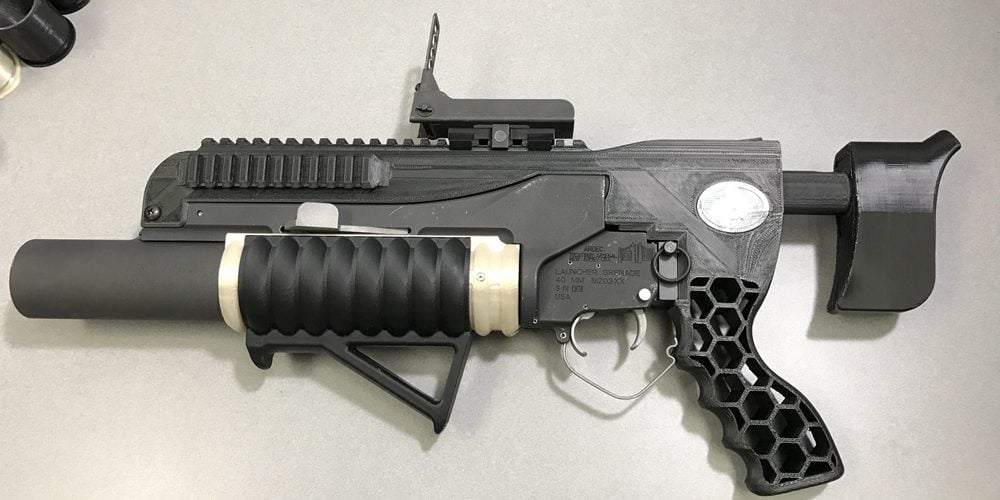
There’s been a bit of a buzz around the US Army’s announcement of an almost fully-3D printed grenade launcher, but really it’s just an experiment.
The device, with the amusing name of “RAMBO” (Rapid Additively Manufactured Ballistics Ordnance) is apparently entirely 3D printed with the exception of springs and fasteners, which can be of standard issue. They explain how it was made:
Every component in the M203A1 grenade launcher, except springs and fasteners, was produced using AM techniques and processes. The barrel and receiver were fabricated in aluminum using a direct metal laser sintering (DMLS) process. This process uses high-powered precision lasers to heat the particles of powder below their melting point, essentially welding the fine metal powder layer by layer until a finished object is formed. Other components, like the trigger and firing pin, were printed in 4340 alloy steel, which matches the material of the traditional production parts.
So it appears they were using 3D metal printers to produce the weapon. As readers will be familiar, this process is frightfully expensive and so far is financially feasible only for industries with previously high unit prices for parts, such as aerospace and dental markets.
So could this be feasible for production use? The US Army says:
The technology demonstrator did not aim to illustrate whether the grenade launcher and munition could be made cheaper, lighter or better than traditional mass-production methods. Instead, researchers sought to determine whether AM technologies were mature enough to build an entire weapon system and the materials’ properties robust enough to create a properly functioning armament.
Aha, so they were simply “seeing if it could be done”. And indeed it can, as their live fire tests subsequently determined the weapon worked correctly.
But what they’re really testing here is NOT the weapon, but instead a new method of weapons development. Like those who first discovered “Rapid Prototyping” years ago, the US Army feels they can dramatically speed up the lifecycle of weapon development in a similar manner. Prototypes can be developed far more quickly, although I suspect large-scale production would again be in the traditional manner for cost, quality and consistency reasons.
But what’s bugging me here is that the headlines may suggest to those less familiar with the technology that the US Army can now apparently 3D print usable (or “fieldable” as they say) weapons instantly on demand from some kind of magic 3D printers. That’s definitely not the case here. You can’t just put 3D metal printers out in the field – that’s silly. They require very special (and costly) environments, ancillary equipment and technicians to operate them.
The US Army is merely catching up to what many industries have been doing for quite a few years.
Via US Army