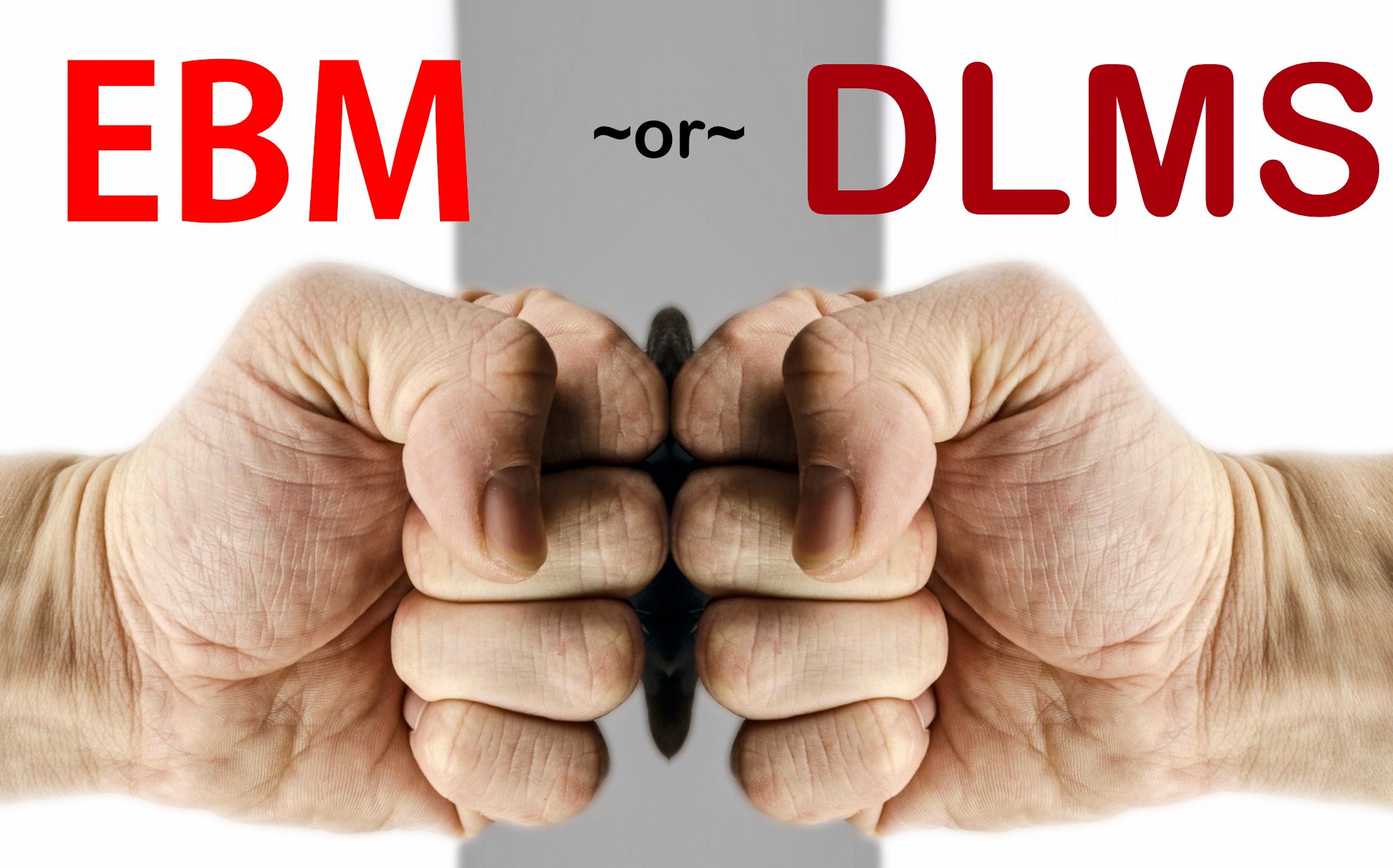
There is no escaping the fact that industrial 3D printing with metal is an increasing application trend for additive manufacturing technologies.
The capabilities of 3D printing with metal have improved dramatically in the two decades since it first became possible. In terms of longevity, two metal processes have been around since the 1990’s — DMLS (Direct Metal Laser Sintering) and EBM (Electron Beam Melting). As a result, a frequently asked question is: which one is best?
You probably won’t be surprised to learn that there is no easy answer to this question. As with all 3D printing processes — selecting the right one usually depends largely on how it is to be applied. That said, here I am going to take a timely look at both DMLS and EBM to highlight both the similarities and the differences and what this means for how they are being — and can be — applied in industry.
Let’s start with the obvious — both EBM and DMLS are industrial metal 3D printing processes that utilize metal powders to produce near net shape parts/components by way of additive layer technology. And these acronyms are both proprietary to the companies that have developed the respective processes.
