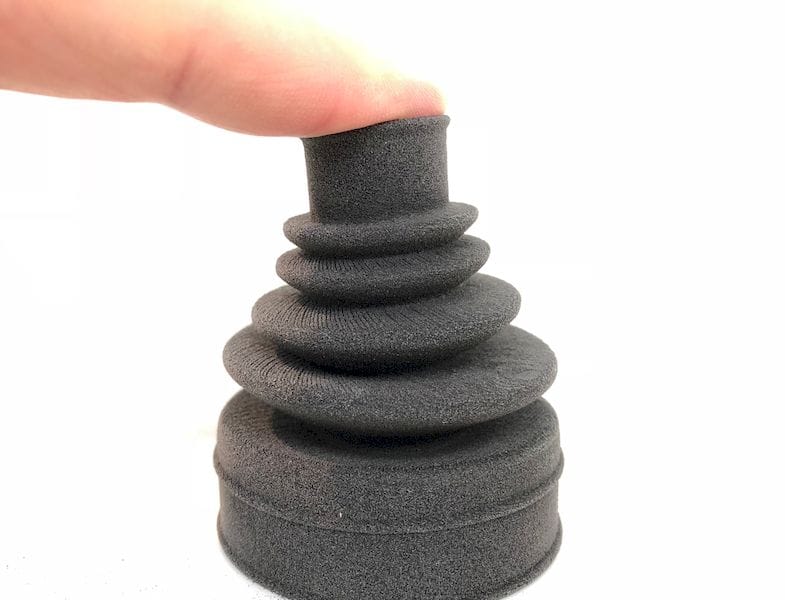
3D printer manufacturer Sintratec has released a new flexible capability.
The Swiss-based company has produced inexpensive power-bed laser style desktop 3D printers for several years now, with the ability to produce strong nylon objects. Now they’ve switched things up a bit with the introduction of a flexible system.
While they haven’t really changed their equipment, they have introduced a new TPE material. This material, when fused by their 3D printer, offers a degree of flexibility. You can see the results in the image at top.
Ambitious Sintratec operators might have attempted to 3D print such powder on their own, but this new material is certified by the company, and their software can provide the optimum settings for successful 3D printing operations.
One question we had was whether it was possible to 3D print the company’s two different materials in a single machine (the other being their standard PA-12 nylon powder). I had thoughts that you might be able to purge the unit of the former powder and then introduce the new powder.
Apparently that’s not the case; Sintratec representatives explained that you really need to have two machines, one dedicated to each type of powder. I can understand this, as it would be challenging to somehow extract every single particle from the material flow path before introducing the next powder. Perhaps if the machine was explicitly designed to do so, it might be possible, but apparently it is not.
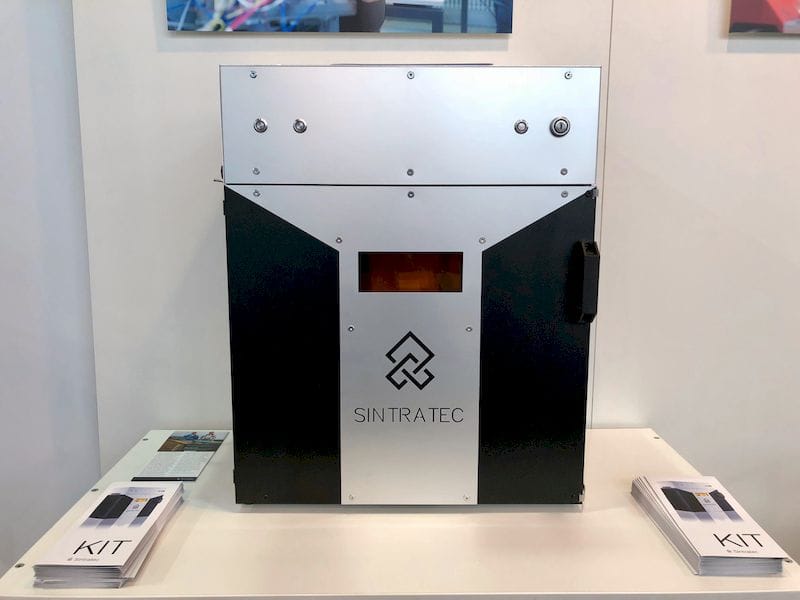
That’s not that big a deal, as Sintratec’s equipment is not that expensive to start with. Their entry-level “Kit” is priced at only €4,999 (USD$5,900) and their flagship model is €19,800 (USD$23,400), both far less than the typical powder-bed laser 3D printers capable of 3D printing in nylon.
It seems that there are some powerful nylon 3D printing capabilities now available at relatively low cost.
Via Sintratec