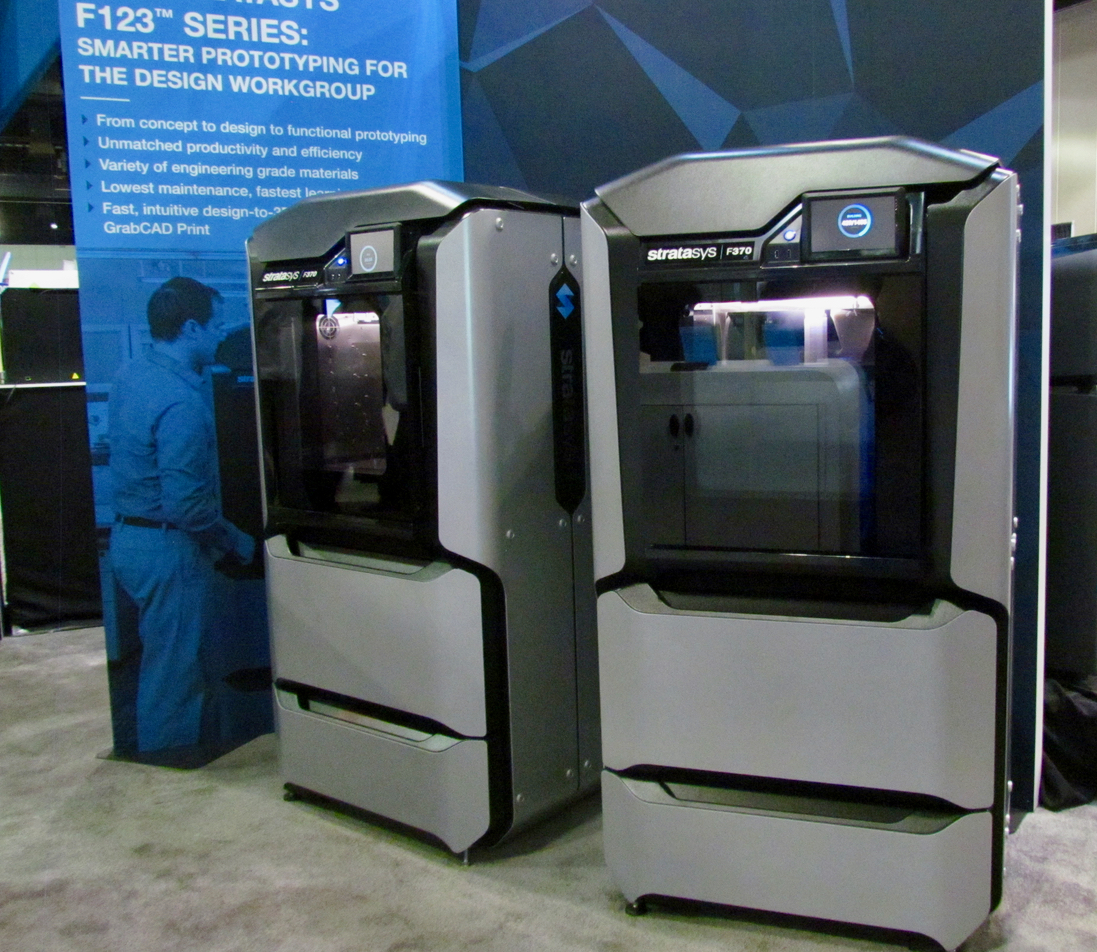
Yesterday Stratasys made what might be their biggest announcement of the year: an entirely new line of 3D printers for prototyping.
The new F123 series is intended to replace the aging Dimension line, which was announced quite a few years ago. It’s composed of three models, the F170, F270 and F370, which differ primarily by build volume.
To be clear, the F123 series is definitely not an improved version of the Dimension series or any other machine in their arsenal. No, it’s said to be entirely new machines, redesigned from the ground up.
They are true FDM 3D printers, using the classic method of 3D printing, but the design incorporates significant improvements in operational workflow, reliability and quality. And you can 3D print some new materials, too. However, they are not production machines; these are intended as “super prototyping” devices.
While rapid prototyping has been around for a very long time, Stratasys believes there’s still plenty of room to expand the market. Why? Because they still encounter companies uncomfortable operating 3D printers and associated workflows. They may be companies with less technical know-how but still could benefit from 3D printing. Those are the folks this line of equipment is designed for.
