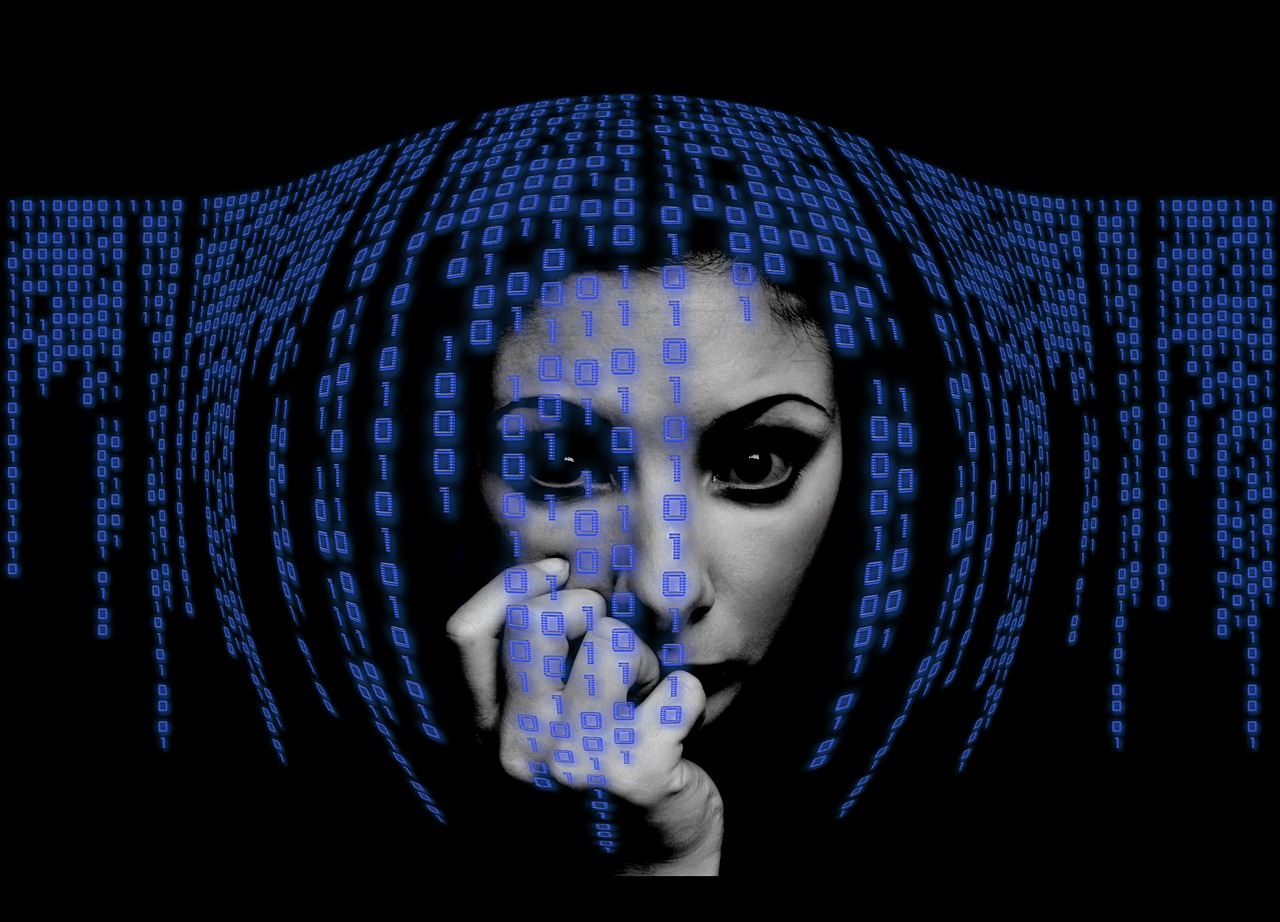
3D printing has continued to prove itself as a promising solution for many manufacturers/businesses, creating opportunities and prototyping capabilities that were once unavailable, while significantly expediting “time to market”.
With the cost of hardware decreasing and machine efficiency increasing, it’s no wonder that many businesses have adopted or considered incorporating some level of 3D printing. And as the products become more real, so do the risks.
