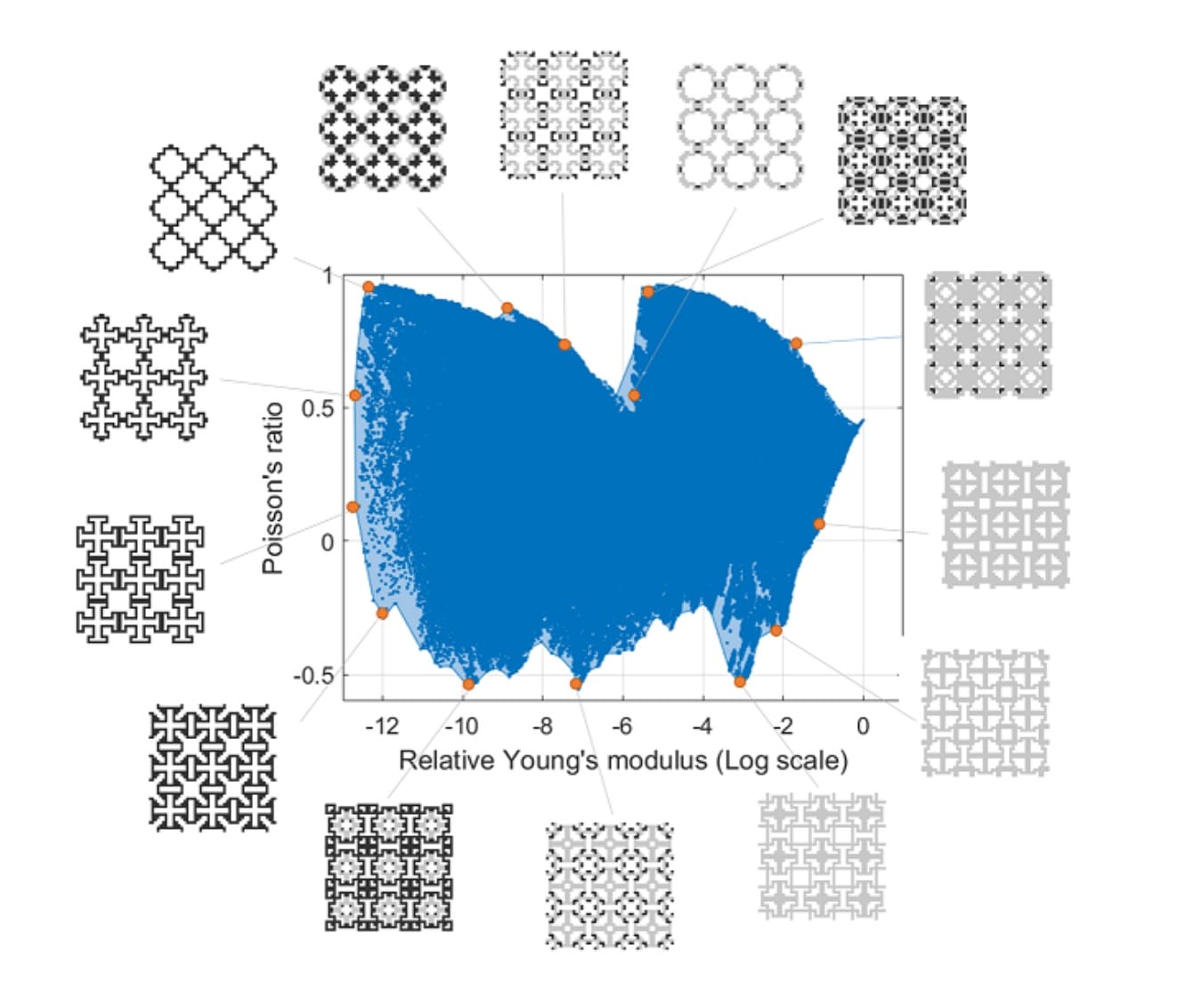
Researchers from MIT have developed what appears to be a revolutionary 3D design system that could enable far more effective leveraging of 3D printing technology.
