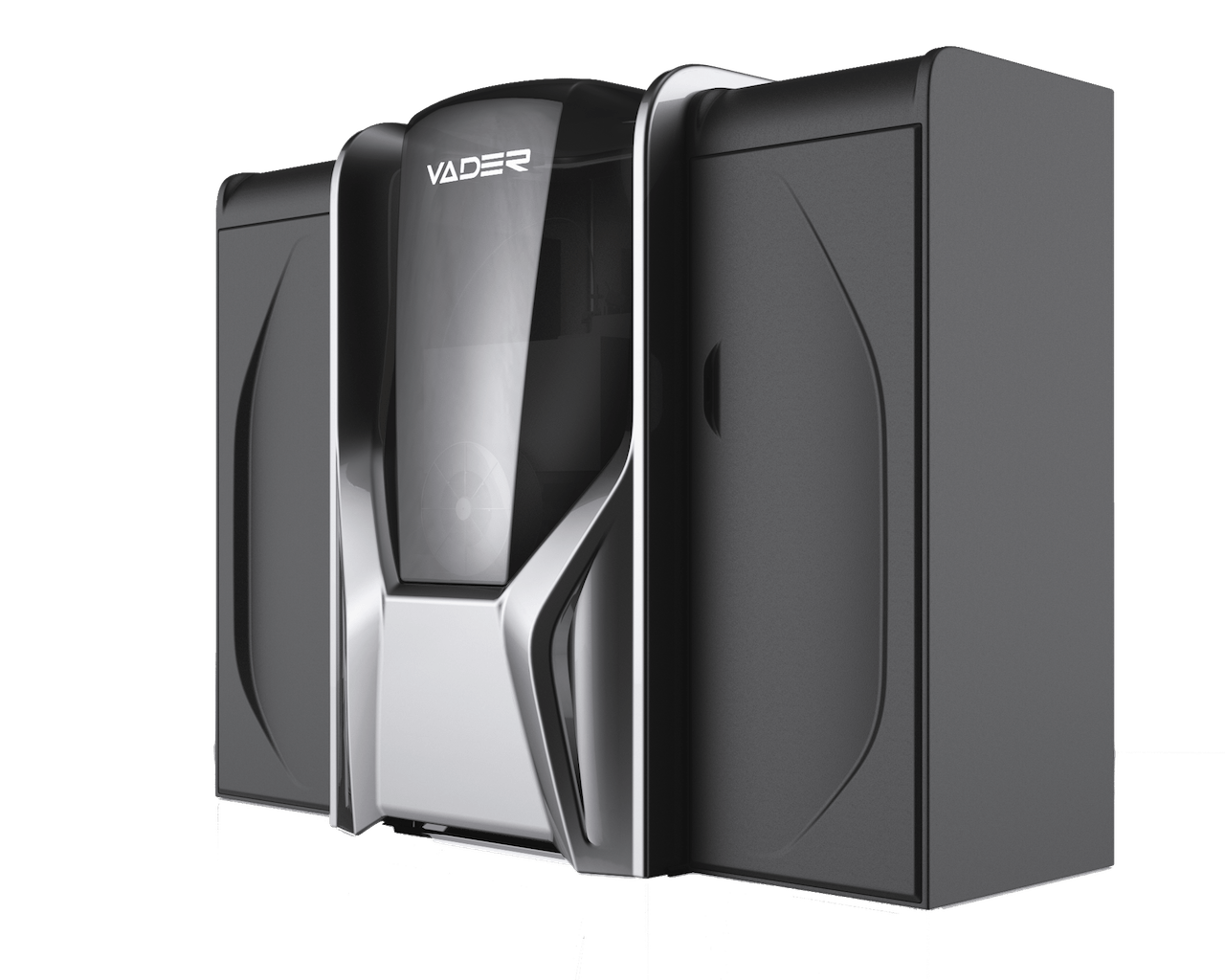
I spoke recently with startup Vader Systems, who have developed a unique method of 3D printing solid metal, which has some very attractive advantages.
It’s amazing how many different processes are being experimented with to perform 3D metal printing, and Vader Systems has one of them.
It’s a relatively inexpensive process that actually uses standard welding wire. Here’s how it works.
Commodity welding wire is pushed into a nozzle, which is heated to high temperatures using electrical resistance. The welding wire gains molten state, whereupon it is deposited by the moving nozzle onto a plane. Additional layers are added to form complete 3D objects.
This process has several advantages.
One is that the material used is a commodity; it is definitely not the ultra-expensive fine metal powder used in other processes, which can cost as much as USD$500/kg. You can get this material at low prices, such as 5kg of steel MIG welding wire for around USD$40. Vader Systems says it’s a factor of perhaps 10X less expensive. If printing many or large metal objects, this alone could save you vast sums of money.
Another key advantage is that because powder is not used, there is little need for complex and expensive powder containment systems. These might include pressurized 3D printer rooms, sealed powder handling equipment, breathing apparatus, etc. In fact, this stuff might cost more than the printer itself – but most of it isn’t necessary if you’re using welding wire.
