While most of the focus on 3D printing lately surrounds plastic and metal 3D printing, there is another potentially powerful material: ceramics.
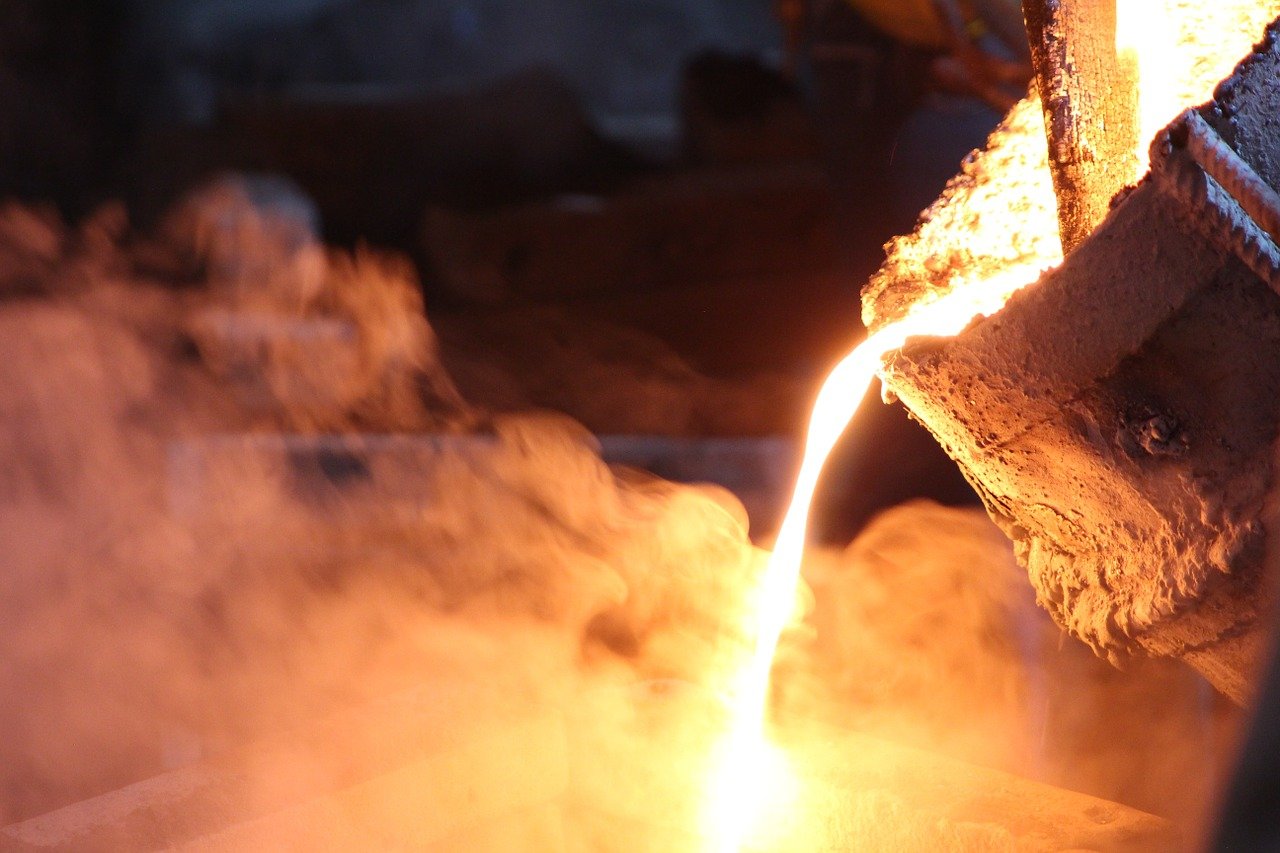
There have been a few ceramic 3D printing initiatives, such as that of 3D Systems (acquired from Figulo) and now apparently shut down.
That process was largely used to 3D print small ceramic objects, such as coffee mugs.
There are larger examples of ceramic or clay 3D printers, but most suffer from geometry problems where the shape 3D printed is constrained by the “slump” of the extruded wet clay. If you look at the prints from such machines, they are typically simple flat walls or gently sloping vases. Nice, but restricted in usage.
Ceramic as a material has properties quite different from conventional 3D print materials, including:
- Extremely hard
- Extreme resistance to heat
- Extreme resistance to chemicals, liquids, vapors and vacuums
One property it does not have is the ability to flex.
Nevertheless, these properties make it an ideal material for many applications requiring those specific characteristics.
And as a heat-resistant material, it can be used as a mold for casting liquid metal or plastic. This is where I believe it could become quite powerful in the future.
Imagine if a ceramic 3D printer were developed that could print arbitrary shapes with smooth surfaces, just as plastic 3D printer could do. With such a machine, you could produce not only very complex ceramic parts, but also complex molds for plastic and metal objects.
Yes, this is done today, but there are more steps to do so. If you could directly 3D print the ceramic mold you’d avoid some steps, making the process more efficient and possibly opening more more applications as a result.
However, at this point there really aren’t any commercially available ceramic 3D printers of this type that I am aware of, although the work of Olivier van Herpt could eventually become such a machine, he’s not there yet.