The F123 series is designed around the workflow required to go from design to final 3D print, and Stratasys has used a variety of techniques to simplify things. The say it will also be more economical, too.
The machines differ primarily by build volume, and in fact they all occupy the same frame and case – visually indistinguishable from the outside. The F170 prints within a 254 x 254 x 254mm volume; the F270 within a 305 x 254 x 305mm volume, and the largest model, the F370, within a 356 x 254 x 356mm volume. They’re all bigger than the uPrint, and the F370 is close to the volume of the Fortus 380mc, now the smallest of the Fortus line, as they simultaneously discontinued the Fortus 250mc with this announcement.
The F123 series prints 20-30% faster than the uPrint, according to a beta user of the F370.
What’s most interesting about this machine is that it can print different materials, whereas the previous equipment from Stratasys had limitations.
Print resolution is similar to prior Stratasys models: 0.005” and 0.010” layers, which Stratasys unfortunately calls “5 slice” and “10 slice”. I’d prefer they simply switch to metric and call it 0.127mm and 0.254mm as almost all other vendors do.
The F123 series prints ABS, as prior models did, and also ASA, PC-ABS (F370 only) and – get this – PLA!
These are the very first machines from Stratays that print PLA, the most popular material among desktop 3D printers. Stratasys says they want people to develop iterative designs rapidly with inexpensive materials.
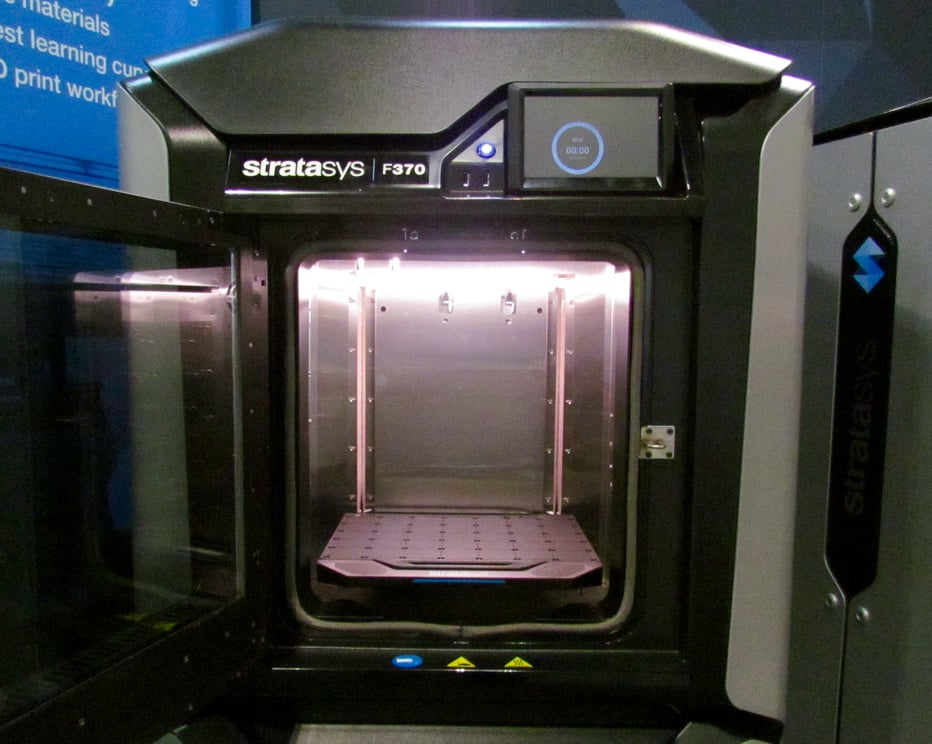
All models include two printheads, enabling the use of soluble support material for 3D printing complex geometries. But there is something interesting when 3D printing PLA plastic.
PLA, as you may know, is a very low-temperature thermoplastic, and it should be cooled very quickly after extrusion to avoid “slumps”. For this reason virtually all PLA-compatible desktop machines include a fan unit to provide this cooling.
But how does the F123 series do it?