A third advantage is that the commodity welding wire is not only widely available, but also in a large variety of standard metal combinations.
Finally, Vader Systems claims their print speed is up to 2X that of standard powder bed fusion with lasers as used by their competitors. This may be true, but many of those same competitors are coming out with machines equipped with two or even four lasers to dramatically speed up their printing rates.
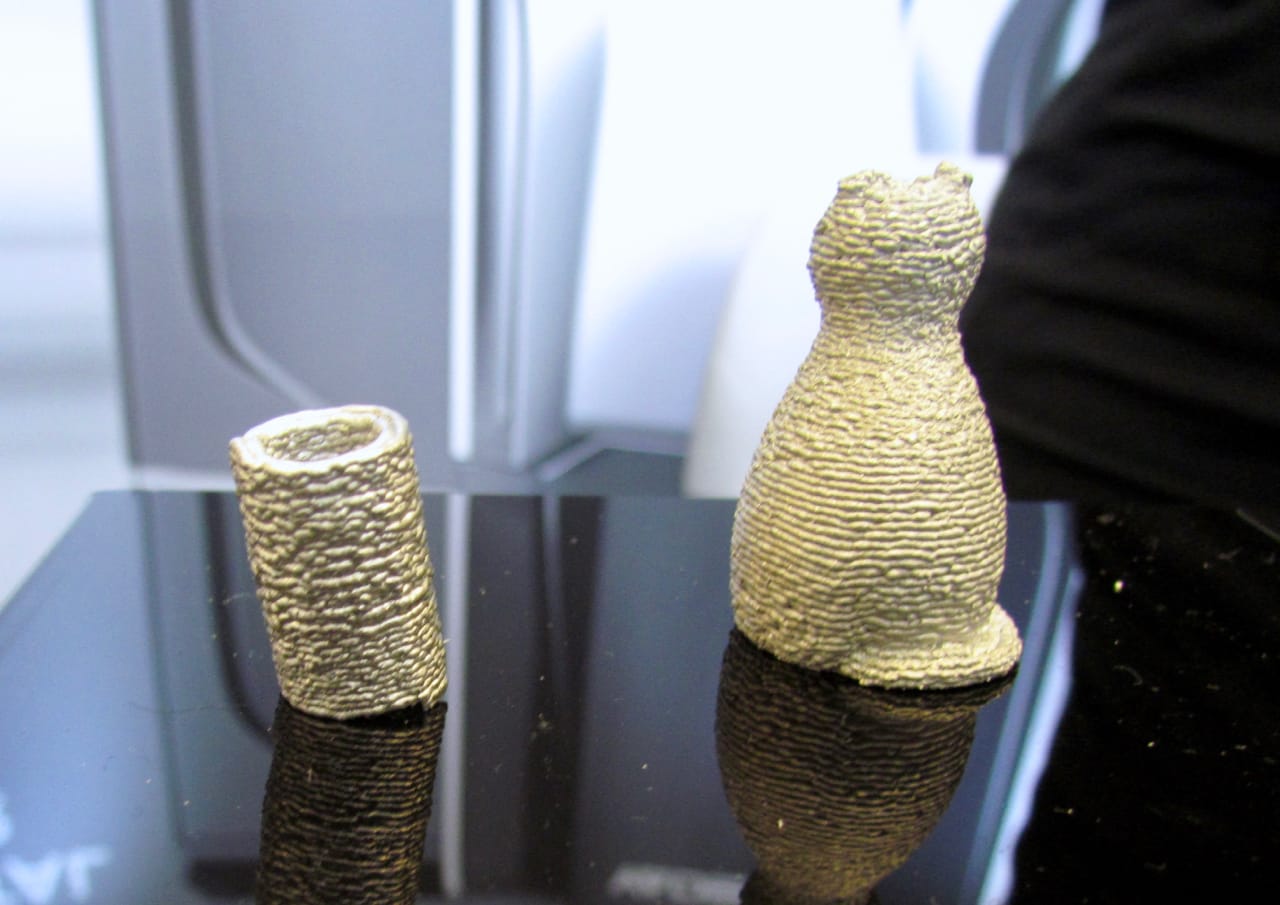
There is a disadvantage, however, and that is resolution. Here you can see some 3D printed samples and it’s clear you can see the rather coarse nature of the prints. Vader systems says their resolution is 300-500 microns, but these samples seem a bit more than that. But in some cases, particularly with large prints, this may not be an issue at all. On the other hand, Vader System’s initial machine has a build volume of only 300 x 300 x 300mm.
And it’s always possible to CNC mill completed prints to a smooth finish, although the geometry of the object might preclude CNC milling all surfaces.
As of now, Vader Systems offers only their “MK1 Experimental” device, a pre-production model. It’s been sold at least once, to the Rochester Institute of Technology, and appears to be available to any other interested parties.
They’re working to market a full “commercial” machine sometime in 2018. I’m sure there are a number of parties anticipating this machine, particularly if it’s priced right.
Via Vader Systems