![[Beam Hardening, courtesy of Radiopaedia ]](https://fabbaloo.com/wp-content/uploads/2020/05/image2_img_5eb091fa3b843.png)
Advanced Manufacturing is the use of innovative technology to improve products or processes. Today, these advancements are especially prominent in the healthcare industry, where we see innovations in prosthetics, dentistry, and medical models.
I recently had the opportunity to speak at RAPID + TCT in Detroit to provide a snapshot of what can be achieved in the medical industry with the technology available today including 3D scanning, DICOM, 3D printing, and post-printing support removal and finishing techniques. Let’s take a look at some.
3D Scanning
3D Scanning technology (and Structured Light Scanning in particular) is well-suited to applications within the realm of cosmetic and other prosthetics requiring 3D capture of external anatomical data. 3D scanning lets you quickly collect a mesh file of the part of the body and then, using surface-to-solid body conversion methods found in 3D CAD software like SOLIDWORKS, turn that patient data into solid CAD models.
These solid models can be used directly or manipulated to create lattice structures, generatively designed structures, and other useful textures. Users can then reconvert the file into a mesh (e.g., STL) file for 3D printing.
DICOM Segmentation and Processing
Digital Imaging and Communications in Medicine (DICOM) files are patient-specific anatomical data taken from MRI, CT, ultrasound, and other medical imaging technologies used to capture internal patient anatomy.
For DICOM to be used for 3D printing, we must first overcome a few restrictions common in modern-day medical scanning.
Factors that affect scanning quality include:
-
Beam hardening — the contrasting of streaks with bone imaging (a problem with metal implants)
-
Blooming — calcium deposits and heterotopic bone appearing larger than they are
-
Radiation exposure (the longer the scan is, the better the imaging) works best on cadavers (per the ALARA (As Low As Reasonably Achievable) principle)
-
Timing of the scan (imagine trying to scan a heart while it’s beating) also known as bolus tracking utilizes a radio-opaque media which is clearer contrast in the imaging
-
Layer thickness
![[Blooming, courtesy of DARConline ]](https://fabbaloo.com/wp-content/uploads/2020/05/image3_img_5eb091fad5fd0.png)
Once usable scanning data has been obtained, it is necessary to choose the appropriate DICOM segmentation software and follow the standard DICOM processing procedures shown in the tables below.
After selecting and segmenting the intended patient anatomy, materials and colors must be chosen to create a structure. Applications for this kind of DICOM to 3D print data are pre-surgical testing, patient communication, and medical training and education.
3D Printing
3D printing offers a multitude of different materials and methods to create physical parts. Below are some of the basics surrounding FDM (Fused Deposition Modeling) thermoplastics and PolyJet photopolymers.
FDM Thermoplastics
Certain FDM materials such as ULTEM are sterilizable, opening up applications for drill guides, cutting guides, and tool fixtures.
PolyJet Photopolymers
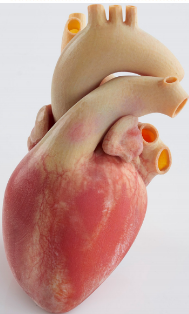
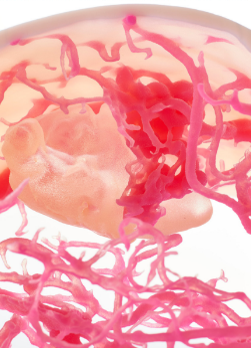
Top of the line PolyJet 3D printers are capable of multi-material, multi-durometer, and multi-color part assemblies with customization down to the voxel. With these capabilities, obtaining segmented anatomical data and specific colors, opacities, and shore values to different anatomical structures and tissue types is possible.
Post-Processing
Both in dental and medical models, support removal is extremely important. PolyJet models, specifically that are created with high complexity and thin anatomical structures, have a high risk of damage and breakage during the support removal process.
Geometries similar to the larynx model above have incredibly small features that can easily break during traditional support removal processes. It is ideal to perform bulk removal whenever relevant, as well as using appropriate soluble support removal tanks to gently agitate the rest of the support structures away, releasing the final model. Companies like PostProcess Technologies have created focused technologies to address these challenges.
Surface Quality
Surface smoothness can be measured as roughness average (Ra), or in other words, the average of surface heights measured across a surface. Raw, as-printed, typically require additional post-processing to improve the surface finish. For medical devices, metal finishing or surface smoothing quality depends on the model material of the part, lubrication chemicals, and the tumbling media. PostProcess Technologies equipment makes it easy to smooth any FDM, PolyJet, or 3D printed medical grade metals like titanium.
Gradient surface finish plays an important role to highlight, for example, bone tissue which requires a textured surface to adhere to. On the flip side, making medical models too smooth could ruin applications. For example, over-smoothing a dental mold could affect dimensional accuracy and inhibit the release of the vacuum-formed retainer.
All of the technology listed above plays a vital role in additive manufacturing in healthcare today and will continue to advance and evolve for years to come. Being in the middle of an industrial revolution means we can continue to expect exciting medical breakthroughs for doctors, patients, and technologists.