It’s an interesting solution: to enable PLA printing, you must quick swap the model material print head to the PLA-compatible version (all other plastics are compatible with the standard print head). Then the second print head, normally used for soluble support material, is quick swapped out for a cooling unit! That’s how PLA is printed on the F123 series.
However, how do you do support when the second printhead is a cooler? The answer is that Stratasys provides software to generate breakaway supports: the supports are the same PLA material as the model itself. I’m told by beta testers that Stratasys has done an excellent job of generating supports that actually break away easily and cleanly.
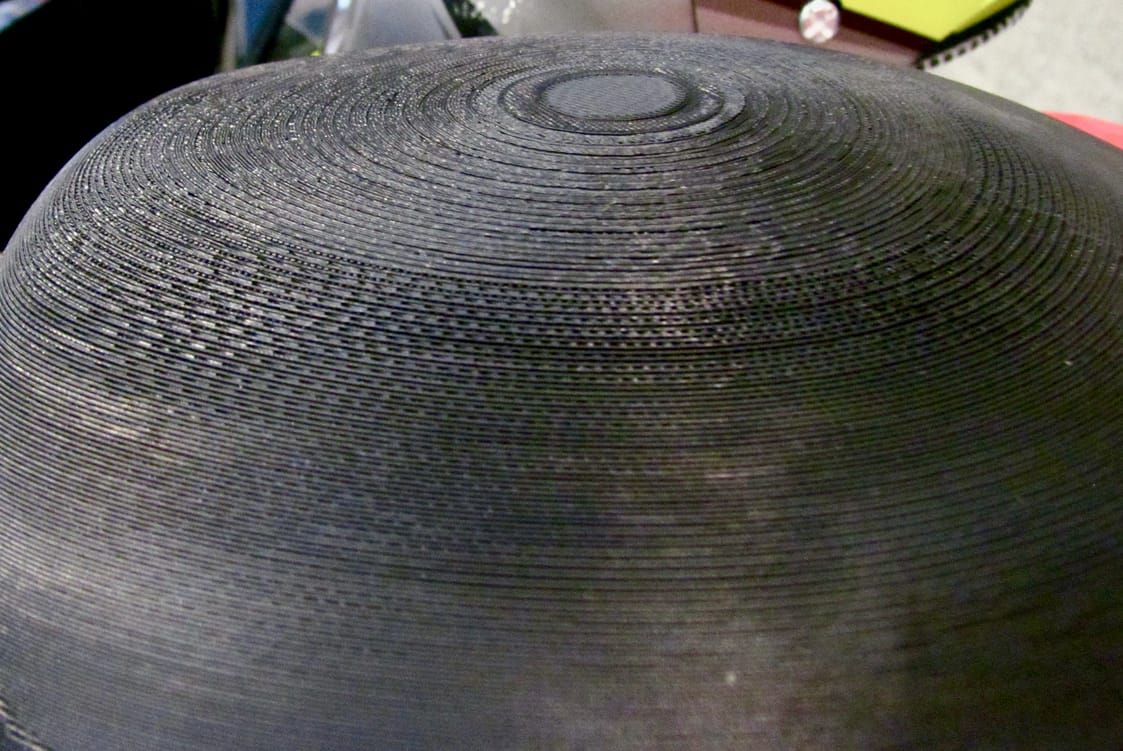
Don’t believe me? Check out the detail of this helmet top, which was printed upside down in PLA. This entire area was filled with breakaway supports, and you can see very little if any evidence support material was once attached.
