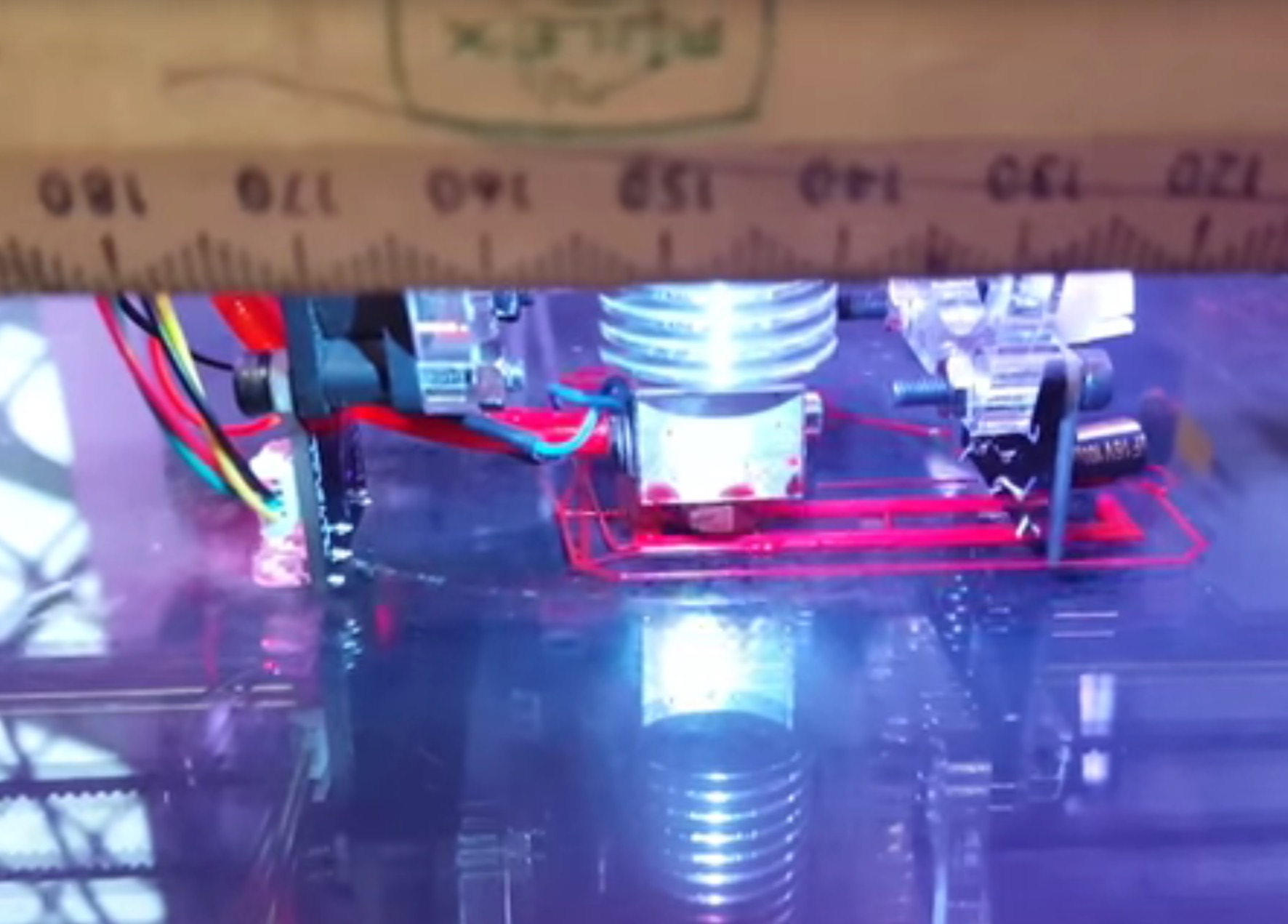
Someone has devised a method for performing dynamic error correction on 3D printers to ensure the nozzle is always placed precisely where it should be.
The problem is one well familiar to operators of less-than-perfect desktop 3D printers. Suddenly, in mid-print, the axes seem to have shifted, and the print is ruined when the top half is 2cm to the left of where it should be.
This kind of problem results from issues in the motion control system of the 3D printer, most often from slipping belts. It can also be caused by motor problems on one of the axes, or in some cases, poorly extruded material snags the extruder as it moves by and pushes the extruder off course.
Engineer Chris Barr of Adelaide, Australia’s solution involves the use of a magnetic encoder to track motion on each axis.
Once a problem is detected, as in, the extruder isn’t where it’s supposed to be, the software automatically moves the extruder to the correct position. Don’t believe me? Watch this video, where the extruder is rudely pushed away from its intended path:
Certainly this is not the perfect solution, as the recover will almost always leave an extra strand or two of filament in the wrong places, but they can be trimmed off after the print successfully completes. This is certainly better than the alternative, which is print failure – and wasted material.
While this particular recovery approach has now been proven in a technical sense, it remains to be integrated into any 3D printer I know of.
Until it is, however, you’ll have to rely on the traditional methods for extruder reliability: regular maintenance, lubrication, cooling, tuning and tightening your belts.