Intellectual Property Concerns: The only people more excited about the capabilities of 3D printing than designers and manufacturers are counterfeiters. Counterfeiting and IP concerns continue to be one of the most cited challenges posed by additive manufacturing, and for good reason. In order to combat the potential for IP theft and illegal copies, organizations are exploring creative ways of embedding authenticity verification into their products such as the use of RFID tags and nano crystals called “Quantum Dots”.
These counterfeits can be more dangerous than many people might assume. In addition to bleeding corporate revenue, they can also pose a considerable threat to end users and the public alike. It’s entirely possible counterfeit industrial parts such as screws and bolts can more quickly/easily fail once installed, resulting in potential bodily injury or property damage.
Even in situations where there has been no actual counterfeiting or infringement, this technology creates the potential for frivolous allegations which can result in significant defense costs. While manufacturers may be more likely to encounter IP claims, the potential of having ones own IP copied/stolen is even greater. Larger companies and those that believe they may be at particular risk for such litigation, should consider partnering with an experienced IP attorney and/or exploring IP insurance.
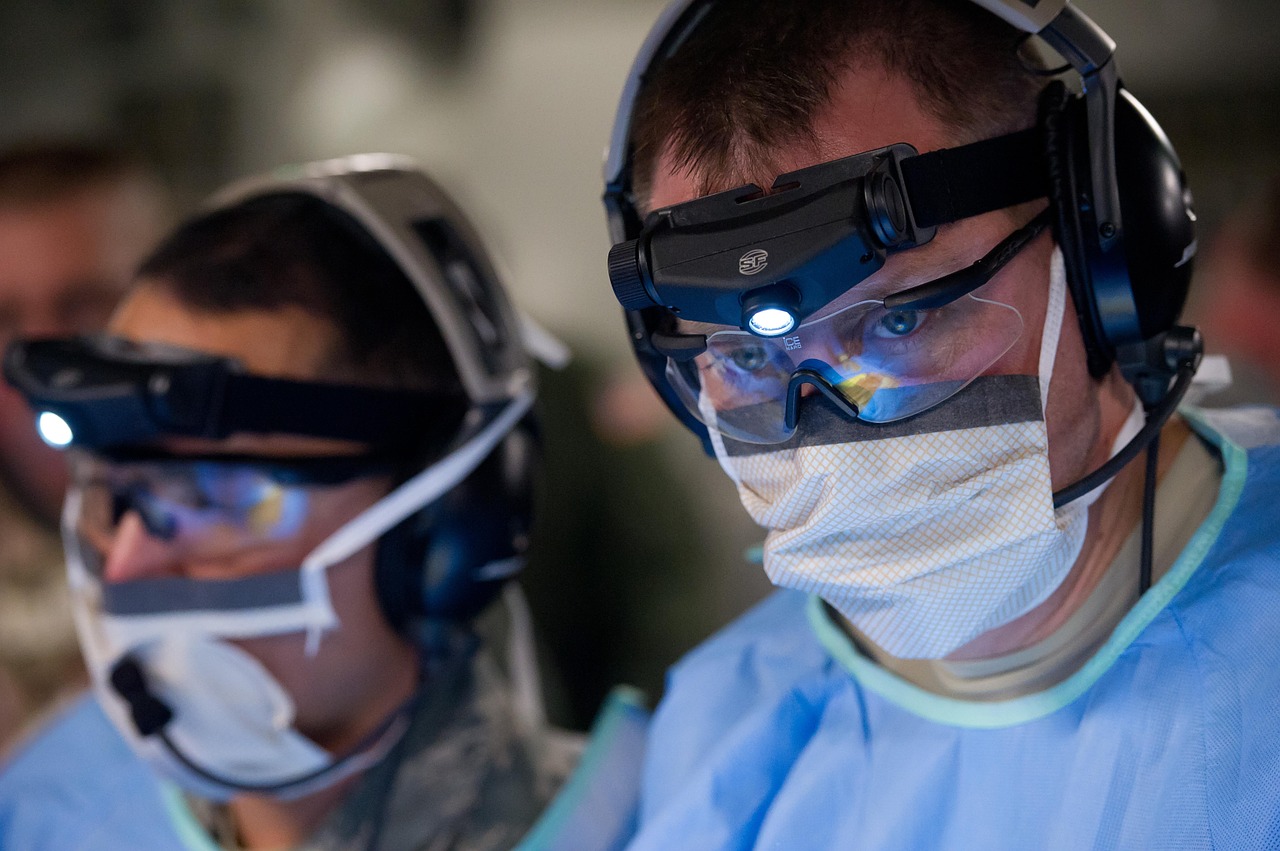
Workplace Safety/Occupational Concerns: There is still relatively little data regarding emissions, toxicity and UFP’s (ultra fine particles) produced during printing and the potential associated adverse health effects, but the data does seem to confirm cause for concern. Long term exposure in particular could result in respiratory issues and skin irritations or have more severe lasting health consequences. For larger operations, it could also become an environmental /pollution hazard subject to emissions or environmental laws.
