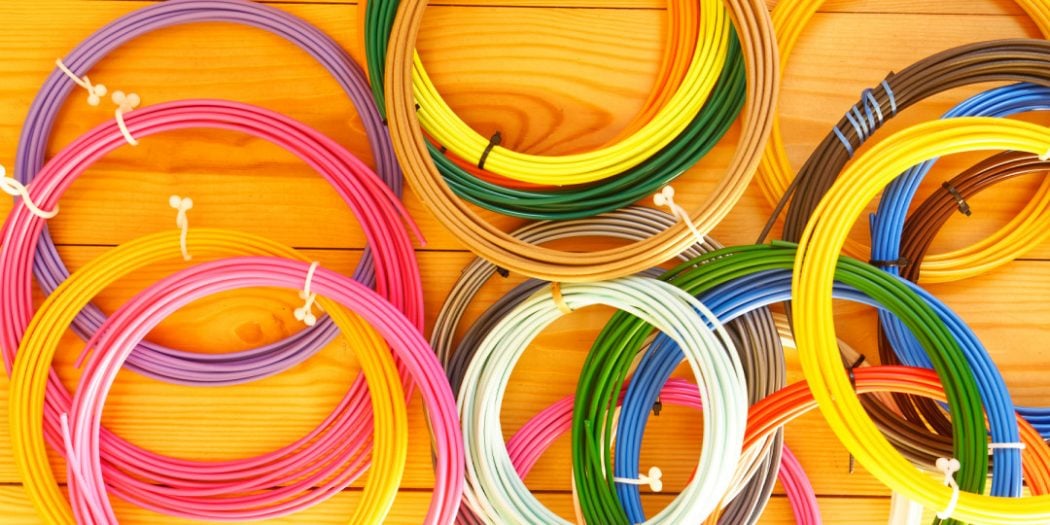
There’s a long discussion of the opportunities and challenges in the 3D printer filament business.
The material takes the form of a set of interviews undertaken by our friends at 3D Printing Business Directory, who interviewed no less than ten folks charged with delivering quality 3D printer filament to buyers worldwide.
Interviewed were representatives from colorFabb, PrintaLot, TreeD, Filamentum, Taulman3D, EUMAKERS, 3D4makers, 3D Printlife, FiloAlfa and 3DXTECH. These are certainly not the entire group of 3D printer filament makers, but a very good cross section of different types of manufacturers of quality 3D printer materials.
Interviewer Minuca Elena asked each about their challenges, evolution, customers, popular products and their thoughts on how 3D printing could be more widely adopted. I was most interested in the answers to these questions.
Regarding the most popular materials, the group fell into two categories: one category, that appears to focus on consumers, tended to sell mostly PLA and far fewer “exotic” materials. The other group focused more on the professional market and sold more nylons, high temperature and other materials used by professionals. Most of these companies do actually sell all types, but it’s interesting to see how they diverge on market.
It seems there are companies slowly gaining a reputation as popular sources for particular types of materials.
Virtually all of the respondents faced challenges due to the explosion of diversity of materials in recent years. Demand from professionals using new, more powerful desktop 3D printers has resulted in a new market. Some filament providers are challenged to identify which new filaments to produce for clients, while others must chemically design them. Others must search through corporate plastics repositories to find appropriate products to match customer needs.
I suppose this is an expected result of the introduction of professional desktop 3D printing, a new discipline that places far more stringent demands on filament providers than the “yoda head machines” as one respondent described.
3D4makers’ Jasper Wille hit the nail on the head with this profound comment:
In aerospace, there are very few standards for filaments for example. Apart from flammability standards such as UL 94 there few standards for filament production and parts. There are also no standardized protocols for moisture in filament or the strength of 3D printed parts. For different customers, we have different tests in place to satisfy their needs. There are also no standards for medical filament, filament for wearables, conductive filament. We develop many filaments some for very specialized applications in space, aircraft, conductivity, oil and gas and other applications. Many times we’re developing our own requirements, standards, testing protocols and quality control as we go along. It would be much simpler if many things were codified and established.
This demonstrates one of the biggest problems in the 3D print materials industry: there are no standards, so no one really knows what they are getting. As a result, the market often defaults to the reputation of the provider. It’s possible some leading vendors in that position may not desire standards, but I suspect they are inevitable sooner or later.
Beyond the introduction of materials standards, the respondents mostly agreed that one key factor that would strongly assist growing adoption of 3D printing would be methods of simplifying the ease of use of the technology. This might include education, more reliable equipment or simplified ways to generate 3D models, but all would help.
And we certainly agree. Read the full story at the link below.