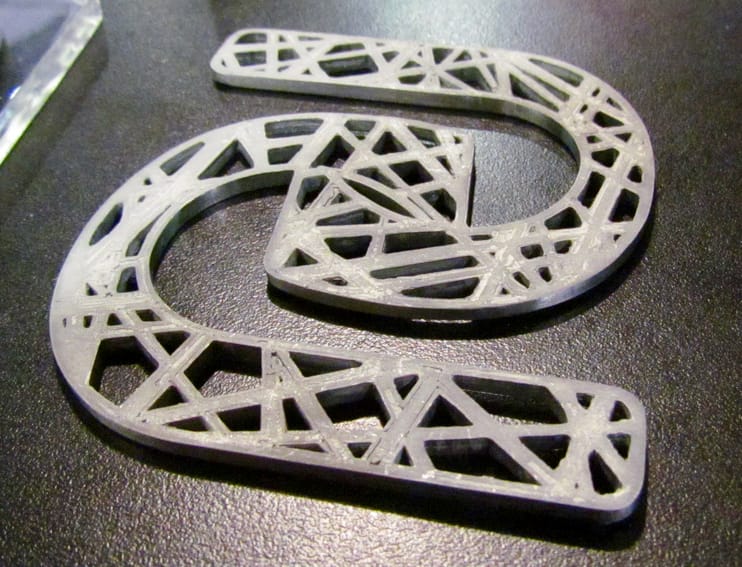
Just about everyone interested in metal 3D printing finds it difficult to stay on top of all the advances with the technology.
Whether itâs an innovation that pushes forward an existing metal additive process or the creation of a new process entirely, it seems there is no shortage of content on industry websites and blogs.
We will help to make sense of the current metal 3D printing landscape by reviewing the latest versions of some existing technologies and also new processes that are close to commercialization.
Powder Bed Fusion
Powder Bed Fusion (PBF) is what comes to mind when most people think of metal 3D printing. PBF includes two main technologies: laser sintering and electron beam. These techniques are grouped together since they each begin with a layer of metal powder being rolled onto the build tray, and then an energy source (laser or electron beam) fusing or melting the powder into deliberate 2D designs. These thin 2D layers are fused on top of each other to create the 3D object.
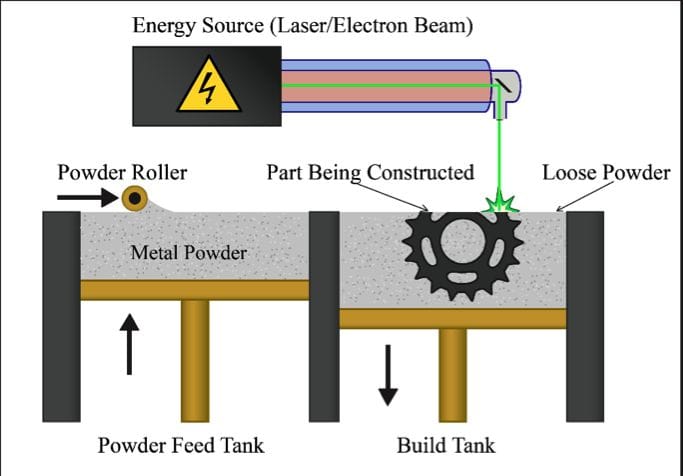
PBF received a huge shot in the arm last year when GE purchased Concept Laser (laser sintering) and Arcam (electron beam). The massive engineering infrastructure of GE is now being brought to bear on PBF and the rumor mill is awash in reports of forthcoming increases in capability including increased build sizes, reduced build times, and larger material portfolios.
Time will tell regarding actual advances, but itâs clear that GE has taken the lead globally with the creation of their GE Additive division. Despite many of the recent advances to date, high-quality PBF machines are still over $1 million per unit with only modest throughput. This limits the current range of applications of PBF to only high-value parts that are used in industries such as aerospace, industrial power generation, and others with extreme environments where the high part cost can be justified.
Binder Jetting
Binder jetting has recently seen a huge spike in interest, most notably from the massive marketing effort by Desktop Metal. HP is reportedly developing a binder jetting machine as well. Binder jetting is a powder bed process that utilizes inkjet technology and a binding agent. The inkjet head deposits binder in the shape of the part for each respective layer, and the result is a âgreen partâ which then needs to be placed in a sintering furnace to achieve final part density.
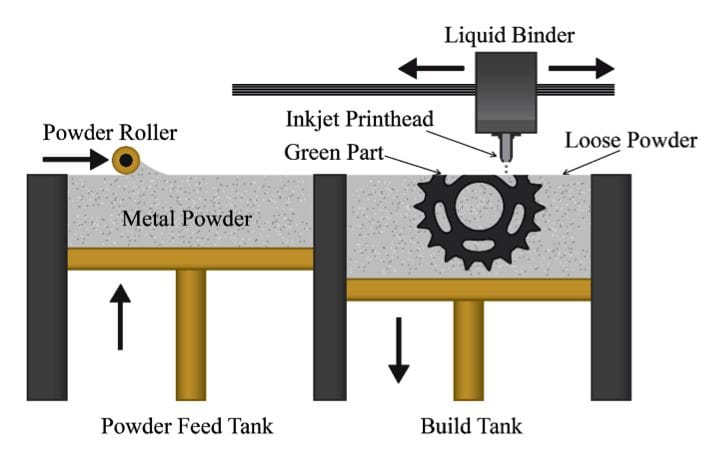
The technology showed a lot of early promise for reducing both print times and cost when it was commercially released in the early 2000s. Unfortunately, the need for infiltration (usually bronze) precluded it from replacing traditional manufacturing due to the changed material properties of the metal being infiltrated.
