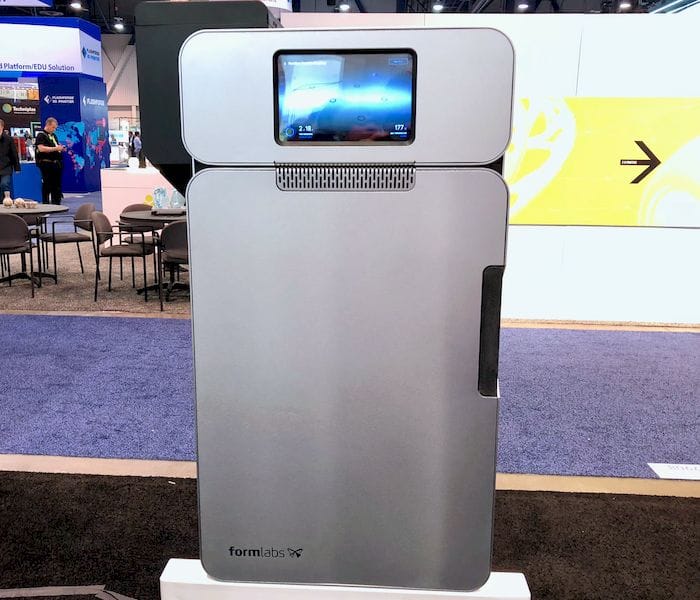
You couldn’t get a company farther from its roots than Formlabs has progressed.
We had a visit with the company, and spoke to their CEO, Max Lobobsky at CES about the changes the company has undergone from its humble beginnings in a Kickstarter launch years ago, where they attempted to address the then-burgeoning world of desktop 3D printing.
Since then, consumer interest in desktop 3D printing has abated considerably, forcing 3D printer manufacturers to shift their focus elsewhere. And wow, has Formlabs taken this strategy to heart.
Yes, they still sell the versatile Form 2, but it seems they now have additional goals that center on industrial markets. This is evident in three developments they’ve recently undertaken.
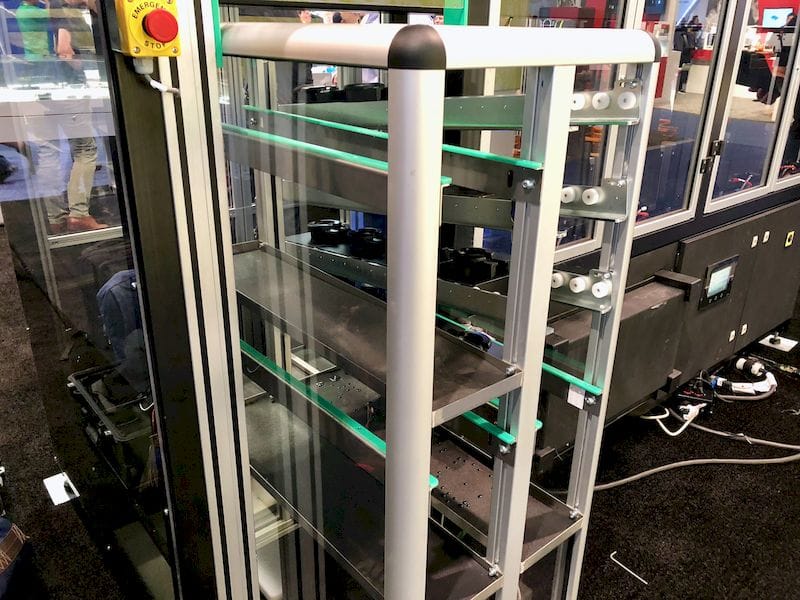
The first is the Form Cell, a system for automating 3D printing. Essentially it is a robotic and software system that manages a supply of print plates for Form 2’s. Here you can see the input hopper on the Form Cell, where they are taken to and from participating Form 2 3D printers as print requests arrive and prints complete.
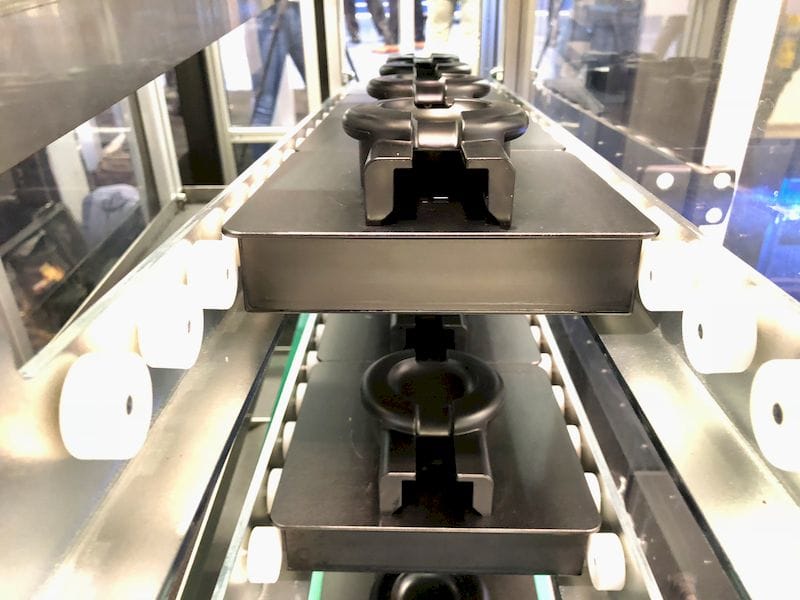
This device transforms the otherwise standalone prototyping-ready Form 2 into a small manufacturing system, capable of punching out as many objects as you want.
