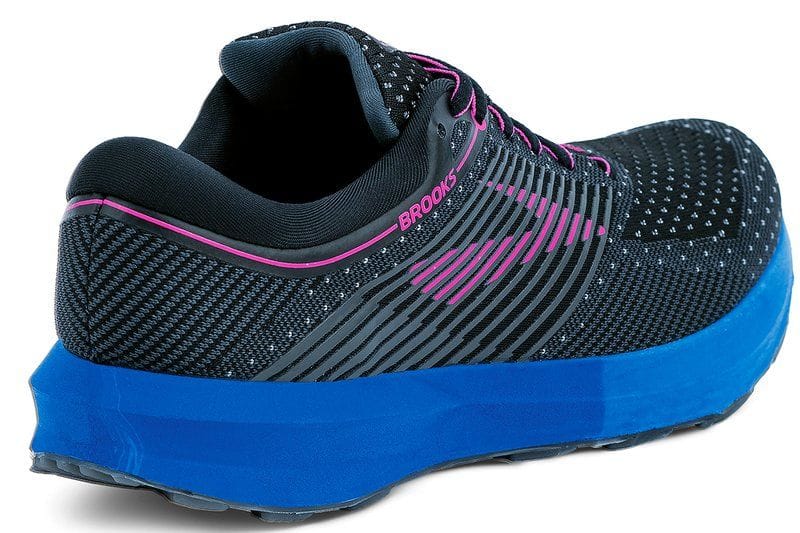
We’ve heard a lot about “personal” 3D printing in the past, but perhaps it’s time for “personalized” 3D printing.
By “personal” 3D printing, I mean the ownership of a 3D printer and production of objects for personal use. This was, and probably still is, the vision for consumer-based 3D printing. While there was a great deal of buzz about the concept a few years ago, it didn’t take off for a number of reasons.
But underneath that concept was a perceived need: making things that “fit” the requestor. “Fit” as in, “works better for me than the a mass manufactured version”.
Mass manufacturing is almost always less expensive than 3D printing, but it holds a key restriction: every item must be the same. That’s where the cost advantage comes from.
While in some applications it is highly desirable to have identical parts, for example, the mechanical components inside a machine, it is less desirable for fashion or body function items.
Fashion items are valued by the whims of the public. Their tastes come and go, creating trends and retreats from different style approaches. It’s desirable to be different! It’s an entire industry that in the end will probably make enormous use of 3D printing if innovators can figure out a way to make it works smoothly and economically.
Body function is another obvious area of personalization, in a very literal way. Your feet, your hands, your face and the rest of your body is almost certainly unique among the human population of the globe. If only there was a way to enable 3D printing technology to match body requirements with objects.
I believe this is coming, and coming strongly. Today we see the very early first steps in this process.
A story in Fortune describes a new venture at Brooks, the shoe manufacturer, where they’re attempting to apply this concept to footwear.
Shoes are a notoriously difficult item to produce to match the needs of a specific person, because everyone has very different feet, and different ways we use them. And we use them a lot – most people take many thousands of steps every day of their lives.
A company like Brooks, in the past, could only make an assessment of the needs of an individual in order to determine which category of mass-manufactured shoes could best be used by that individual. Brooks uses a relatively sophisticated measurement that takes into account personal motion, structure and timing to create what they call a “Run Signature” to understand the runner’s profile. While that’s significantly better than randomly choosing a shoe, the wearer is limited to the designer’s whims of shoe categories.
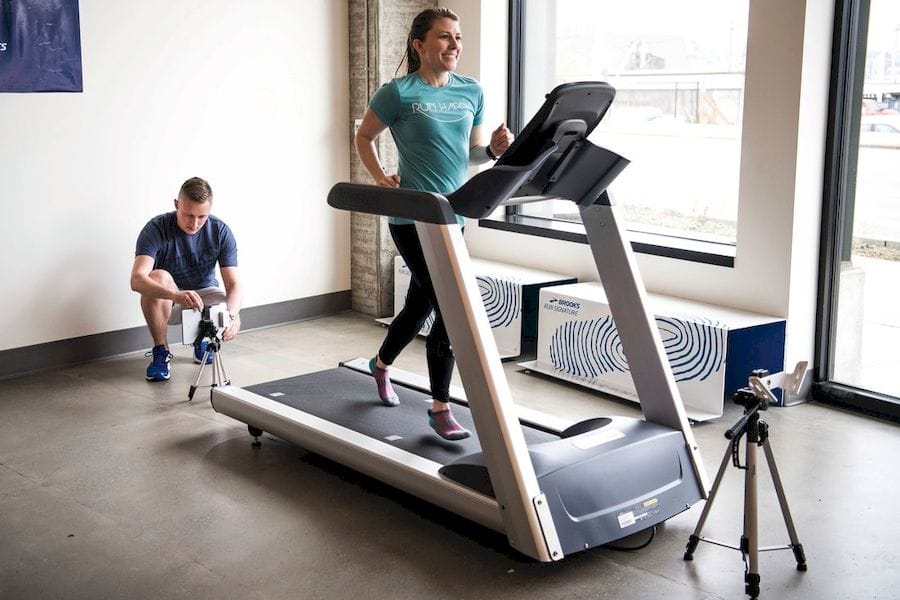
Brooks has teamed up with HP to offer a way to truly custom-build shoes for individuals by combining the Run Signature knowledge with HP’s FitStation. This is a device that measures the strike force at multiple locations on each foot as strides are taken. This can then be translated into a custom density map for the shoe sole for that individual to optimize their stride impact.
This is a key step, but it isn’t yet mass customization through 3D printing. But I believe this is a big step towards that goal. If Brooks and HP can measure humans to determine polyurethane density, it’s a far shorter step to 3D printing the sole directly.
And how would you do that 3D printing? With metamaterials, of course.
Via Fortune