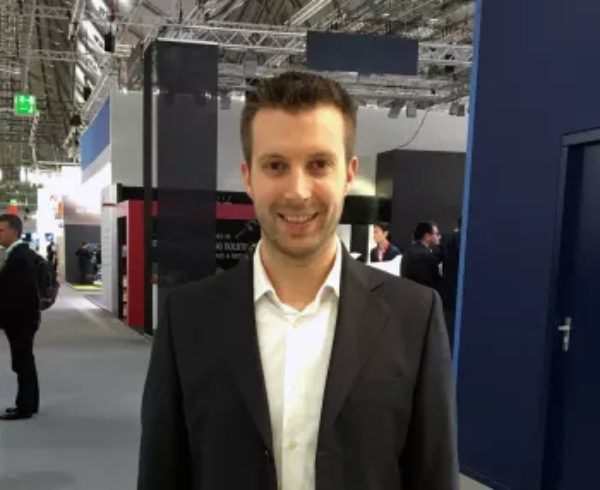
Compared to plastic 3D printing technology, metal additive manufacturing (AM) is relatively young.
EOS released the first commercial powder bed system in 1995. Since then, a handful of manufacturers have maintained dominance in the space, but, in more recent years, a number of new powder bed metal 3D printers have been introduced to the market with the potential shake that dominance.
In 2014, the Italian Sisma Group and German Trumpf Group embarked on a joint venture to create a new line of metal 3D printers. While Trumpf had manufactured directed energy deposition (DED) machines, together the companies developed powder bed systems. Sisma went onto release the smaller mysint100 in 2014 before releasing the larger mysint300 in 2016.
ENGINEERING.com reached out to Adriano Bernardi, product manager for the Additive Manufacturing division at Sisma, to learn how the company’s powder bed metal 3D printers fit into the larger 3D printing ecosystem and into Sisma’s vision overall.
Entering the AM Market
Bernardi explained how Sisma went from its roots in machine production into the 3D printing industry. “Sisma is a worldwide reference in designing and producing high precision machinery and laser systems. Established in 1961, Sisma has extensive experience with more than 130 models of automatic chain-making machines. Today at the forefront in the development of laser solutions, Sisma has been able to extend its know-how to marking, welding, cutting, engraving and the most recently developed range of Laser Metal Fusion and Laser Stereolithography 3D printing systems,” Bernardi said.
Sisma may now be the largest laser manufacturer in Italy, selling about 1,000 laser devices every year. With both Sisma and Trumpf as experts in manufacturing equipment, a proprietary series of metal 3D printers would give them both strengths in their respective markets. On the one hand, Trumpf could add to its line of laser welding systems with a powder bed series, making it the only manufacturer to have both DED and powder metal 3D printers. For Sisma, it could provide the opportunity to further target its existing customer bases and expand beyond them.
“Sisma is widening its range of 3D printers and is pushing to become the top player in terms of output quality, machine userfriendliness and post-process know-how,” Bernardi said. “Constantly involved in research & development, the aim is to improve and update its technological solutions, being able to provide an extensive range of material options (resin, metal) while covering very specific sectorial needs (industry, jewelry, dental, medical).”
Read more at ENGINEERING.com