The work attempts to develop an alternative means of optimizing structure and material distribution in 3D objects. Traditionally this is done through very complex and computationally heavy algorithms that in practical terms have limits to the complexity of an object.
This type of analysis, if scalable, would enable highly complex objects to be created that provide the most function possible for the least amount of material. But up until now, this has not been achieved.
The new work proposes a rather different approach in which they develop the concept of a “microstructure”, which is a collection of voxels exhibiting a particular engineering property. For example:
Microstructures made of alternating layers of soft and stiff isotropic materials exhibit an anisotropic behaviour as they are able to stretch more easily in one direction that in the others.
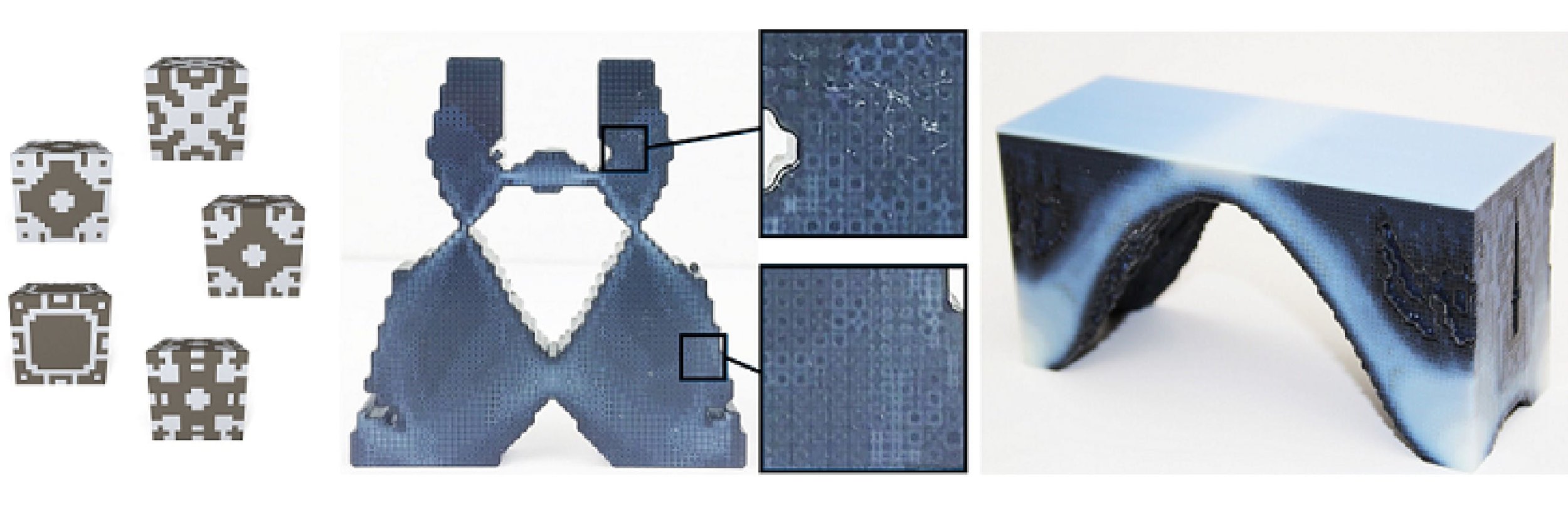
Think of this like a kind of microscopic “building block”. There are many possible variations, as you would expect, but the research team found a way to compute many different variations to build up a library, or “gamut” of possible microstructures.
Now imagine that this menu of building blocks can be used to construct a complex object, by selecting the appropriate combination of microstructures that provide the desired mechanical (or other) properties for each section of the object.
