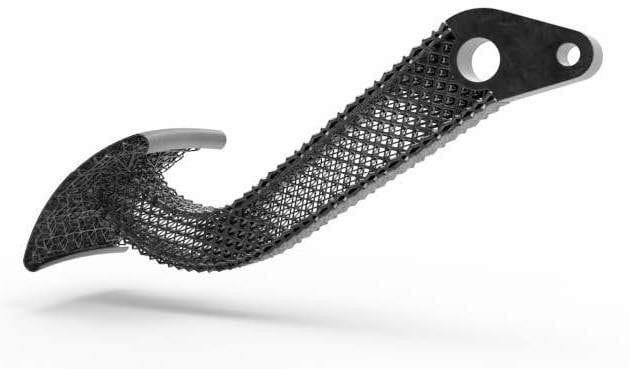
The 3MF Consortium announced a new feature that should have a significant effect on the use of 3D printing.
The 3MF Consortium is a non-profit industry group composed of most of the leading 3D printing companies, whose mission is “Advancing the print industry with a universal specification for 3D printing.”
Their mandate was a reaction to the rather stagnant state of the .STL format commonly used in 3D printing to represent the 3D model to be printed. This now aging format was invented decades ago to facilitate the first primitive 3D printers, but now exhibits a series of problems. That’s largely due to the advancement of 3D printing technology that has progressed well beyond .STL’s ability to match.
The Consortium’s major output to this point is the very flexible .3MF format, which is intended to replace .STL and other less-than-optimal 3D model file formats. It’s an XML-based format that enables it to be extended as necessary and adapt to new scenarios that may emerge in the future.
Now they’ve announced a specific extension to .3MF: the “Beam Lattice Extension”, a means of describing complex lattice structures.
Why announce this seemingly obscure feature? There’s a very good reason.
.STL and similar file formats describe the 3D object with a series of adjacent flat polygons that wrap the object’s entire surface. Many flat polygons are required to describe a curved surface is one of the implications.
Another implication is that .STL must explicitly describe each and every surface polygon. This becomes highly problematic when you’re working with more complex geometries, as the number of polygons skyrockets.
Now imagine you’re attempting to create a revolutionary aerospace component that is significantly lighter – due to extensive use of internal lattice structures. Perhaps it might be something like the sample image at top.
If using .STL to describe this part, the curves in the enormously complex lattice will require truly gigantic numbers of polygons, driving the file size to immense proportions. Any digital surgery on this file could break the software simply due to size limitations and machine capacities.
That’s what the new Beam Lattice Extension attempts to resolve. Rather than explicitly describe each and every curve of the extensive lattice surface, a mathematical description of the lattice is used to generate it dynamically.
The Extension provides for a number of parameters to describe different forms of lattices, which takes up significantly less file size than a .STL equivalent.
This should make life significantly easier for those designers creating lattice-based components, and that is precisely where most of the interest in 3D printing technology has been recently. Driven first in aerospace, for obvious reasons, lattices are now entering a number of other markets, even including sport shoes.
One potential drawback is that the lattice descriptions possible are not infinite, at least in the current iteration of the Extension. I believe there will be great value in highly variable complex lattice structures, but you might not be able to describe them in 3MF, yet.
Nevertheless, this is still a very good step forward, and another encouragement for everyone to move to adoption of .3MF format from the aging .STL.
Via 3MF Consortium