The second development was the Fuse 1 SLS 3D printer (shown at top), which can produce nylon parts at a very low cost. It’s not a lot different from far more expensive systems that have been available for years from other vendors, but is priced in a very different way: only USD$20K.
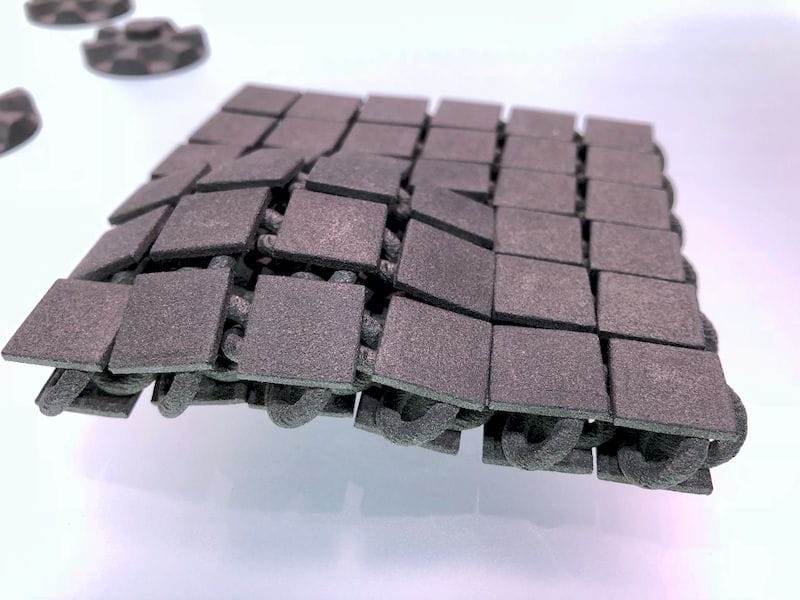
This device produces objects that can be considered production-ready, as the nylon material is far stronger than anything you’d get from SLA machines, and frequently from plastic extrusion machines as well.
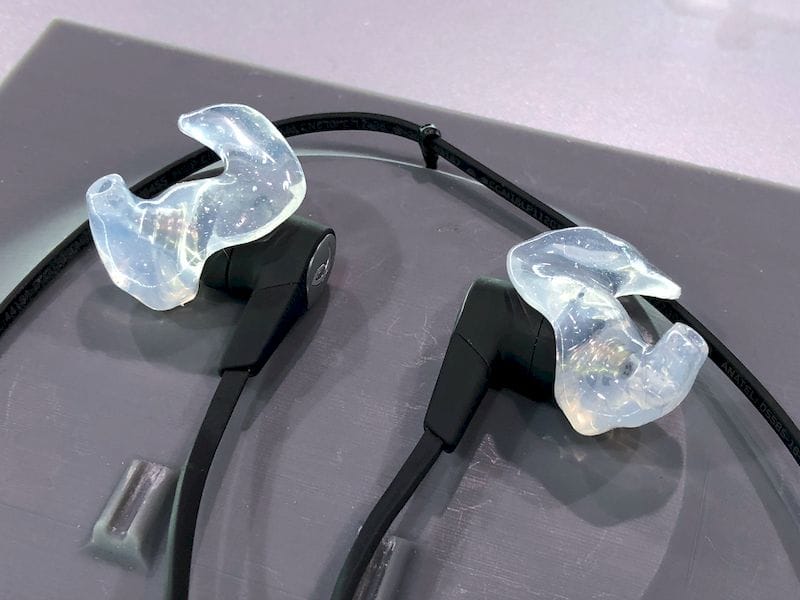
Finally, Formlabs demonstrated an interesting manufacturing partnership at CES. With 3Shape, a vendor of 3D scanning services, they’ve organized a system in which a customer can have their ear 3D scanned using a specialized handheld 3D scanner. This 3D scan is then digitally transformed into an earbud 3D model, which is then 3D printed on Formlabs 3D printing equipment.
