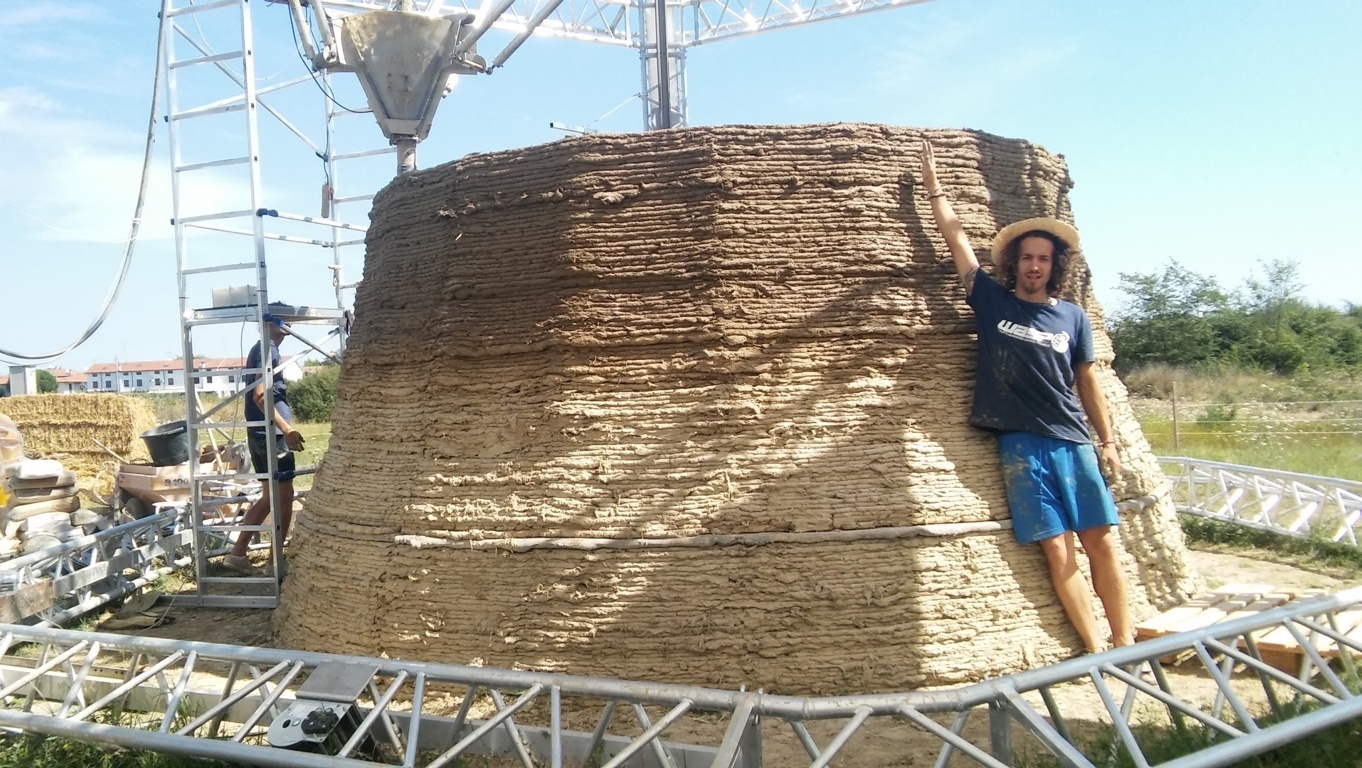
Italy-based WASP has been experimenting with their building-sized BigDelta 3D printer.
The BigDelta is a massive 12m tall and is capable of 3D printing large exterior structures in clay. It’s not a product (yet), but their goal is to provide a means to quickly 3D print buildings in third world countries where construction is challenging.
In the experiment, they’re attempting to 3D print a soil and straw building, essentially an extremely large vase shape. But as the experiment proceeded, they encountered a number of problems, some of which have never been faced by 3D print technologies previously.
WASP explains:
The list of the problems faced and constantly solved every day in the experimental camp in Massa Lombarda (Ravenna) is too long: let’s mention some of them. The main goal was to develop an extruder able to lay down scores of mixtures, to verify if the machine mechanism was able to stand a continuous work of material deposit, to solve the problem of the material loading after a significant high, to supervise the extruder during the printing phase, to face printing interruption and recovery, also connected to material pick up, to protect the wall from the rain in case of storms, and more. These are some of the difficulties we faced and solved.
Outdoor 3D printing is clearly a different kind of animal, but I’m very happy that someone is investigating the process and developing solutions.