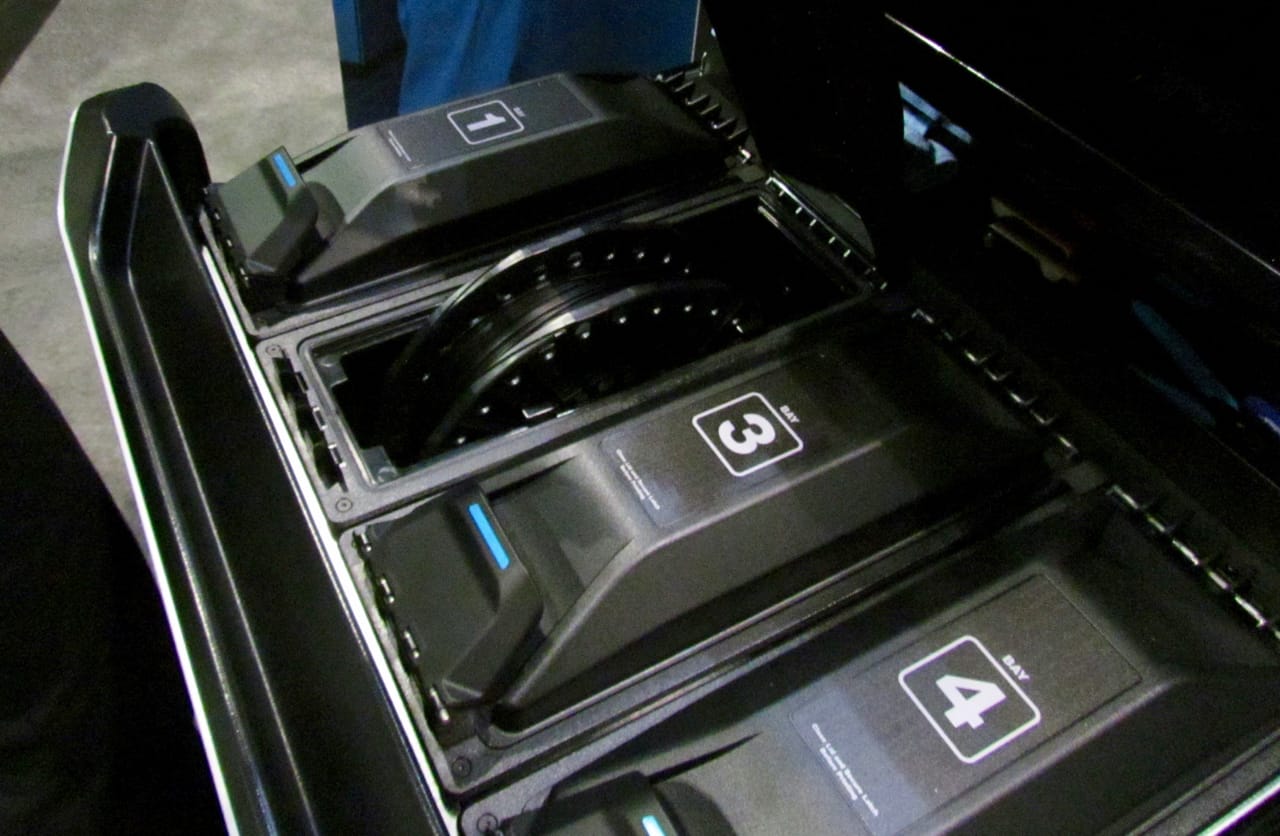
The F123 series includes a number of efficiency features to make life easier. One of them is a simplified filament system. Instead of the awkward canisters used on the uPrint and Fortus, the F123 series uses plain old spools just like everyone else. However, the spools do contain a chip on the edge that’s queried by the 3D printer to track usage and identify the type and color of material loaded.
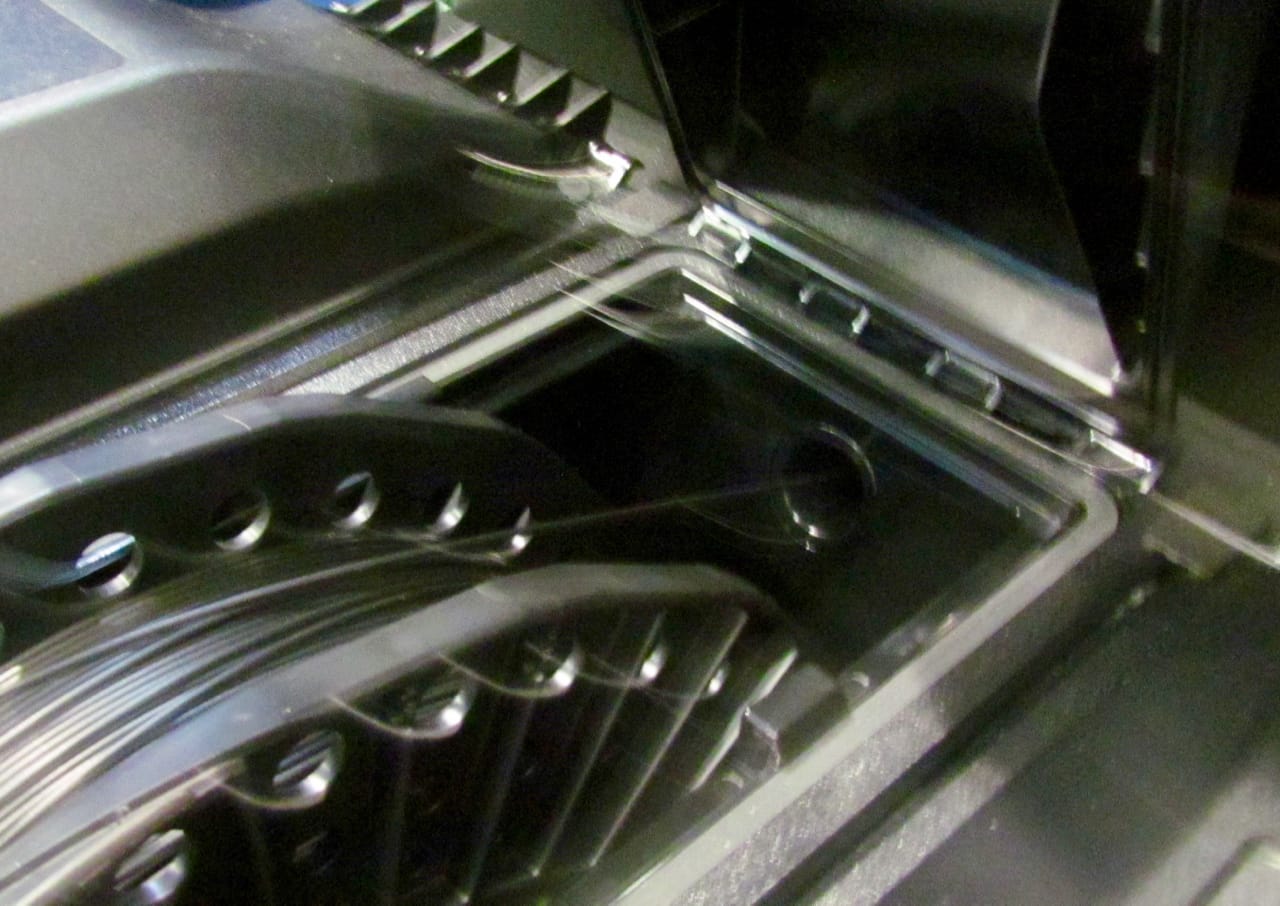
The new spooling arrangement makes loading filament spectacularly easier. They say, and beta testers concur, that you can actually swap a spool in less than a minute, 30 seconds, perhaps.
There are up to four spools that can be installed, normally two model and two support material spools. If a spool runs out during a job, the machines automatically switch to the alternate spool and continue printing. Sounds like a Fortus feature, but it’s on these less expensive units.
The software used for slicing 3D models for the F123 series is none other than GrabCAD, acquired by Stratasys a couple of years ago and now providing a very easy to use interface for those uncomfortable operators I mentioned earlier.
