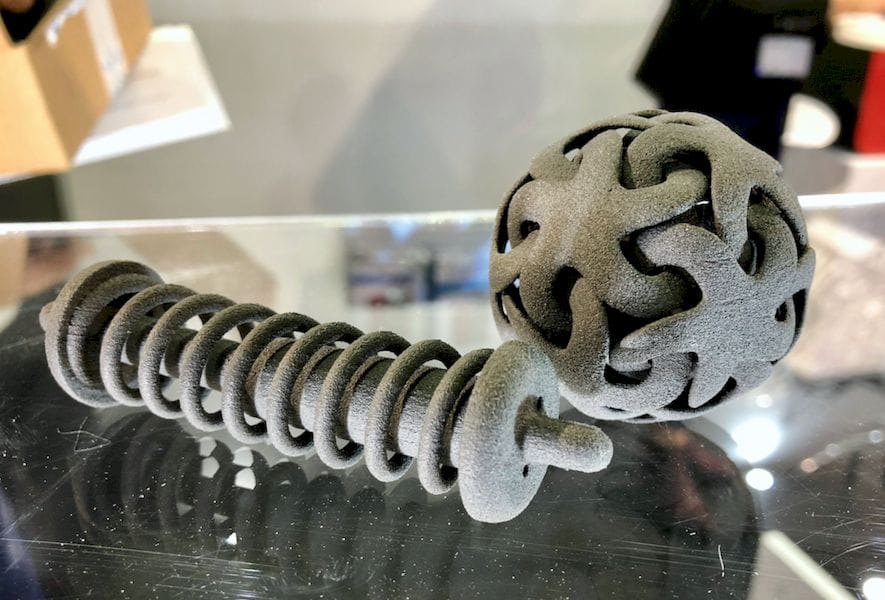
Sinterit has been improving their inexpensive desktop SLS 3D printer.
The Lisa, as it is known, is perhaps the least expensive desktop SLS 3D printer you can obtain, at a cost of only €4,990 (USD$6,000). This price is massively less expensive than traditional commercial systems available that can cost 10X as much.
These systems are typically used to 3D print strong nylon objects in very good resolution, and can produce production parts as well as prototypes and artwork. However, Sinterit explains to us that the Lisa is usually purchased by academic institutions and small to medium companies for prototyping.
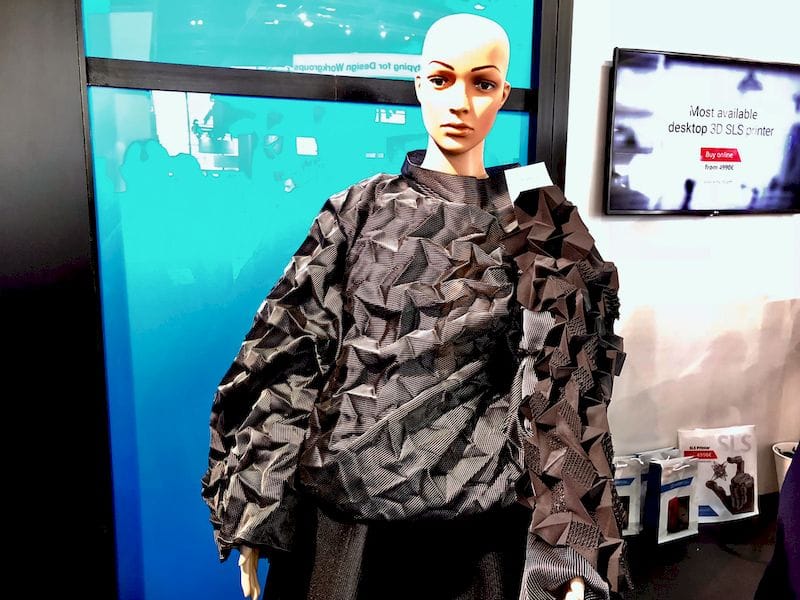
You can 3D print some very interesting items with the Lisa, such as the nylon 3D prints at top, as well as components of this interesting fashion item. If you look closely, you’ll notice that the left arm has a 3D printed section. This is an example of mixing 3D printing and fabric to create an unusual artistic fashion piece.