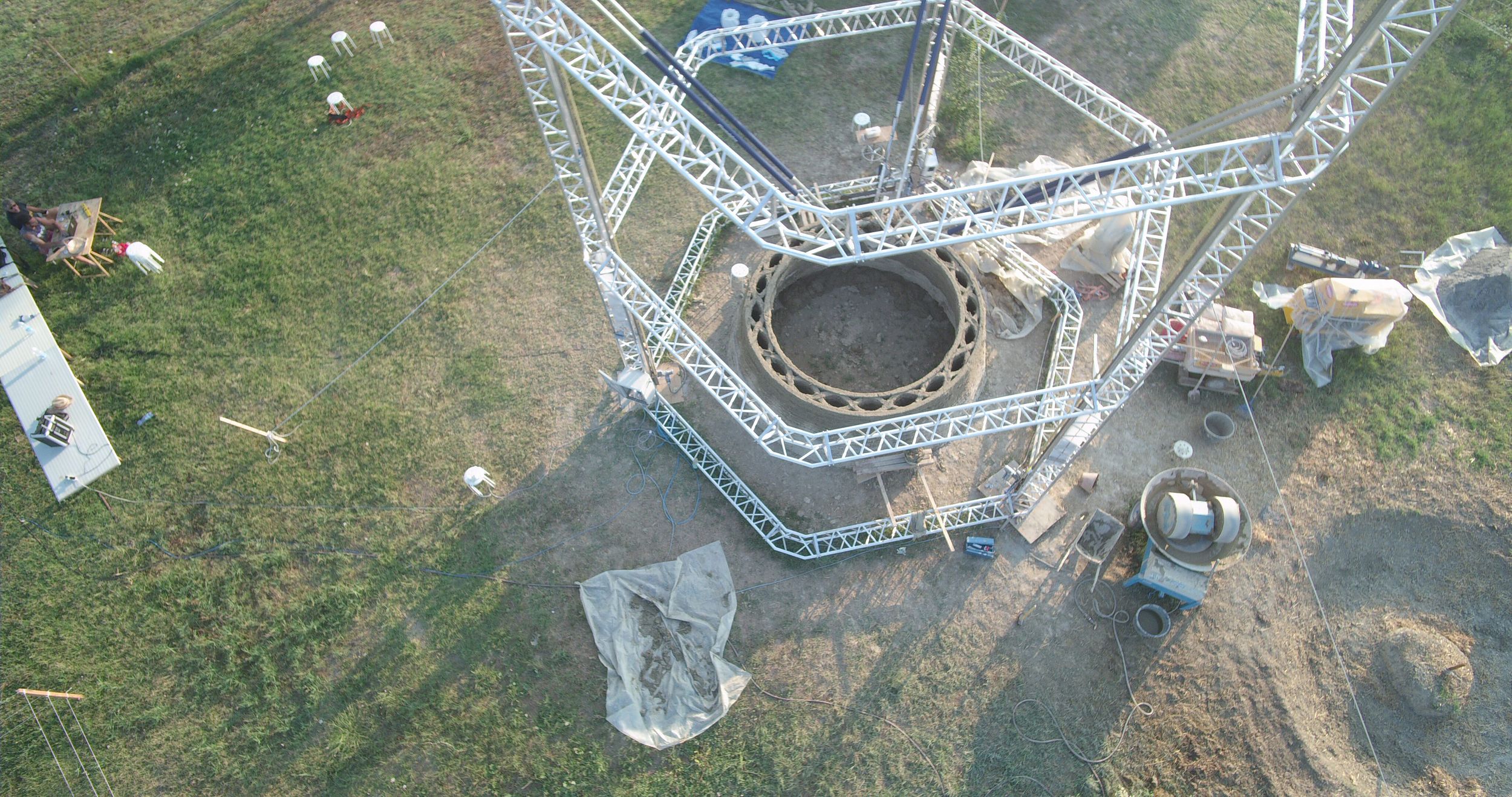
The team has produced some statistics for their progress thus far that illustrate the scale of their project:
270 cm height of clay and straw wall
5 meters diameter
40 tons of material!
135 layers printed, with an average weight of 300 kilos each
20 minutes time to create a layer.
2 cubic meters water consumed
200 Kwh of electricity required
And this comes to the most important analysis: the cost of the structure, which is vitally important to the project. They’re intending on producing an extremely inexpensive solution suitable for poorer regions.
They report the following:
- 32 Euros for the electricity
- 3 Euros for the water
- 10 Euros for the straw
- 3 Euros for motor hoe’s gasoline
- For a total of 48 Euros (USD$54). That’s pretty cheap, but they also explain that if you were to knead the soil mixture with feet instead of a motor unit, you’d save 90% on the electrical power!
Progress! I’m looking forward to the final totals when the project concludes.
Via WASP