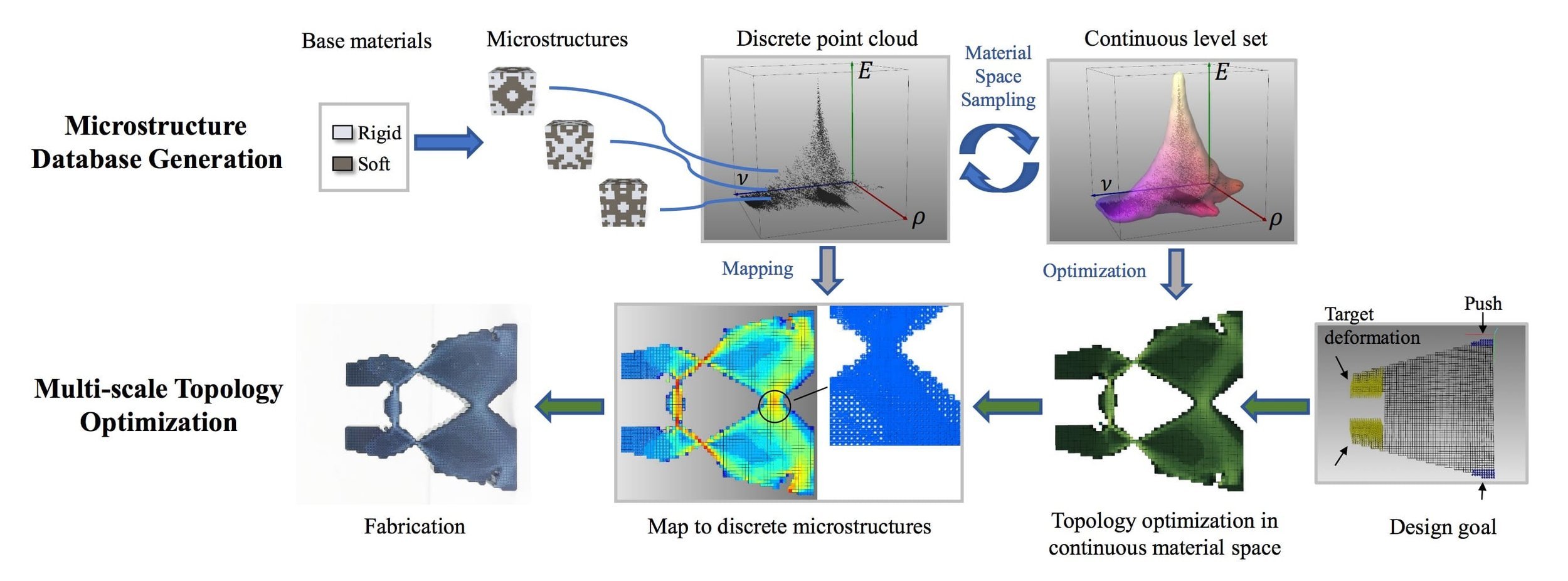
That’s what their software does: it converts the optimization problem into one that’s more solvable by using a series of discrete microstructures. Apparently they are able to compute models efficiently containing billions of voxels! They explain:
We present a fully automatic method for computing the space of material properties achievable by microstructures made of a given set of base materials.
We propose a generic and efficient topology optimization algorithm capable of handling objects with a trillion voxels. e key of our approach is a reformulation of the problem to work directly on continuous variables representing the material properties of microstructures. is allows us
to cast topology optimization as a reasonably sized constrained optimization problem that can be eciently solved with state of the art solvers.
We validate our method on a set of test cases and demonstrate its versatility by applying it to various design problems of practical interest.
So far they have 3D printed examples of parts generated from this process on conventional 3D printers, including the common Stratasys Objet Connex500 using only two different materials, their rigid clear and flexible black resins.
I find this development quite exciting as it opens up the possibility of 3D printing vastly more complex organic structures that offer surprising capabilities. It’s possible some industries would find such 3D printed parts essential and revolutionary, potentially changing their industries forever.
But for now, this is merely research. But it sounds sufficiently promising that we may see this approach bundled into practical software in coming years.
Via Arxiv (PDF)