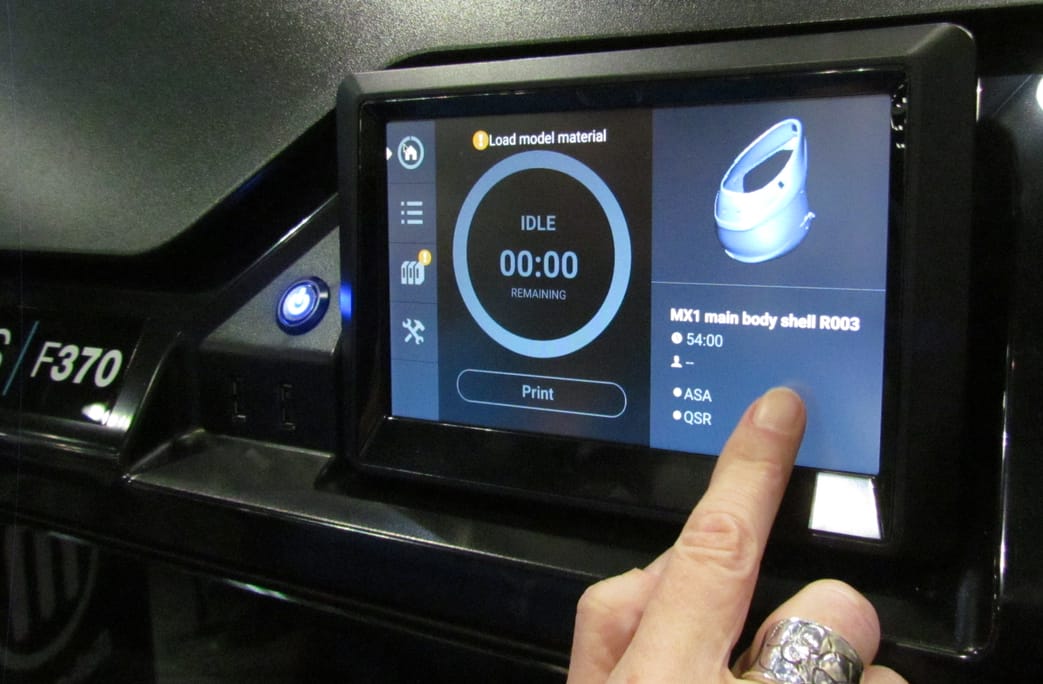
The control panel of the F123 series is also extremely easy to use. But what I found interesting is that the screen displays – and those of GrabCAD and the associated smartphone app – are suspiciously similar to MakerBot’s new MakerBot Print application that we reviewed earlier. They were good for MakerBot and they’ll be good for Stratasys.
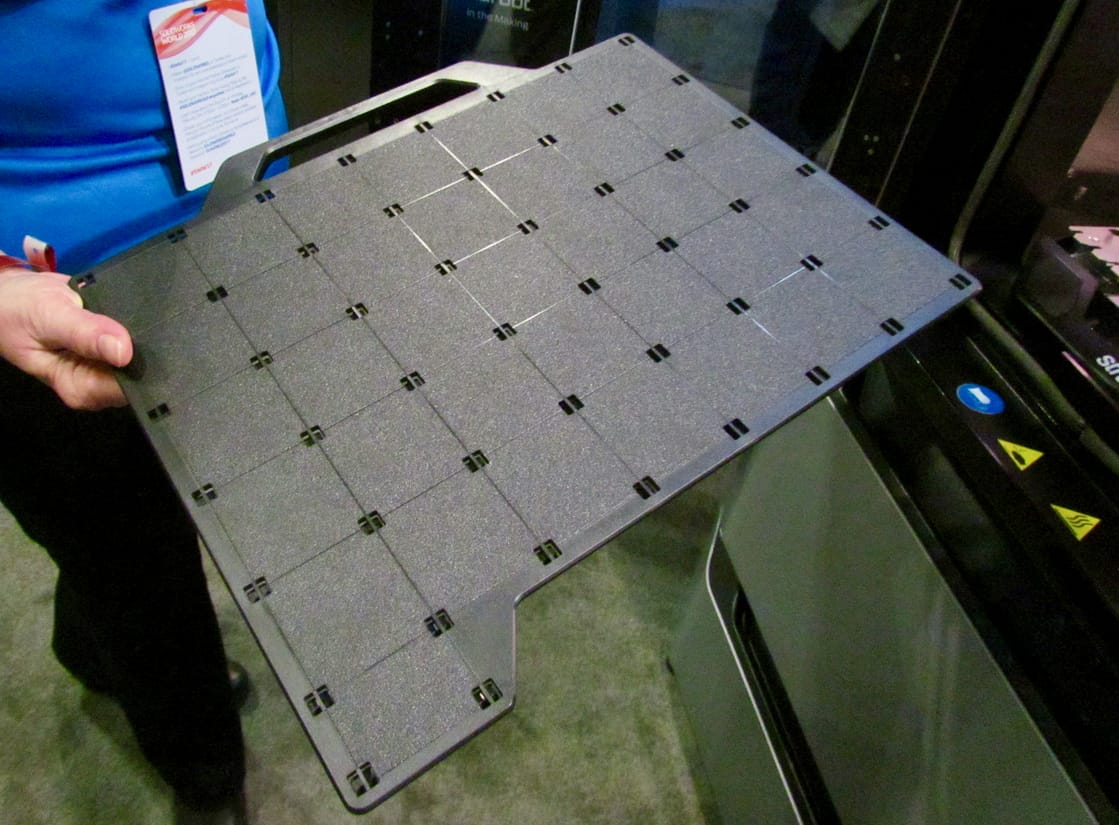
Another feature that’s eerily reminiscent of MakerBot’s equipment is the new build tray. It’s held down by a matrix of hooks, so no need for a vacuum plate.
