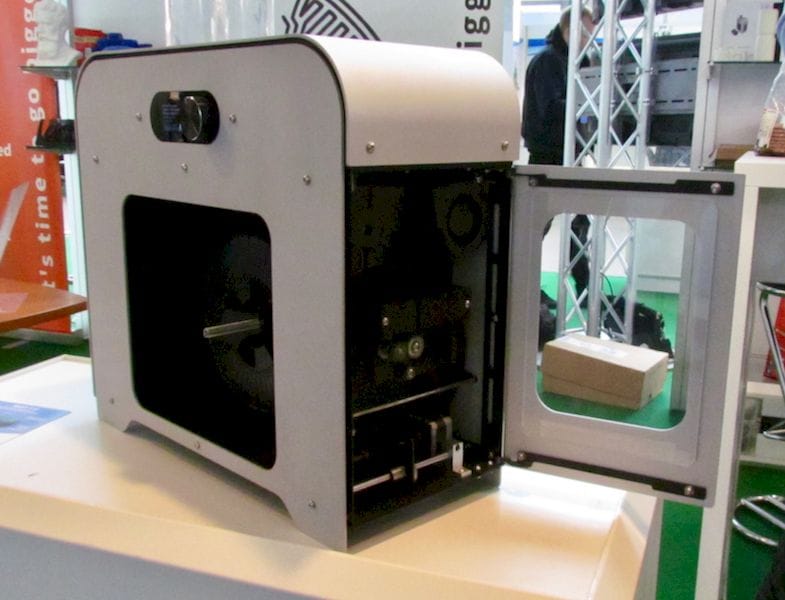
We finally got a close look at 3DEVO’s desktop filament maker.
The device, called the “NEXT”, actually makes usable 3D printer filament from pellets – or similar raw thermoplastic material. It works by precisely melting the input material and extruding it through a nozzle of diameter suitable to form filament in the desired size. The filament is carefully cooled and then spooled up as it emerges.
The result is a spool of 3D printer filament that’s instantly usable.
3DEVO markets two models, the “NEXT Regular” and the “NEXT Advanced”. The primary difference between the two is analogous to the difference in some professional desktop 3D printers: the temperature.
The advanced unit is able to extrude materials up to 450C, making it able to form filament from more exotic engineering materials such as PEEK or PC. It also has a larger spool capacity for additional material take up.
The regular unit is able to handle PLA, ABS and Nylon PA-12, which is entirely suitable for many users.
Fortunately, 3DEVO provides extrusion profiles for each material, making it relatively easy to successfully extrude your own filament.
In fact, you can produce a number of interesting materials for 3D printing as shown here.
The regular NEXT costs €3,550 (USD$4,200), while the advanced version costs either €4,150 or €4,275 (USD$4,930 or USD$5,080), depending on whether you want the white anodized case.
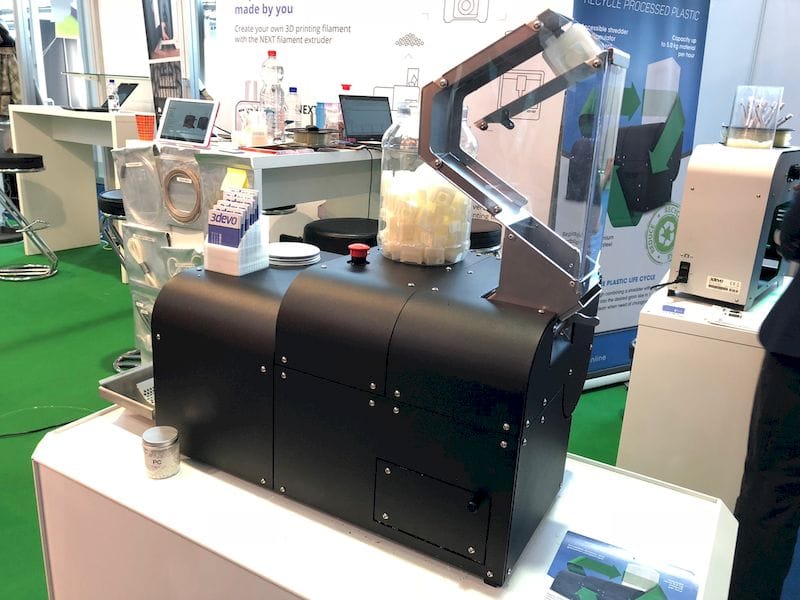
What was of particular interest to me was their new product, the SHR3D IT plastic processor. This is an accessory to the NEXT units, which is able to accept larger plastic objects and shred them into small pellets. The shredded material is perfectly formed for use in the filament extruder.
With the SHR3D IT device you could potentially be able to recycle undesired previous prints. This is something I am interested in, having my office literally covered with accursed 3D prints from years of printing.
