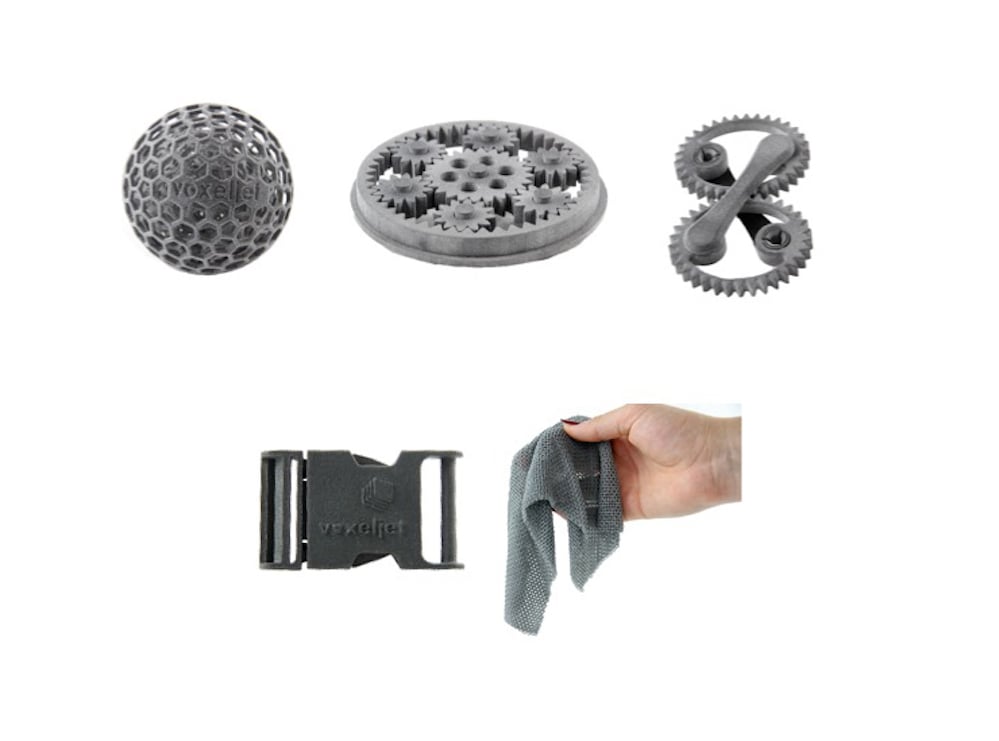
Germany-based voxeljet announced a new 3D printing process they call HSS.
voxeljet is known for their line of very large format 3D printers, which are specialized for the production of casting molds. Many companies use voxeljet technology to produce large cast metal parts, and in many circumstances, do so much more effectively than using conventional metal casting techniques.
But the new HSS technology from voxeljet actually doesn’t involve metal – or casting, for that matter. It’s all about plastic.
voxeljet has adapted their existing technology to create HSS. Their “core technology” used to create large casting molds involves jetting binder on a powder surface, which hardens to form the mold. Now that same binder jetting technology can be used to create functional plastic parts.
Here’s how it works: a flat layer of plastic powder is applied in the usual manner. A toolhead selectively jets liquid binder on to the powder surface.
Now the interesting part happens: the binder is designed to be highly sensitive to infrared light. When a layer is jetted, an infrared light source blasts the surface, whereupon the binder heats up. The heat is sufficient to melt the powder to which it was applied, fusing the plastic powder into a solid layer and binding it to those underneath. This graphic illustrates the process:
This is a very interesting approach, as it should be able to produce very strong plastic parts more efficiently than laser-based systems that must traverse every voxel of every layer. At top you can see some sample parts produced using HSS.
Another interesting aspect is that the powder-based nature of HSS should permit use of any suitable powdered plastic. While I’m pretty sure voxeljet will sell their own line of plastics, it should be possible to use virtually any thermoplastic powder in this system, opening up the possibility that HSS could produce very unusual parts.
voxeljet’s CEO, Dr. Ingo Ederer, explains more:
Our new high speed sintering process will initially be launched on our VX200 platform. With that, we are excited to offer to our customers great flexibility regarding process and machine parameters, as both can be tailored by our customers to their specific needs. We offer the option of open sourcing for materials, as our customers can choose various testing and validation services from voxeljet. ProPrint, our new and modular printing software, is available in a full access development-kit, allowing for even greater customization options. The availability and application of a wide range of 3D printable thermoplastic materials, including elastomers, makes this product line ideally suited for material suppliers, universities, and other institutions.
Thus it seems that HSS will be an option for inclusion on voxeljet’s line of large-format 3D printers. This is quite an interesting development because of the incredible size of the voxeljet 3D printers.
Their vx4000, for example, has a build volume of 4 x 2 x 1m (yes, meters), while the first system to use HSS, the VX200, has a build volume of 300 x 200 x 150 mm.
I’m wondering if this process will be applied to their larger systems, beyond the VX200. If so, it would then be possible to 3D print enormous plastic parts at efficient costs. One possible issue facing voxeljet could be the control of the heating. The amount of heat collected by a build chamber during printing could take some time to cool down, limiting the throughput of HSS.
This is also a challenge for HP, who use a somewhat similar process. However, they overcome the difficulty by creating a removable build chamber, allowing you to continue printing using a second build chamber while the first one cools down. It’s not clear if voxeljet will go this route for their larger units.
However, for now HSS will only be available on the relatively smaller VX200 system.
Via voxeljet (Hat tip to Nick)