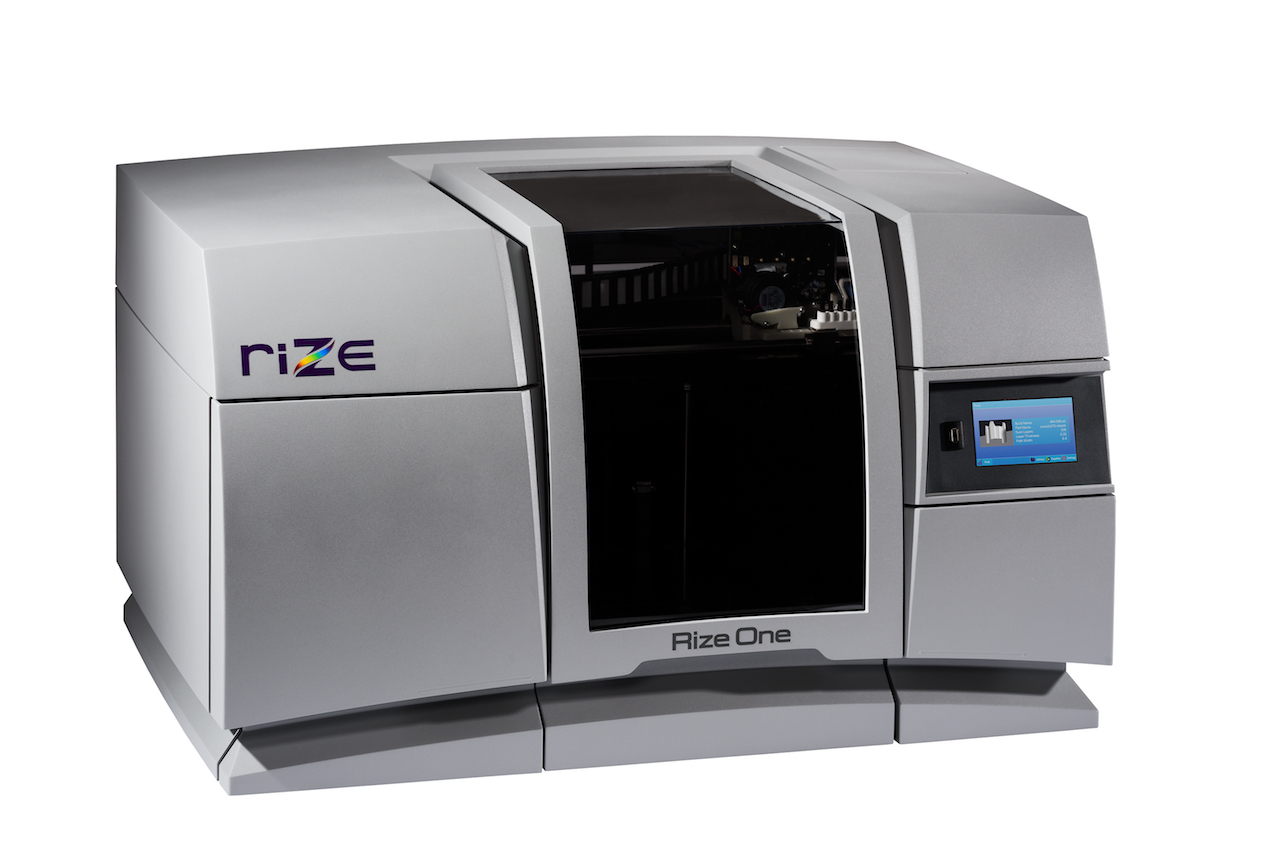
Stealth 3D printer startup Rize3D today released details on their new device, the Rize One, which has a unique approach to handling support structures.
The company has smartly addressed a key need of industry to improve efficiency. You see, it’s not just the ability to print an object; there are multiple steps in the process to produce a finished part.
The part must be designed appropriately for successful 3D printing first, followed by the actual print process. But after printing, almost all parts must undergo a post-processing step.
Post-processing is often an afterthought by most 3D printer vendors, but it is not only critical, but also time consuming and sometimes annoying.
Depending on the system used, post processing can involve lengthy baths in tanks of questionable fluids to dissolve supports; or you might have to use powerful waterjets to blast away support material, being very careful not to damage your object; or you may have to laboriously pick off support structures with hand tools, again being careful not to damage the part.
After you’ve spent hours doing one of the above, you then are often faced with a part that has a rough surface where supports were previously attached, or residual support material pasted within inaccessible crevices.
And for that you may have spent hours of human labor to complete.
This is the crux of the Rize3D strategy: drastically reduce this step in the workflow, while improving part surface quality at the same time.
How do they do it? Let’s look at all three stages.
First, the software. Rize3D has developed custom software that examines the incoming 3D model to ensure it is practical to 3D print, as well as slicing the 3D model for printing. However, you are able to examine the slices to ensure you’re getting the optimum strength for your part.
I have confidence their software will be well able to accomplish these tasks for one big reason: their founding team includes experts who created Revit, a well-known 3D tool for architecture and construction use.
Their 3D printer is the next step, and it’s a filament extrusion-based system. I should note that the Rize3D team includes staff from the former ZCorp and Objet companies, bringing with them a wealth of knowledge and experience.
The Rize One has a healthy build volume at 300 x 200 x 150mm, and prints in 0.25mm layers. This is definitely not the finest resolution I’ve seen in a 3D printer, as many filament extrusion machines can go as low as 0.05mm these days. However, that’s not what this machine is for; it’s to produce part prototypes that don’t require perfectly smooth surfaces. Also, their competition in this market, Stratasys, has FDM machines that offer similar resolutions.
Instead of the typical ABS or PLA materials, Rize3D has devised their own model material, “Rizium One”. Rize3D describes it as an “engineering- and medical grade thermoplastic” compound. Evidently this material is up to 2X stronger than typical alternatives. Rize3D says the materials will be priced at half the cost of materials from “similar class systems”. I take that to mean half the price of Stratasys FDM materials.
The Rize One also has a unique feature: it includes an inking head that can print lettering or images on the print surface at any angle. Essentially it squirts a little bit of ink on the edge on each layer. This feature can be used to provide identifying number codes on parts, which could be very useful if you are iterating through a series of prototypes.
But the key feature of the printing process, and indeed the major portion of Rize3D’s strategy is how the Rize One handles support structures.
The Rize One inserts a thin layer of a special fluid, “Release One” in-between the model and support material. Thus the support material is not solidly bound to the model material.
This brings us to the final step, post-processing, where the support removal takes place. Instead of cutting, filing, pulling, scraping, blasting or dissolving, you simply lift off the support structures, leaving smooth surfaces. Rize3D explains that this step takes only seconds. Perhaps you can even shake off the support?
That capability alone removes a great deal of post-processing labor, and produces a superior part as well.
This approach seems brilliant, although there could be one issue: if support structures are embedded within a geometry, it may not be possible to remove them. However, this is already a limitation on many existing 3D printing approaches.
Can you buy a Rize One today? Not quite. While the machine is just entering beta testing at several locations, the company plans to begin accepting orders in September, with delivery for later in the year. The cost of the machine itself will be USD$19,000 and USD$25,000 with a set of starter materials and a worktable.
My thought is that this is a very unique idea that could be of great interest to smaller companies seeking a powerful ability to create part prototypes quickly and cheaply. For some companies, the in-house 3D printing option can be discounted due to the unexpected cost of labor required to run the machine and post-process prints. That cost could be drastically slashed with the Rize One.
Via Rize3D