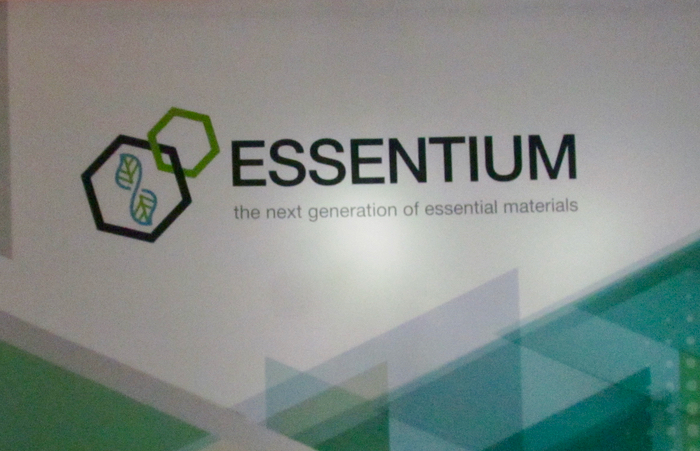
It’s been a long time since I’ve seen something this revolutionary: Essentium has created a completely new filament-based 3D printing process.
For as long as everyone can remember, the process of 3D printing filament has been as follows: feed a thermoplastic filament into a hot end and move around the shape of the object. The problem with this approach has been around heating, where desirable materials expand and shrink according to temperatures encountered. This generates warps, dimension issues and other challenges. Another problem with this approach is that the fresh layer, while at softened temperature, is laid upon a cold layer, making layer bonding less than optimal.
Industrial machines solve these issues by enclosing the build volume and providing heating for the entire chamber. Typically such arrangements operate around 70C, making materials more or less stable during printing. Once complete, the parts cool uniformly in all directions to assume the desired dimensions.
However, the heating system is under patent by Stratasys, thus this approach is not open to other 3D printer manufacturers, and the results of 3D printing are accordingly not optimal.
Now Essentium has developed a brilliant new approach to solve this problem, which they call “FlashFuse Filament”. Here’s how it works:
- The Fuse filament has a unique coating containing carbon nanotubes and other special materials that are electrically conductive.
- The filament is 3D printed in the typical manner, heated through a hot end and extruded through a nozzle.
- The special coating is mixed through the plastic during extrusion.
- An electric current is applied to the nozzle.
- An electric circuit is formed between the nozzle, through the extruded plastic and a metal print surface, which completes the circuit.
- Electrical resistance in the special material generates heat.
- The extruded plastic remains at a desirable temperature throughout the printing process.
This process has a number of important benefits.
First, since all of the extruded plastic is at temperature, the bonds between layers are far stronger because the plastic can mix more than occurs with typical “hot on cold” layer printing.
Second, the print doesn’t warp because the plastic remains at a high temperature for the entire printing process.
As a bonus the carbon nanotubes add significant strength to the material, and when combined with the improved layer bonding, creates a very strong print. Essentium claims some parts exceed the strength of injection molded parts. Delamination should be a rare occurrence with these prints.
I’m very impressed with Essentium’s approach because it negates the need for a heated chamber entirely: you heat the plastic directly instead of a huge, mostly empty chamber. In fact, the energy required to heat the plastic is far, far less than that required to heat a build chamber. And there’s no warm up time, either.
The company likes to describe this process as “electromagnetic welding” and I presume they are correct.
The parts are dimensionally stable during printing and shrink uniformly after printing, just like those from 3D printers with heated chambers.
I should point out that such parts remain conductive even after 3D printing. This may be of benefit in some situations but not in others. Thus you may have to post process your print to remove conductivity by painting or otherwise treating the surface.
The company is hoping to launch this product in mid year, and you can bet it will carry a premium price.
But you might ask, “How can I use this filament if my extrusion system isn’t electrified?” Essentium is developing a kind of “add on kit” that can be applied to a variety of commonly found desktop 3D printers. Currently they have an in-house machine for testing and development.
It’s also possible they may strike deals with 3D printer manufacturers to include their technology within new models in the future.
It’s been said that the future of 3D printing is materials, and developments such as this are confirmation of that premise. An invention from a company that otherwise produces straightforward 3D printer filaments could generate much change in both hardware and materials.
Via Essentium