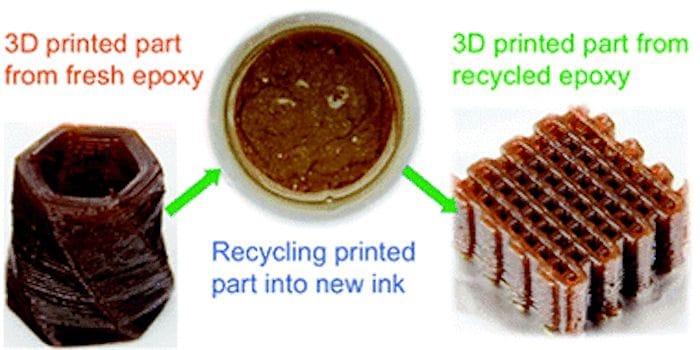
A method has been discovered that allows moderate recycling of photopolymer 3D prints.
Researchers at the Digital Manufacturing and Design Centre of the Singapore University of Technology and Design have developed a technique that has eluded others for some time.
Most non-metal 3D printers use one of two types of plastics: thermoplastics, which can be softened and reshaped many times. Typical thermoplastics include ABS, PLA, PETG and the usual filament-based materials.
The other type of plastics is a thermoset, which is a material that remains in liquid form until sufficiently stimulated, whereupon it forms strong bonds and solidifies. Typical examples of this include any photopolymer resin that hardens upon exposure the appropriate frequency of light (usually ultraviolet).
Thermoplastics are obviously recyclable; you simply melt them down and go again. To this end we’ve seen multiple desktop 3D printer recycling systems. These will shred undesirable 3D prints into fragments, where they then enter an extruder to reproduce new filament. There are arguments about the quality of recycled filament, but these largely center around the quality of the machinery performing the recycling, rather than the ability of the thermoplastic to do so.
Meanwhile, there was no equivalent for thermosets. You print it, you keep it. Or throw it out, in which case you’re adding to civilization’s permanent waste pile. Not a good plan, but no other options available, at least until now.
The researchers have developed a liquid polymer material that is somewhat recyclable if used in a specific process.
The liquid material is first “slightly cured” to begin the process, followed by the printing process itself. Heat is used to cure the material during printing. The resulting part is not completely “set” and requires a post printing stage of “oven curing”, which delivers additional heat to the material.
That appears to be a more or less standard 3D printing process; even the post print curing stage is frequently seen in UV-cured photopolymers, where there is a UV chamber to finalize the solidification.
But then this material is recyclable. The researchers explain that the printed parts can be placed in a sealed chamber with ethylene glycol and heated. Eventually (they don’t say how long) the printed part breaks down into the same liquid material that was originally used to print the part.
They say:
Our experiments demonstrate that the ink can be printed four times and still retains very good printability. In addition, the vitrimer epoxy can be used for pressure-free repairs for the 3D printed parts.
Four iterations of recycling doesn’t sound like a lot. But in fact low cycle counts are typical for many so-called recyclable materials. Paper, for example, is sometimes divided into “recycled” and “fresh” at retail outlets.
I’m a bit skeptical as to the utility of this material. It’s not clear whether the other engineering properties of the polymer are suitable for use in actual applications. What is its heat deformation temperature, for example? Is it chemically resistant? I suspect a side effect of its recyclability will be relatively poor characteristics in other aspects. In this case, if heat is used to dissolve the part, how heat resistant can it be?
And then there’s cost. Users will only take on this material if the total cost of the substance (with reuse procedures accounted for) is less than the cost of buying “fresh” material from traditional sources.
Of course, this is only a research project and we cannot know what the costs of the material might be. However, resins can be made relatively cheaply, so it is possible this may work if properly commercialized.
Via Royal Society of Chemistry