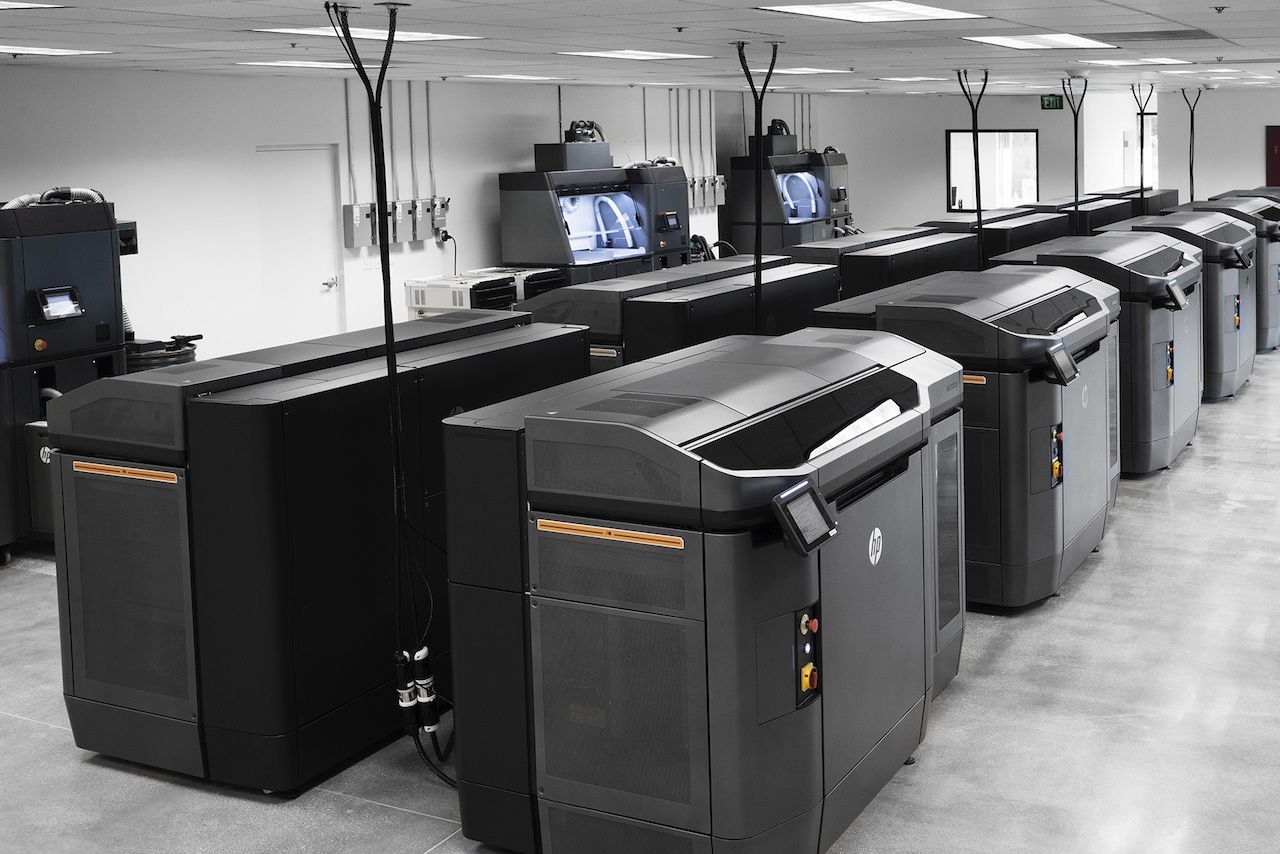
HP today made some interesting announcements that tell us quite a bit about their long term strategy, which just might work.
HP is like the elephant in the room within the industry. They’re really big – financially. When they move, it’s important. While they are quite a bit smaller than the existing players in the 3D printing industry, that may not be so in the future.
But let’s look at today’s announcements, which on the surface are less important than their long-term implications.
