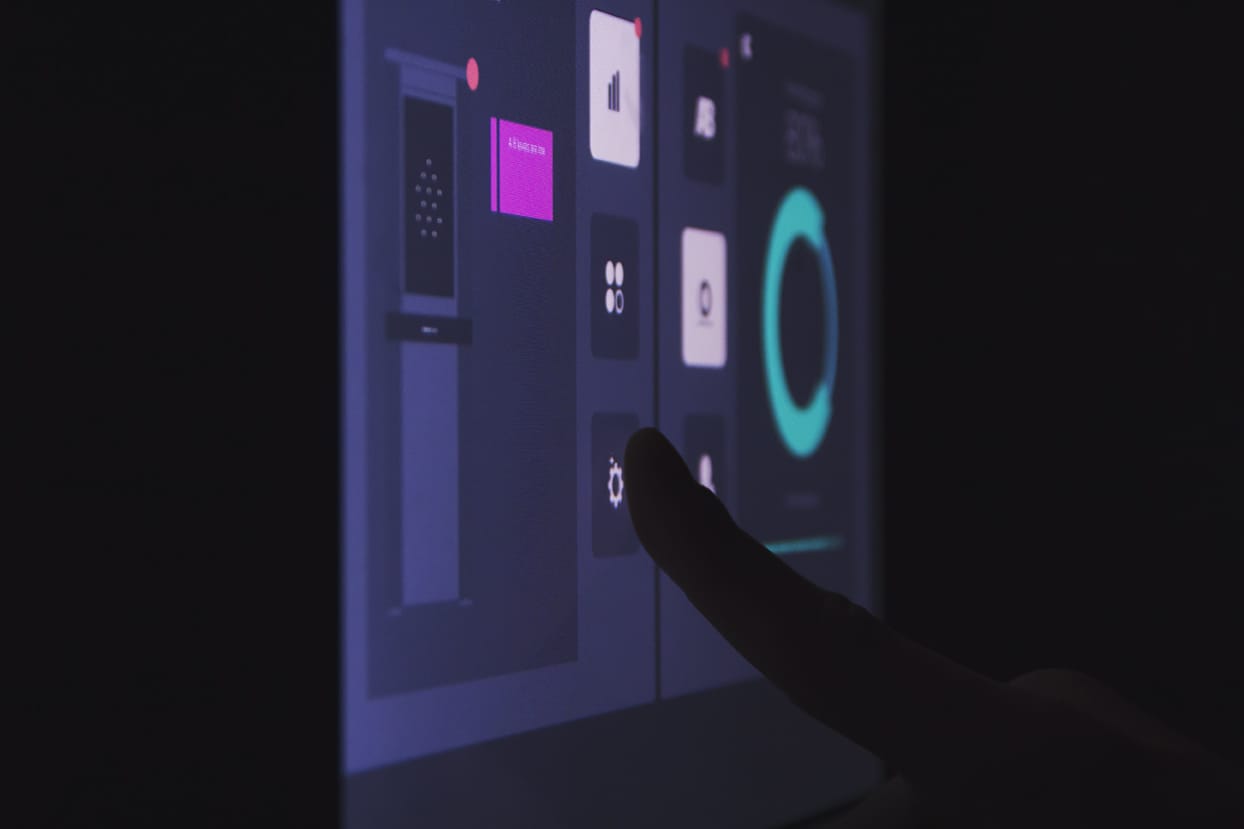
One 3D printer we’ve been awaiting for almost a year is the fascinating Orchid concept from startup Collider.
Announced in late 2016, the industrial-level 3D printer employs a unique process: sacrificial molds. While this approach could be done manually on almost any 3D printer with appropriate materials, Collider has built it all into a complete unit.
Here’s the concept: a negative mold of the desired 3D object is 3D printed on the device, which turns out to be a DLP-style resin 3D printer. The DLP printing process is said to be continuous, similar to several other advanced resin 3D printers, making it quite fast to print the mold.
https://www.youtube.com/watch?v=MCOwYaCyG2I
Then the interesting part happens: the mold is injected with a standard industrial thermoset resin, which then solidifies in the traditional manner. After curing, the mold is removed through dissolving step, although you can manually remove portions for added speed.
This is quite interesting because there are several advantages:
- The 3D printing process uses far less material than if the object itself was being produced, because you’re only printing the walls of a mold.
- The bulk of the object uses standard industrial materials that have known properties and commodity pricing.
- Parts produced are literally indistinguishable, material-wise, from injection molded parts.
- You get the advantages of complex 3D printed geometry and customization, with many characteristics of traditional making.
One issue with this approach is that the molds are sacrificial, and it remains to be seen where the break-even point in production would be for using a traditional metal mold opposite Collider’s concept. However, that’s moot if the objects you’re producing are customized.
Where this may sit well is with those seeking low volume, high quality production of parts. As long as the costs are lower than using standard metal molds, this might work very well.
However, there’s one big catch: the Orchid is not yet available. According to Collider’s website:
BETA machines ship late 2017. Customer-ready machines ship 2018.
That means someone is going to see these machines in action for real very shortly.
Via Collider