While the overall effects are still being researched and published, 3D print operators are well advised to familiarize themselves with OSHA (or relevant local) safety standards and implement proper safeguards such as masks, gloves, goggles and ventilation systems to help protect employees from unnecessary exposure.
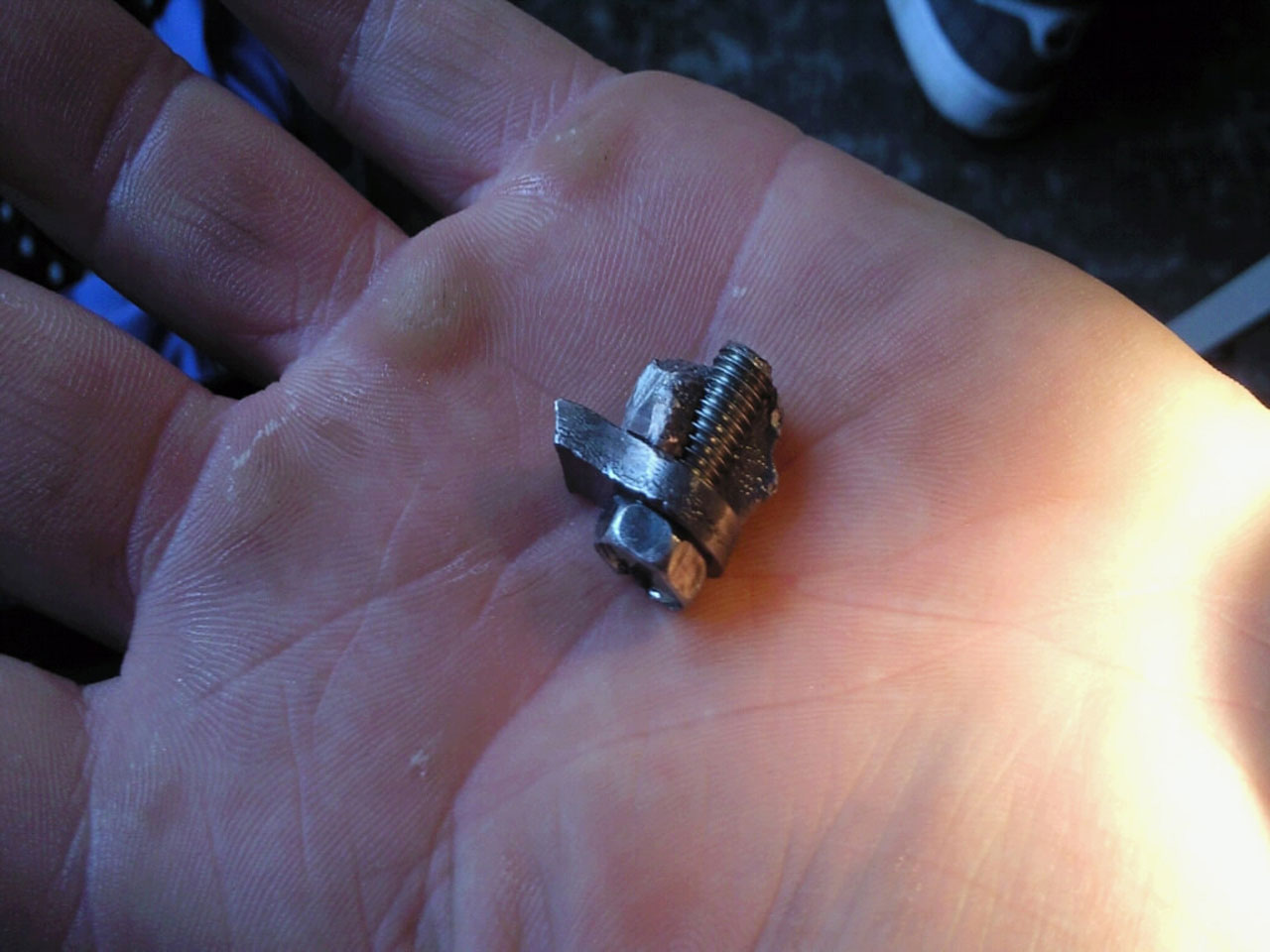
Engineering and Product Liability Concerns: 3D printing provides speed at the cost of strength, and also brings with it a greater chance of oversight in addressing potential product liabilities.
