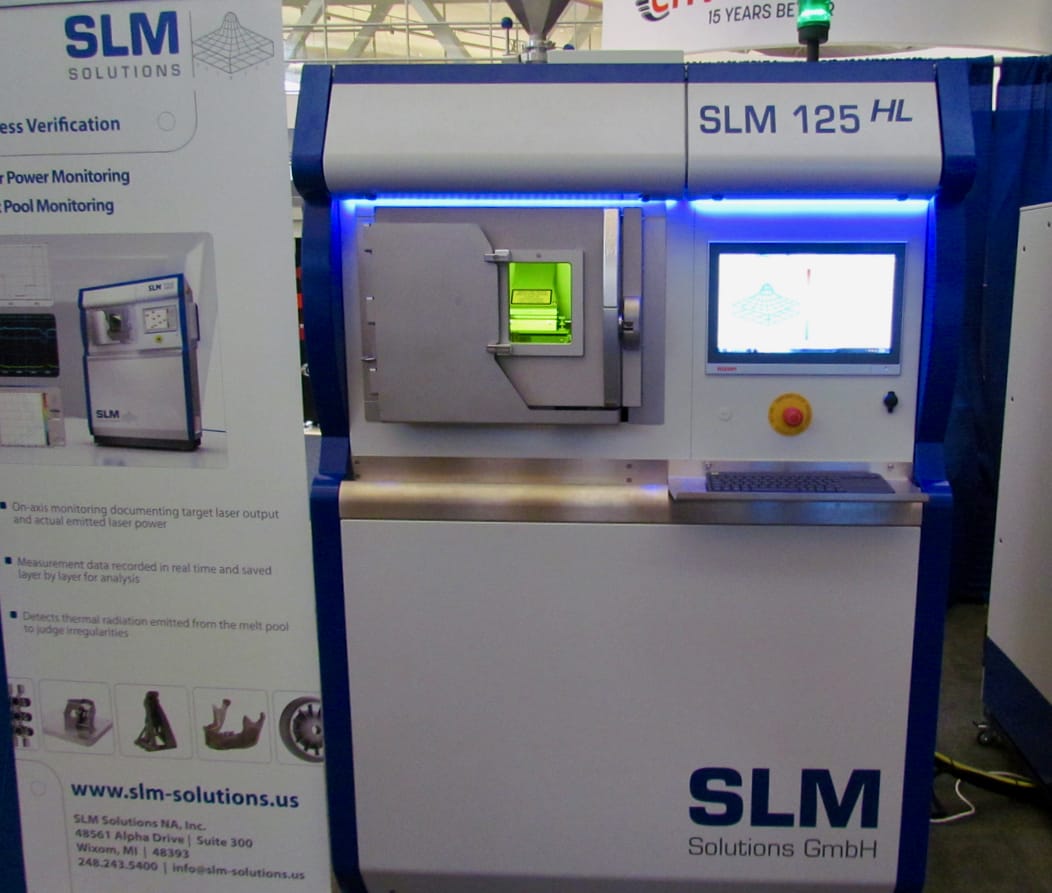
We finally had a chance to spend some quality time with representatives of SLM Solutions, and learned a great deal about their 3D metal printing advances.
SLM Solutions uses the well-known powder-bed / laser system to 3D print metal objects and they are one of the leading producers of high-quality 3D metal printers in the world today.
They offer three different models, differing mostly in build volume – and price. But we’ll get to that later.
The company has been tuning up their equipment significantly in recent months with a number of interesting improvements. Let’s take a look at some of these advancements.
There are some straightforward features, such as employing twin lasers to double the print speed, and using gravity fed bins for powder input – these can be refilled while the print proceeds.
But let’s get a bit deeper. Inside the machine SLM Solutions has installed a larger gas pump. As you may know, the build chamber must be evacuated of oxygen during print operations; typically argon gas is used. The new pump provides a way to relive soot accumulations that might otherwise pollute the print and reduce quality.
A liquid cooler is used regulate the gas temperature. As you might imagine, the inert gas in the build chamber can get extremely hot as it touches the powder being melted by powerful lasers. The cooler helps ensure the gas is at the optimum temperature for 3D metal printing.
Another very interesting feature is what they call “melt pool monitoring”. In this feature a mirror splits off a tiny fraction of the main laser beam for real-time measurement. Sensors also measure the reflection of light from the current melt pool, which moves about with the laser beam’s contact point on the powder bed.
This is quite complex to do, as the lasers can move at up to 1200mm per second, and sub-second monitoring takes place.
The idea is to monitor the quality of the printing process in real time by measuring what the laser is doing to the melt pool. Of course, at these speeds it’s impossible to stop and correct the problem, but at least you know if a print is gone awry. The print could potentially be aborted, saving time and expensive materials. This could be vital for prints that require specific quality levels, such as flight-critical parts for aircraft.
As far as we know, the SLM Solutions melt pool monitoring system is the first of its kind available in North America.
SLM Solutions has implemented this only on their single laser systems, simply because there is a massive amount of data generated by the sub-second real-time monitoring sensors. Apparently they generate around 60MB per layer, and there are many layers in some prints.
The melt pool monitoring feature is actually available as an upgrade to existing SLM Solutions equipment, so long as it’s a single laser system. The cost is said to be between USD$60-100K for the upgrade.
That’s as compared to the typical pricing of their base machines:
-
SLM 125: USD$400-500K
-
SLM 280: USD$750-1000K
-
SLM 500: USD$1-2M
At those prices, wouldn’t you want a real-time quality monitor?
Via SLM Solutions