However, this doesn’t mean your single purchase of 3D printer material can be recycled endlessly. 3DEVO representatives explained that in fact during each heating cycle the plastic’s carbon chains get shorter, and eventually it just won’t work. I’m not sure how many cycles this may take, but even a few cycles may be worth the effort.
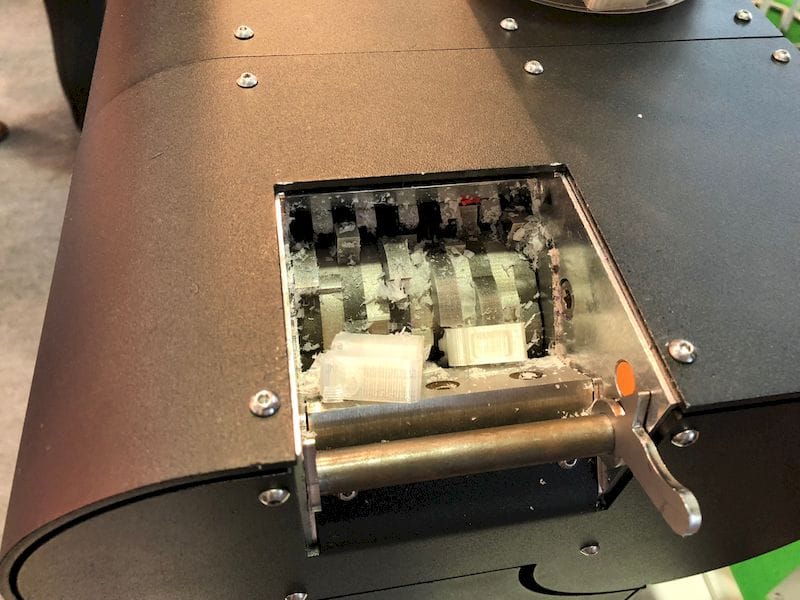
The SHR3D IT device includes, as you might imagine, an input hopper, where you can insert large chunks of plastic, typically previously 3D printed items. The reason for this is that you can be reasonably assured of a consistent material within the same print. If you’re mixing materials on the input side, your output filament will be similar mixed up, likely compromising print quality.
There are two stages of operation in the SHRD IT. A slower chopper is the first stage, and then a higher speed cutter creates the final output material. A size filter ensures the pellets are of consistent size.
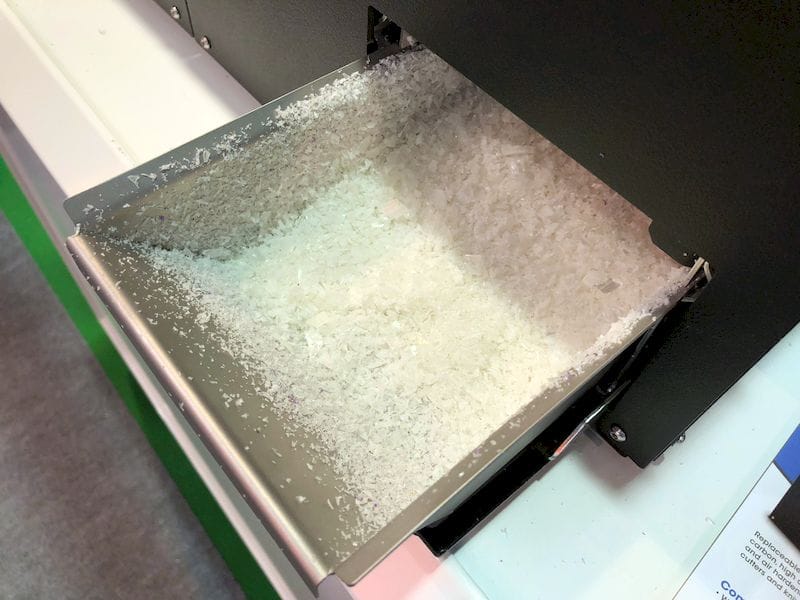
The output of the SHR3D IT collects in another hopper. This material can be directly poured into the NEXT extruders to create new filament. It’s also possible to add a bigger receptacle to hold larger quantities if required.
One interesting spec is that the SHR3D IT requires only 1100W power while running, meaning you can more easily power both the shredder and a filament maker on the same circuit.
The SHR3D IT is priced at €2,975 (USD$3,500), meaning for the combined price of only USD$7,700 you can set up your own thermoplastic filament recycling system. To put this in financial perspective, if you were saving USD$30 per kg spool, this means you’ll break even after around 250 spools recycled.
While that amount of material may be large for an individual, there are certainly many businesses, universities, makerspaces and institutions that would indeed go through that many spools over the course of a year or two. For them, this setup could be quite attractive.
Via 3DEVO