First, the company announced a new 3D printer, the MJF 4210, a device specifically designed for production use. We asked what makes this machine different from the earlier model, and were told that it includes features specifically designed to accommodate manufacturing.
The MJF 4210 can apparently handle “bulk packaging” of materials of up to a ridiculous 1,000L – or more! To put this in perspective, this is literally a cubic meter of material. I suspect this is the size of the 4210’s build module.
The massive capacity will enable much longer continuous operations, which decreases operator cost and generally lowers the cost of parts produced on the system.
The other change on the MJF 4210 is significant changes in the workflow to operate it; data management, control parameters are altered to allow more degrees of freedom to define and integrate the device into a real production process. Also very important.
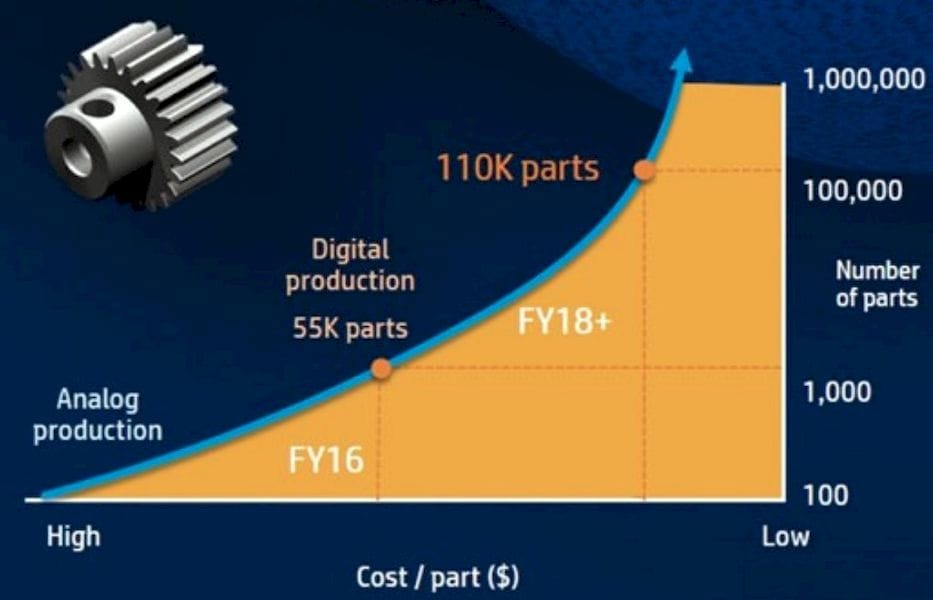
HP stated one of their strategies is to drive down the cost of materials, and the MJF 4210 seems to be part of that equation. They say the cost per part could be 65% less than “other solutions”, and that they now feel the system has a 110,000 part quantity break-even price opposite traditional injection molding. Of course, this depends on the nature of the part, but their point is simply that with the lowered costs per part, you can justify doing larger runs. Even more ominous is their intention to raise this to over 1,000,000 parts within a few years. This would utterly transform manufacturing, as a million parts is a million parts, that’s effectively mass production scale.
The other announcements made by HP related to materials and their material development strategy.
First, they announced three new interesting materials, including Nylon PA-11, a PA-12 with 40% embedded glass beads and a Polypropylene material. Each offers different engineering characteristics that could open up a few more applications for the system. Here is HP’s description:
- HP 3D High Reusability PA 11: for producing low-cost, high-quality functional parts with impact resistance and ductility for prostheses, insoles, sporting goods, snap fits, living hinges, and more.
- HP 3D High Reusability PA 12 Glass Beads: for producing low-cost, high-quality functional parts with dimensional stability and repeatability ideal for applications requiring high stiffness like enclosures and housings, molds, and tooling.
- HP 3D High Reusability Polypropylene: Durable low cost material that offers enhanced flexibility with excellent chemical resistant, lightweight, and watertight capabilities.