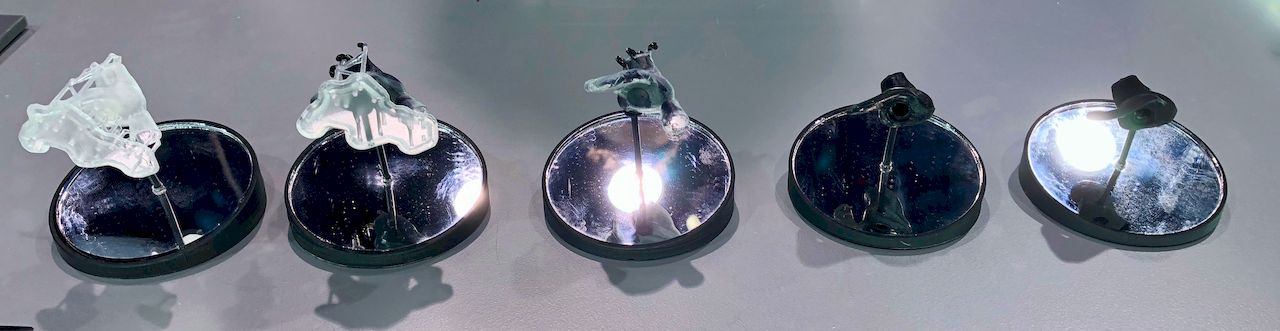
Actually, they 3D print a mold into which body-safe silicone is injected to form the final earbud. I presume this will persist until Formlabs invents a resin that can perform in a similar manner.
The idea here is to produce a highly customized earbud that matches only the customer. In fact, only one of the customer’s ears. This concept puts several technologies and services into a unified series to create a usable product for a customer.
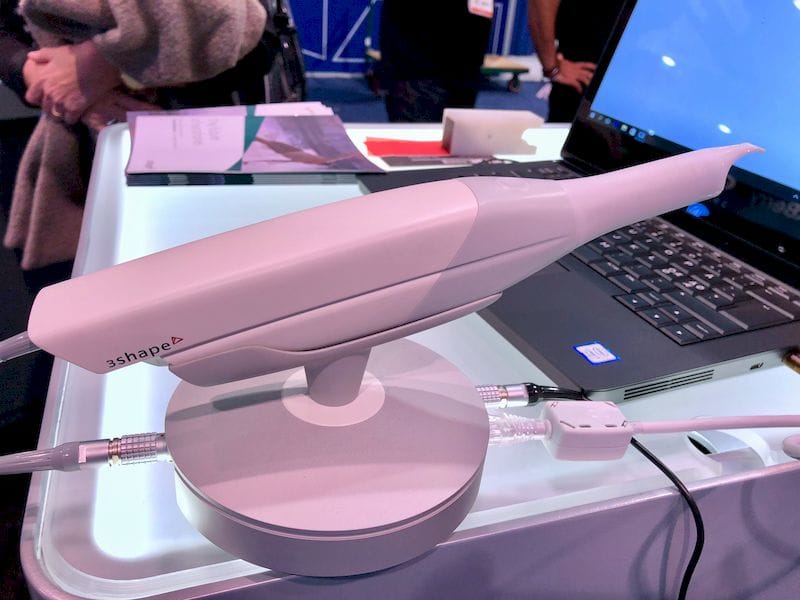
While it’s merely a demonstration, one could say the same thing about the Form Cell and the Fuse 1. These are going to be real products, and so is the mass customization concept from Formlabs.
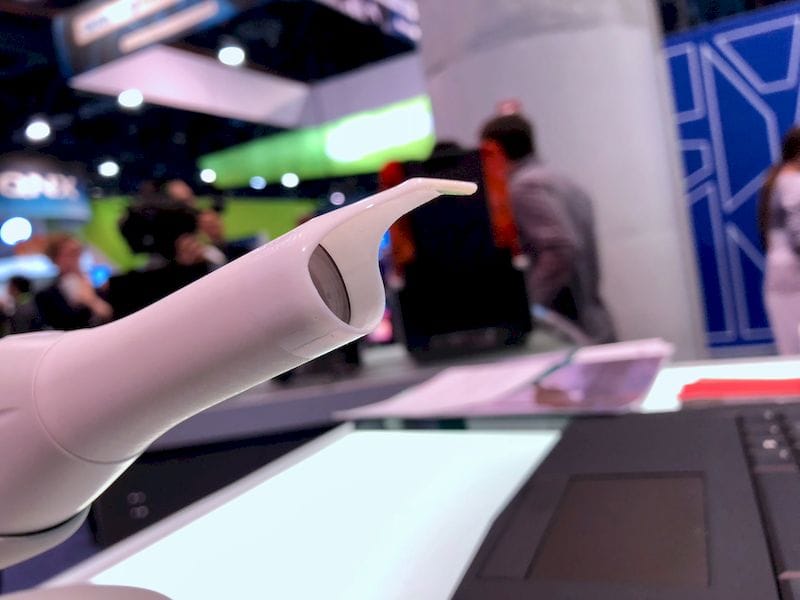
There are countless examples of personally customizable items possible and by demonstrating this concept, Formlabs could attract new industries to the use of 3D printing.
And for us, this means we could gain access to a number of customizable products we could never have imagined.
What do all of these announcements mean? To me it says that Formlabs has very strongly shifted towards business as its primary market for the future. We’ll see them develop even better machines and, more importantly, find practical ways for them to be used by business.
Via Formlabs