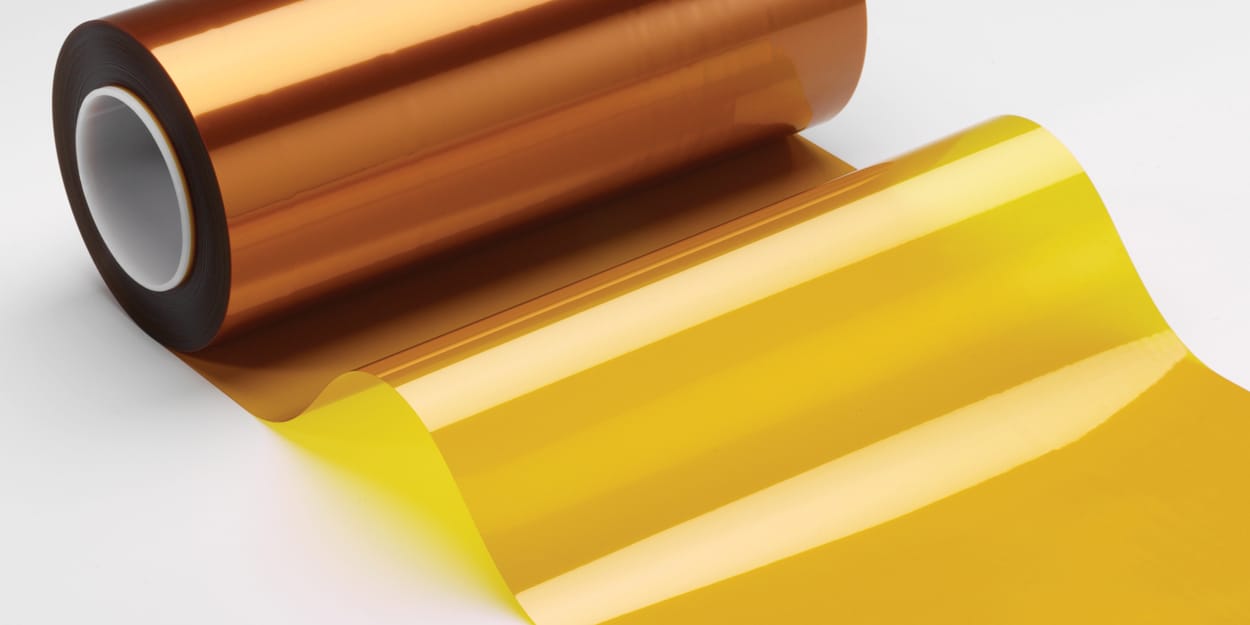
There are two popular surface adhesion treatments for desktop 3D printers, but which is right for you?
The surface adhesion problem has plagued desktop 3D printers using extrusion techniques since they emerged in 2008-9. The issue revolves around whether the print will become dislodged or warped during printing, either corrupting the print’s geometry, or causing a complete print failure. The early acrylic build plates were particularly problematic.
It was learned early on that a heated print surface would greatly assist the problem, Borosilicate glass with an under-bed heater became a popular solution.
While heated glass worked reasonably well for most PLA plastics, it was still challenging to print the rather warp-prone ABS plastic. For ABS some would apply glue sticks or “ABS Juice”, a liquid mix of acetone and dissolved ABS to the glass for extra adhesion.
But these solutions worked partially (glue) or sometimes too much (ABS Juice).
Another solution is Kapton tape. Kapton is a Polyimide film developed over 50 years ago by Dupont chemists, and has been used in industry ever since. It’s most notable use has been as a thermal insulating blanket for the Apollo lunar landers.
But it’s also been used as an adhesive surface for 3D printing, as it was discovered that the substance can stick to ABS when sufficiently heated. Typically a wide tape layer would be applied to an otherwise normal 3D print surface.
However, while it did provide a better surface for adhesion, it wasn’t optimal. Kapton tends to wear out relatively quickly, requiring replacement. Often Kapton tape on print plates would get nicked or cut by aggressive 3D printer operators, hoping to scrape off a print. For this reason you would often find a large roll of Kapton tape near the 3D printer.
More recently PEI has become a more popular adhesion treatment, as it offers some advantages.
One advantage of PEI is that it sticks very well to both PLA and ABS plastics, but its major advantage is that it is far more durable. Put a thin slab of PEI on a print plate and it will last for a great many prints if cared for appropriately.
PEI surfaces are often fairly stiff, making them a lot easier to apply to a print plate than the very thin, floppy Kapton tape. I’ve often seen Kapton tape installations with bubbles and folds, left as the frustrated installers don’t bother to fix them. And with PEI, you’re not changing them nearly as often.
PEI is actually ULTEM, a high temperature plastic that can actually be 3D printed on certain high-temperature 3D printers. However, its high temperature resistance allows it to act as a print surface for lower temperature materials like ABS and PLA.
An increasing number of desktop 3D printers now come equipped with a replaceable PEI surface, making 3D prints far more reliable. For those that don’t, it is also possible to purchase third party PEI sheets and apply them to your print plate.
Printing without a proper adhesion surface? There’s no reason not to these days.
Image Credit: Dupont