Most 3D printed products do not have the same structural integrity as their molded counterparts due to the layered nature of the printing process. Utilization of under-qualified CAD designers/engineers can also result in compromised product integrity.
Printers and manufacturers should have established professional/vendor criteria when hiring or outsourcing the design process and ask the important questions; Who is performing any required engineering calculations? Are they qualified? Have all critical joints, connection points and stress tolerances been properly calculated? For any consumer products housing electronic parts, has proper heat dissipation been accounted for and are all electrical components proper shielded? What methods are used for testing? For products that might be utilized by children, its also important to consider risks such as potential allergic reactions or choking hazards. Printers must also ensure they are aware of (and in compliance with) regulatory and statutory laws such as those posed by the CPSC and FDA among others.
Limited Medium and quality: 3D printers use materials in several forms: powder, solid plastic filament and liquids. While the list of usable materials is still generally limited to particular ceramics, plastics and metals, newer materials are becoming available, from carbon fiber and carbon nanotubes all the way to stem cells. The effectiveness of 3D printing machines’ capabilities with these advanced mediums is still to be determined.
Additive manufacturing also has its aesthetic limitations when it comes to obtaining specific colors, finishes and/or design work. For products that require specific materials, ratios or specific design aesthetics, 3D printing may not be a solution – substituting materials or sacrificing design can result in compromised product quality or decreased product appeal and loss of sales.
Lastly, ensuring the quality and consistency of the materials themselves is best-practice, especially for products which need to perform under stress or loads. It can be easy to assume that all of the materials are properly labeled and thoroughly mixed when received, but failure to check consistencies, ratios and strengths can result in unintended product failures, and any resulting litigation will likely rest on the shoulders of the printer (especially if the supplier is located overseas). This risk is best managed through the Implementation of supplier qualification criteria, established internal quality control assessments and obtaining “additional insured” certificates of insurance from all suppliers and outsourced 3rd parties involved in the process.
Costs and Energy: Machines can be resource and energy heavy depending on the type of production run. The cost-benefit advantage is dependent on the complexity and number of parts or products being produced. Production costs may be low for a single complex prototype or custom part but due to the loss of economies of scale, the price (and time to market efficiency) is quickly diminished with larger quantity manufacturing runs due to the resource requirements of the machines. There is fine line when it comes to benefits in costs and production times that need to be calculated. As machines become increasingly efficient, that line will be continue to be stretched.
Security/Cyber Concerns: Another often discussed risk is the possibility of a hacker tampering with your product or manufacturing process. The IOT (internet of things) and constant connectivity means that machines themselves are computers which can be breached or compromised like any PC. Downloading, storing and transmitting 3D models creates a lot of opportunities for security breaches. Hackers can also modify components and sabotage a company with the intent to profit from cyber espionage, ransomware or simply in retaliation.
Protection of your own IP/blueprints and lost income resulting from an attacker disrupting the manufacturing process are yet additional risks. Companies looking for a holistic risk management solution should implement strong internal security measures, thorough employee training, a well designed business continuity plan and a well structured cyber insurance policy.
Regulation on the horizon: As an advancement in its infancy, 3D printing is currently in transition between early adopters and more mainstream implementation. For many of the reasons mentioned above, regulation seems to be imminent. Those that make themselves aware of the risks, remain current with industry changes and abreast on regulations and litigation are sure to find themselves in a better place than those that are resting in the comfort of the untested waters that this technology has provided.