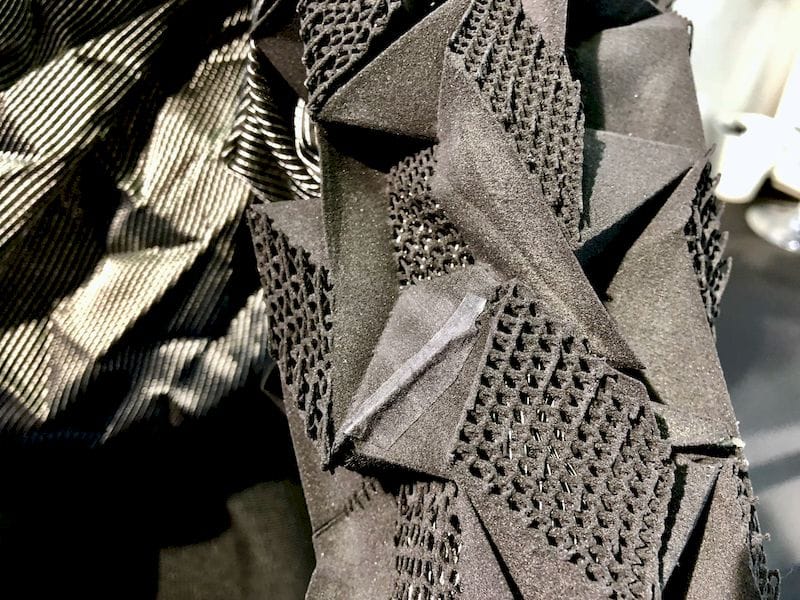
The company introduced the system about two years ago, but in the past year has introduced a number of improvements to the Lisa.
They’ve done some silent upgrades to the system to incrementally improve the quality and make prints more durable, which are all good things. They’ve also been continually refining their software, which drives the system. One of their prime goals is to make the system easier to use, which should be of great interest to the market they’re addressing.
When Sinterit introduced the machine it was certified only for PA-12 nylon powder material. Since then they’ve introduced a second material, “Flexa Black”, a flexible material that should enable many more interesting possible prints on the Lisa.
It’s not stated on their website, but we’re told they are now developing a polypropylene material to add to the shelf. The PP material should make things quite interesting for this machine, because it is a material very commonly used for production parts. Thus a designer could 3D print a prototype in the exact material they intend for the production version. Sinterit explains they are testing this material now.
In fact, they are apparently working on “many materials”, but intend on releasing only those which work properly in their machine as a result of their testing. Thus we may see the company announce the availability of additional materials in the future.
Their strategy appears to be to convince those using desktop extrusion-based equipment to convert to SLS, as it does offer a number of advantages. The prime reason for conversion likely is the fact that SLS 3D printing requires no support structures as the powder layers support loose portions of the print.
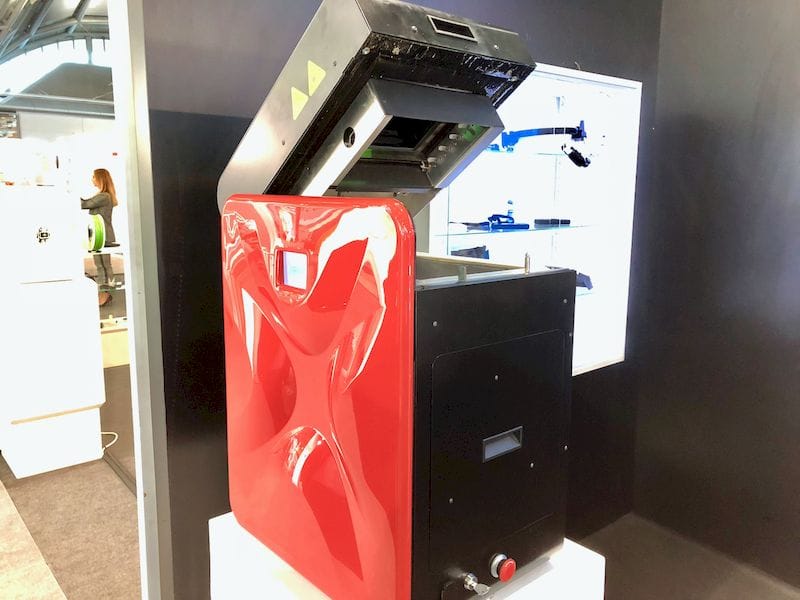
SLS also provides somewhat better surface quality than filament extrusion, although it’s not quite as good as you’d find with SLA approaches that use finely focused lasers to fuse photopolymer resin. But then, SLS can produce objects in very strong nylons, whereas you cannot easily do that with SLA.
With these benefits, it seems that converting to SLS may be an easy decision, unless your budget allows only extremely inexpensive filament-based desktop equipment.
Via Sinterit