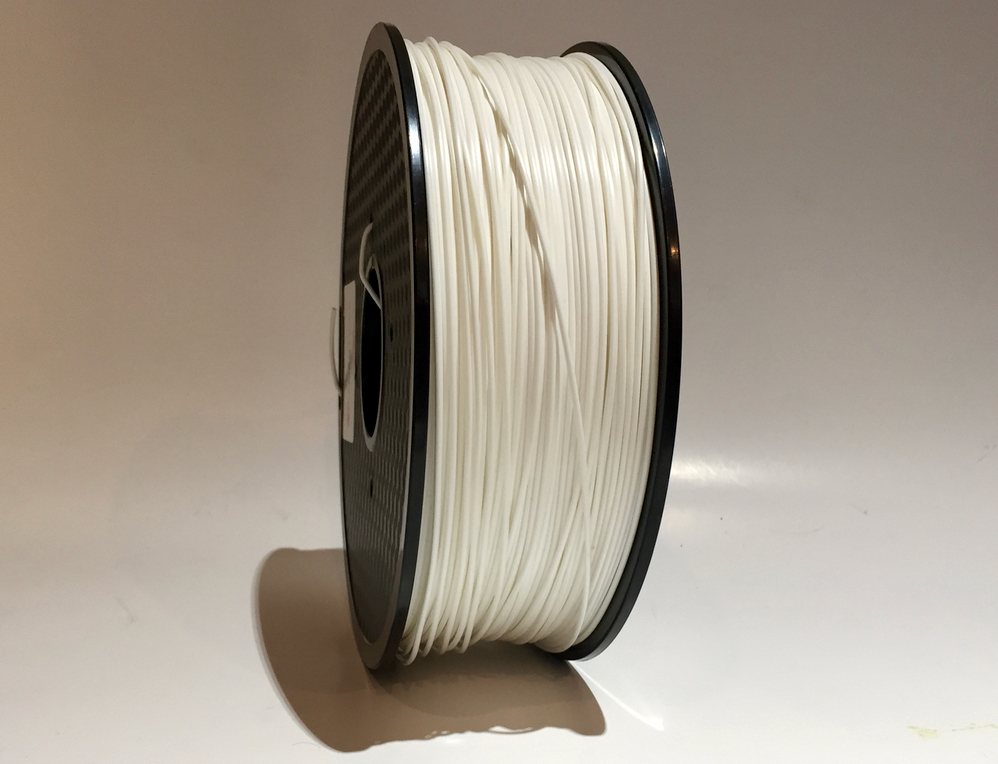
There are two major plastics used for dissolvable support structures in desktop 3D printing, but neither is perfect.
Early on in the development of 3D printing it was realized that layer-by-layer builds had an inherent issue: some geometries include features that would have “nothing” underneath them. This necessitated the need for inclusion of “support structures” to hold up these portions of a 3D model.
But then the fun begins: how exactly do you create support structures in the best way?
Single extruder machines simply added support structures using the same (and only) material available. This excess material is simply trimmed off after the print completes. This definitely works, but has a couple of major problems:
Cannot be used for internal supports where the support structure cannot be removed – say from the interior of a cube.
Leaves unsightly marks on the print where the support structure attached.
Then the idea of dissolvable support material emerged. At first, you’d think this is a really good idea: just print and toss your print in a liquid and let chemistry do the work. However, it turned out not be exactly the best option.
There are two plastics commonly used for dissolvable 3D printer support material, the first being PVA, or Polyvinyl Alcohol. It’s a water soluble material that can be extruded from a second hot end on appropriate 3D printers during a print operation to create dissolvable support structures.
Because PVA is dissolvable in water it’s very easy to remove support. You can increase the dissolve rate by heating and agitating the water slightly.
But that’s AFTER you print. While you print PVA, there can be many problems, as it’s a very tricky material.
PVA is notorious for absorbing water vapor from the air. Worse, when it does, it can become slimy and unsuitable for 3D printing. This means you must diligently store your PVA in air-sealed bags between prints, or the PVA goes bad.
Worse, it is temperature sensitive. If you get temperatures too high, it chemically reacts and can easily cause a jam in your extruder.
Finally, it doesn’t stick very well to print surfaces.
There are a few variations of PVA on the market that attempt to solve some of these issues, but it appears no one has completely done so yet.
That’s one option, and it’s not great. The other option is HIPS, or High Impact Polystyrene.
It’s used in the same manner as PVA to print dissolvable support structures. However, there’s one difference: you cannot dissolve HIPS in water; instead you must use Limonene. Limonene is a commonly available house cleaning product – and it smells wonderful, too.
Simply drop your HIPS-supported print into the Limonene and some hours later the HIPS will be gone. HIPS does not have nearly as many issues printing as PVA does.
But HIPS requires Limonene, which doesn’t come out of your kitchen tap. You’ll have to buy it and that’s a cost that adds to your printing operations. Worse, I’ve seen some evidence that you cannot reuse a batch of Limonene on subsequent prints, so you may have to buy a lot of Limonene, depending on how much you print.
These are the tradeoffs one must analyze when selecting a dissolvable support material.
At least until the need for support structures goes away – which may be sooner than you think.