Finally, they’ve developed what they call a “3D Materials Development Kit”. I’m not sure exactly what this might be, but I suspect it might include a smaller model of the MJF system designed for experimenting with unusual materials.
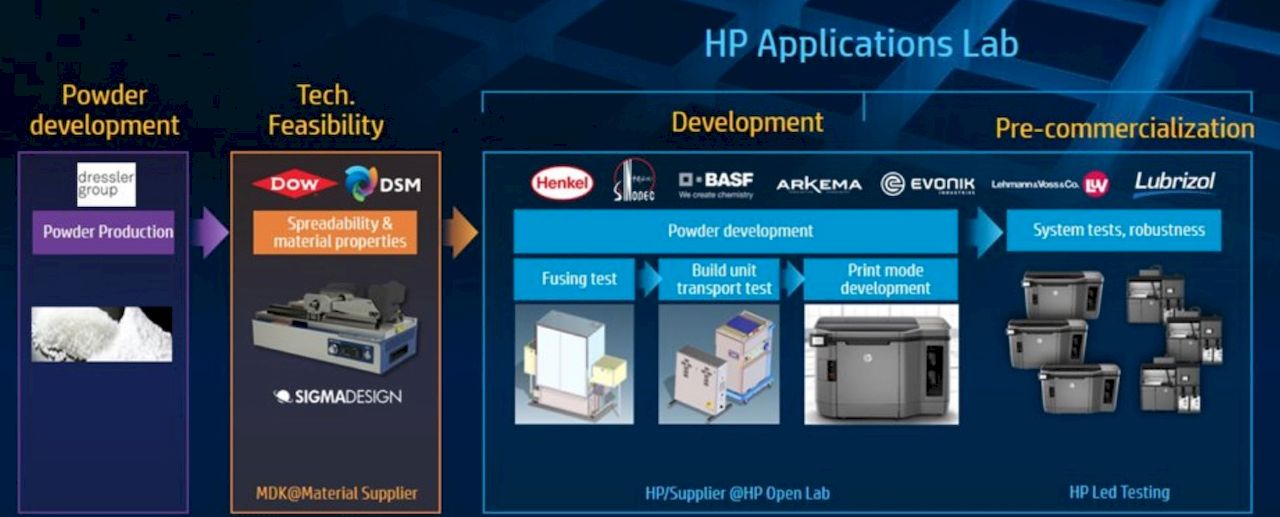
This kit is being distributed to several global-sized chemical companies to assist in the development of additional materials. Two new large players, Dressler Group, and Lubrizol, have been added, while others, like Dow Chemical, have taken on the development kit.
HP’s strategy here is extremely interesting. They are enabling chemical companies to work with their clients to develop new materials as required for applications. This means they are forming a worldwide squad of material makers that will all gradually add to the HP materials suite. Eventually, HP hopes to have a portfolio of materials that will rival today’s injection molding world, where there are literally thousands of different materials for product makers to choose from.
So let’s put this all together and add it up:
- They have added a few new materials and set up a pipeline to develop dozens or even hundreds more materials
- They have introduced a machine designed to integrate with production manufacturing environments
- They have lowered the per-part cost of printing
- They have NOT sped up the per part print speed (time per part), but have increased the system throughput (number of parts per time)
If you look at these points, and in particular the last one, it is very clear they are making a huge play for future manufacturing with 3D printing technologies.
I find this interesting because the existing market is largely for prototyping and very low volume manufacturing. HP has been severely constrained in those environments due to Stratasys’ exclusive contracts with the major resellers, making it challenging for HP to sell to those markets.
What is the answer then? Make a new market: Production.
They are doing an end-around Stratasys’ reseller contracts by pushing strongly toward manufacturing, which will typically involve different resellers and different sales processes.
Meanwhile, both Stratasys and 3D Systems have made significant buzz lately about production intentions, so the race is now on.
Via HP