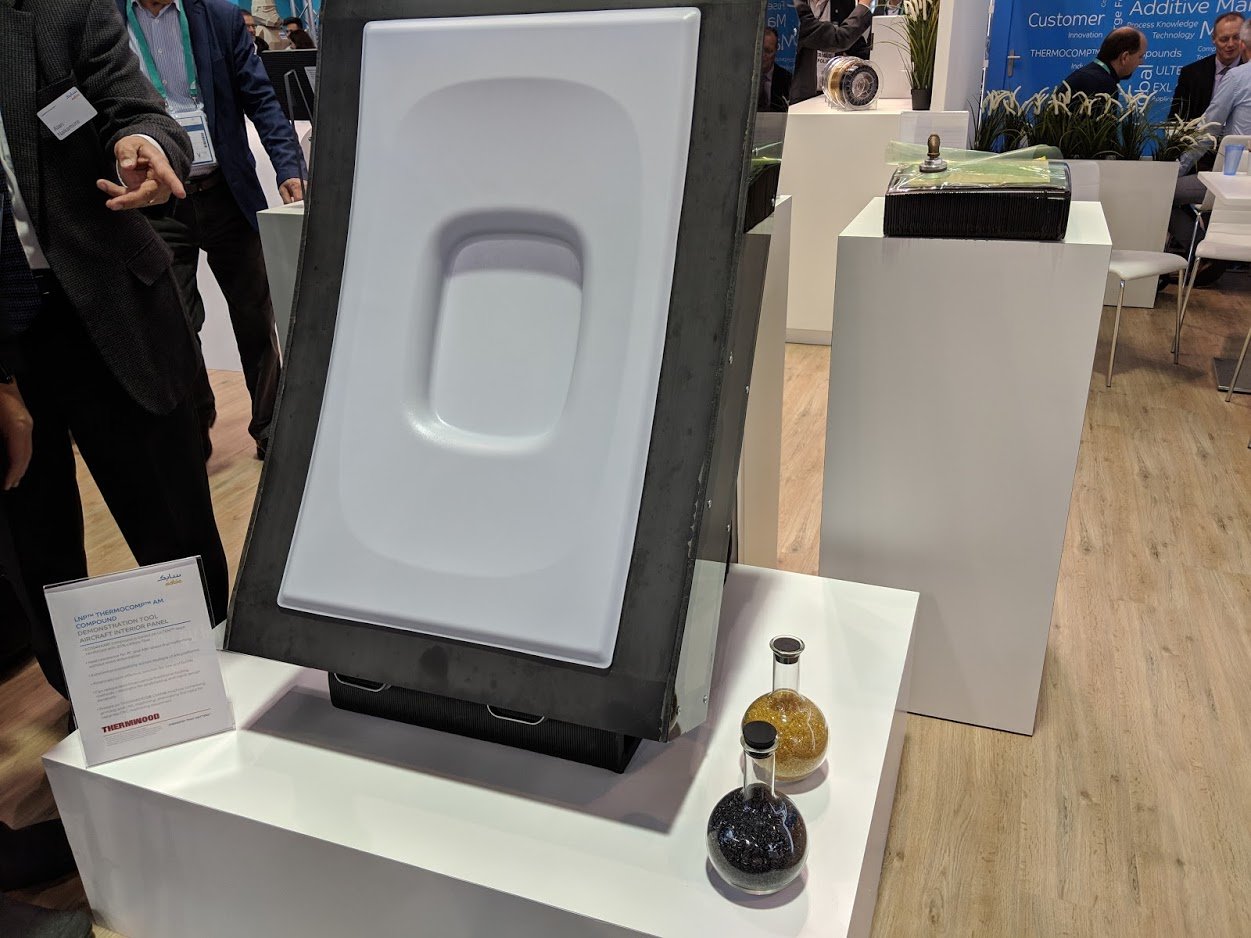
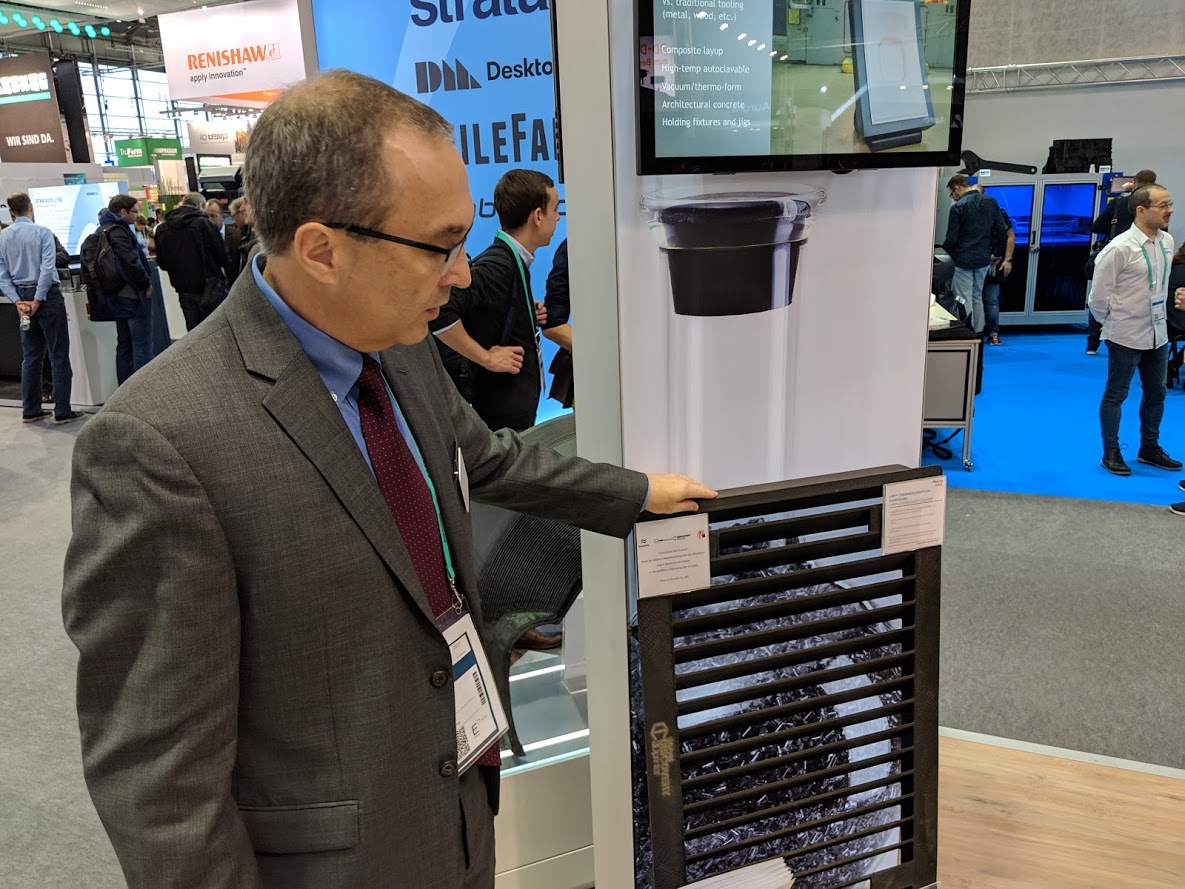
SABIC’s strong showing at formnext left me with the feeling we have plenty more to look forward to in terms of material variety suited to fit a broad spectrum of industry needs as the massive chemicals company continues to focus on additive manufacturing.
Via SABIC
An inventive designer has developed a method for producing 3D paper objects using recycled paper and 3D printed molds.