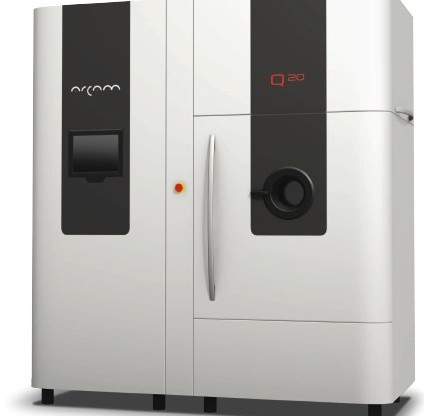
EBM
Arcam is the sole owner of Electron Beam Melting, or EBM. Founded in Gothenburg, Sweden in 1997, the first commercial EBM platform — the EBM S12 — was introduced in 2002. Since then the company has relentlessly continued its R&D, with specific focus on dominant vertical markets, specifically in the medical and aerospace sectors. Today, Arcam has EBM installations throughout the world, still predominantly focused on aerospace and implant applications and has established a new base in the US as of 2015.
Process: As stated, the Arcam EBM process builds functional metal parts layer by layer using metal powder. What differentiates this process from all other metal 3D printing processes is that the powder is melted by a powerful electron beam (typically around 3,500 watts) to produce precise, often complex, geometric shapes directly from a 3D CAD model. Due to the use of the electron beam as the heat source, parts are necessarily built under vacuum conditions and at elevated temperatures.
Platforms available in 2016:
- Arcam Q10
- Arcam Q20
- Arcam A2X
Materials:
- Titanium Ti6Al4V / Titanium Ti6Al4V ELI
- Titanium Grade 2
- Inconel 718
- Cobalt-Chrome, ASTM F75

Advantages of the EBM process:
- Low level of internal defects.
- Good material properties, in particular fatigue properties.
- No limitations in chemical composition.
- Minimal residual stresses due to high process temperature
- Little waste material: virtually all excess powder can be recycled.
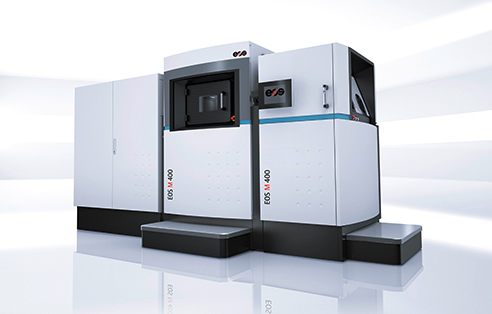
DMLS
The Direct Metal Laser Sintering, or DMLS, process belongs to EOS Gmbh
Electro Optical Systems. The history of EOS is somewhat more complicated than that of Arcam. The company was founded by Dr. Hans J. Langer and Dr. Hans Steinbichler in Germany in 1989, with Steinbichler bowing out the following year and Dr Langer still at the helm today. EOS originally developed stereolithography (SL) polymer resin additive processes; with laser sintering not emerging from the German manufacturer until 1994 when it commercialized its EOSINT equipment for plastic powdered materials. Over the years a great deal of litigation has taken place, largely in the background and particularly around the SL process, however the company’s commitment to R&D has never faltered and the first EOSINT platform for metal materials was unveiled in 1995. At this time it is fair to say the metal process was rudimentary and no where near the sophisticated, production grade process that it is today. Moreover, during its 20+ year history, EOS has greatly expanded its materials development and has the broadest metal material palette for AM, including a partnership agreement for the processing of precious metals with Cooksongold, established in 2012.
Process: DMLS is the oldest industrial metal additive layer manufacturing process that uses a precise, high-wattage laser to “sinter” powdered metals and alloys to form accurate, complex and fully-functional metal parts directly from CAD data. Today, the sintering terminology lingers due to it being the historical proprietary process name given by EOS rather than it being an accurate description of the current process, which actually involves almost complete melting of the metal powder to produce fully dense parts. Thus, it is also pertinent to note that the DMLS process is very similar to the laser melting processes of SLM Solutions, Realizer and Concept Laser et al.
Machines available:
- EOS M 100
- EOS M 290
- EOS M 400
- EOS M 280
- Precious M 080 (via Cooksongold)
Materials:
- EOS MaragingSteel MS1
- EOS StainlessSteel GP1
- EOS StainlessSteel PH1
- EOS stainlessSteel 316L
- EOS StainlessSteel CX
- EOS NickelAlloy IN718
- EOS NickelAlloy IN625
- EOS NickelAlloy HX
- EOS CobaltChrome MP1
- EOS CobaltChrome SP2
- EOS CobaltChrome RPD
- EOS Titanium Ti64
- EOS Titanium Ti64ELI
- EOS Aluminium AlSi10Mg
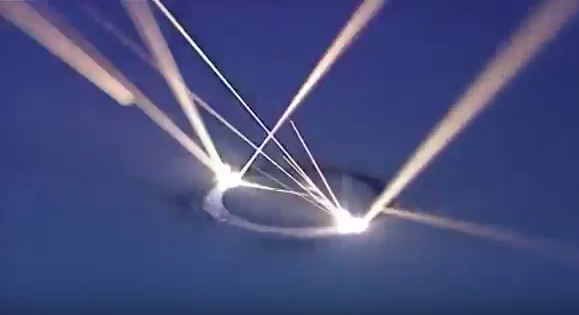
Advantages of DMLS:
- A broad range of metal materials.
- Finer layer thickness (typically 20–40 µm, compared with 50–70 µm for EBM).
- Better accuracy as a result – typically DMLS produces a smoother surface finish than EBM. Raw DMLS parts have a surface finish comparable to fine investment cast parts.
Part two of this series will compare the two processes directly.