There is renewed enthusiasm for binder jetting this month, as Digital Metal recently released a non-infiltration binder jetting machine that creates high-resolution smaller parts, and Desktop Metal plans on using binder jetting for its high-volume production system scheduled to be released in early 2019. Binder jetting appears to be the early favorite for tapping into higher volume metal applications not currently addressable by PBF.
Emerging Metal 3D Printing Processes to Watch
The excitement surrounding 3D printing has driven investment across many new metal 3D printing technologies. Though not exhaustive, here is a list of several new technologies entering the market.
Material Jetting
Material jetting is an interesting new technology that has transitioned over from the plastics and polymers platforms. Material jetting with metal is like binder jetting in that a green part is created and then sintered in a furnace. The difference is that material jetting is not a powder bed process â instead, metal particles are combined with a binder before being jetted through a nozzle and are then carefully placed on the build tray to create the green part.
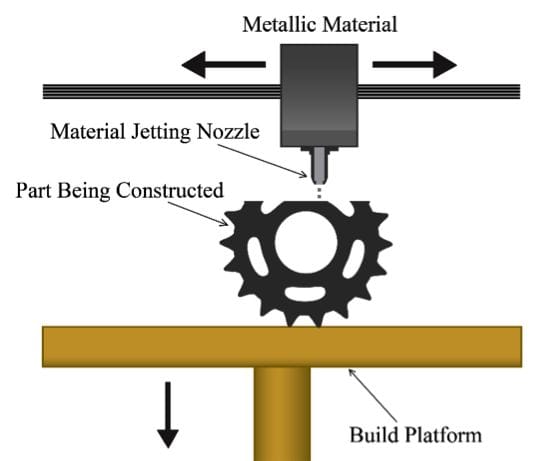
XJet is making a splash for material jetting with its patented NanoParticleJetting technology. The company just shipped its first commercial unit to a customer, creating an important milestone for this emerging metal 3D printing technology. It appears that the build size for material jetting is still smaller than PBF or binder jetting, but the technology is worth keeping an eye on as it continues to advance.
Bind & Sinter
This is a catch-all category that includes technologies other than binder jetting/material jetting that also use metal powder and a binder to create âgreenâ parts that are sintered in a furnace. By removing the sintering process from inside the machine and moving it to a separate furnace, these processes help reduce the machine cost and ultimately lower the per-part cost.
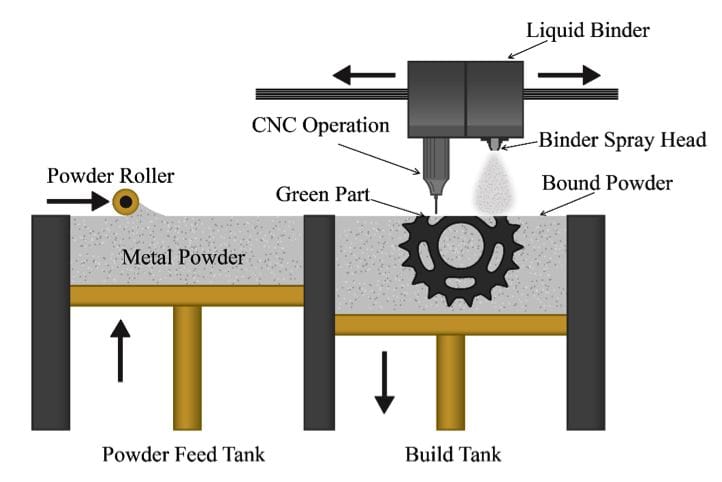
3DEO created a low-cost metal 3D printing process in the bind and sinter category. Fabbaloo wrote about their âIntelligent LayeringÂźâ technology back in July. The company focuses on low-cost parts in higher volumes than currently available with existing metal 3D printing technology. They differ from the industry in that they are keeping their technology in house and supplying parts, rather than attempting to sell machines. Their speed to market was increased by tying Intelligent LayeringÂź to MPIF Standard 35, a widely accepted powder metallurgy quality standard used in metal injection molding.
Metal Extrusion
Fused Deposition Modeling (FDM) is the most popular form of plastic 3D printing, but there are companies attempting to print metal using an FDM-like extrusion process and metal filament as the material.
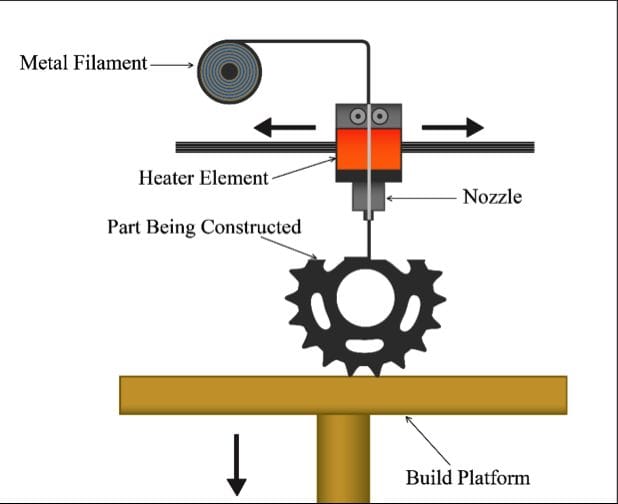
Desktop Metal is using the metal extrusion technology in its new Studio system that is aimed at prototyping. Due to the nature of the extruded material, FDM-like metal processes are generally not appropriate for production because the integrity of the parts are not homogenous.
Metal 3D Printing Marches On
There are several existing technologies that have been omitted from this list including directed metal deposition and sheet lamination, but that doesnât mean they arenât worth tracking. It is an exciting time to be following the metal 3D printing industry and be sure to visit Fabbaloo for latest developments of the technology.