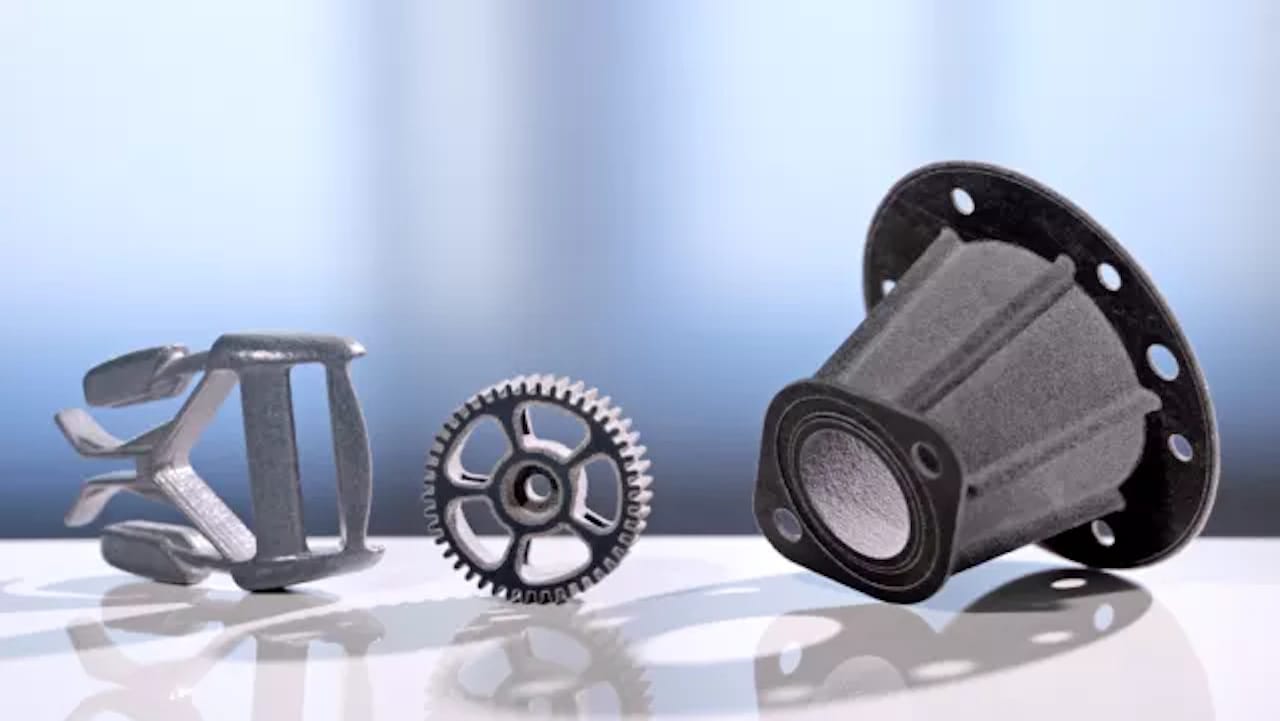
In the last few years, a number of exciting new technologies have emerged in the 3D printing industry that promise the integration of additive manufacturing (AM) into the larger world of manufacturing, including Carbon’s Digital Light Synthesis and HP’s Multi Jet Fusion (MJF).
Before these existed commercially, however, there was high speed sintering (HSS).
Invented and developed by Neil Hopkinson and his team while he was performing research at Loughborough University and, later, the University of Sheffield, HSS uses infrared lamps and an inkjet printhead to outpace other AM technologies like selective laser sintering (SLS). Hopkinson is now at inkjet printhead manufacturer Xaar, where he leads the company’s 3D printing division.
As Xaar looks to fulfill its stated 2020 vision, Hopkinson and his team have just cut the ribbon on Xaar’s new 3D Centre in Nottingham, England. ENGINEERING.com reached out to Hopkinson to learn just what this 2020 vision looks like and how HSS will play a role in it.
What is HSS?
HSS was developed as a means of bringing down the cost of SLS parts in order to make 3D printing competitive with mass manufacturing technologies like injection molding. By replacing the costly laser used in SLS and increasing the throughput of the machine, it’s possible to sinter parts at a pace and cost that could potentially compete with injection molding.
In HSS, an inkjet printhead deposits a black infrared radiation absorbing ink onto a bed of thermoplastic powder, outlining the desired shape. An infrared lamp then heats the powder, causing the particles to fuse.
Read more at ENGINEERING.com