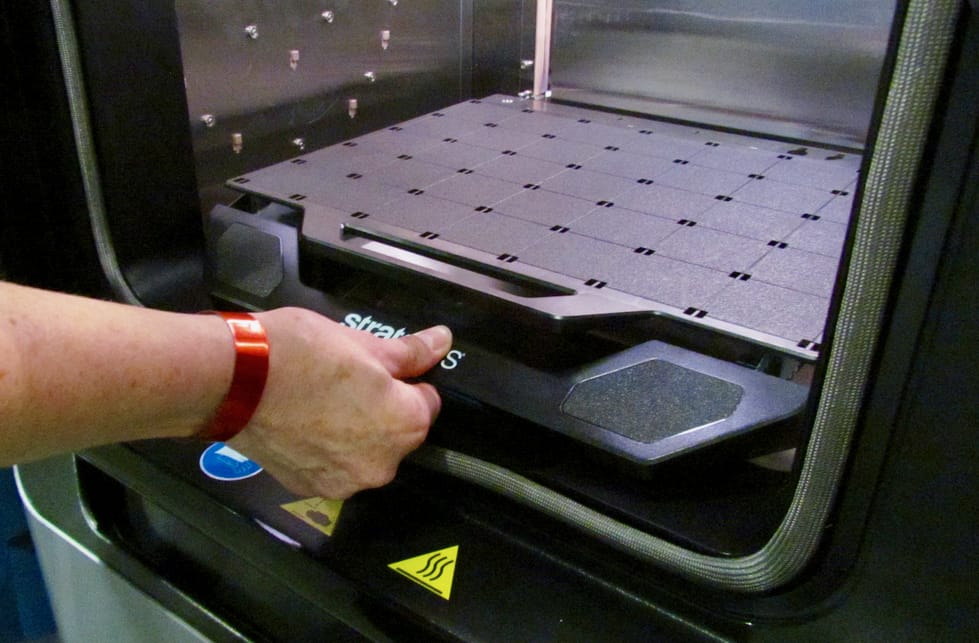
The build tray is installed and removed easily with a prominent latch that opens and closes by raising and lowering.
I’m told the build tray can be reused far more than the previous machines’ trays, which were officially for single use. The new tray can officially take 15 reprints before using, but I suspect it could be used far more if the surface area is randomly used.
I should say that the F123 series also include a camera for remote monitoring of print jobs, displayable on smartphone apps. The new series is also fully able to support workgroup 3D printing.
Users of the F370 will have the added advantage of being able to use Stratasys’ Insight software to provide delicate tuning of the extrusion path for specialized jobs.
The company also announced a new plug-in for Solidworks that permits “drag and drop” functionality between it and GrabCAD for 3D print preparation.
While you can invoke 3D prints through the machines’ network interface, the F123 series also includes a USB slot for private prints that should not travel over networks.
Stratasys says the machines should be the most reliable they’ve produced, having improved the designs, used new high-performance components and performed over 90,000 hours of testing on the machines.
One feature I believe is very important is the simplified installation requirements. Unlike the Fortus machines that require a constant supply of compressed air and three phase input power, the F123 series can be plugged into more typical power outlets.
The three models are available for order now and should ship in March. How much do they cost? We’re told the three models are priced near USD$20K, USD$35K and USD$50K for the F370.
I’m less certain of the materials pricing, as I received inconsistent information. One story had the price of the materials the same as current Stratasys materials per cubic inch (which is rather high, I might add), and the other story indicates the price is a bit less. I’m hoping for the latter. In any case, the spools are 60 and 90 cubic inches; larger than you’d find on a uPrint by far.
These machines generate a number of positive and negative implications for different parties in the 3D print space; stay tuned for more thoughts on this important announcement.
Via Stratasys