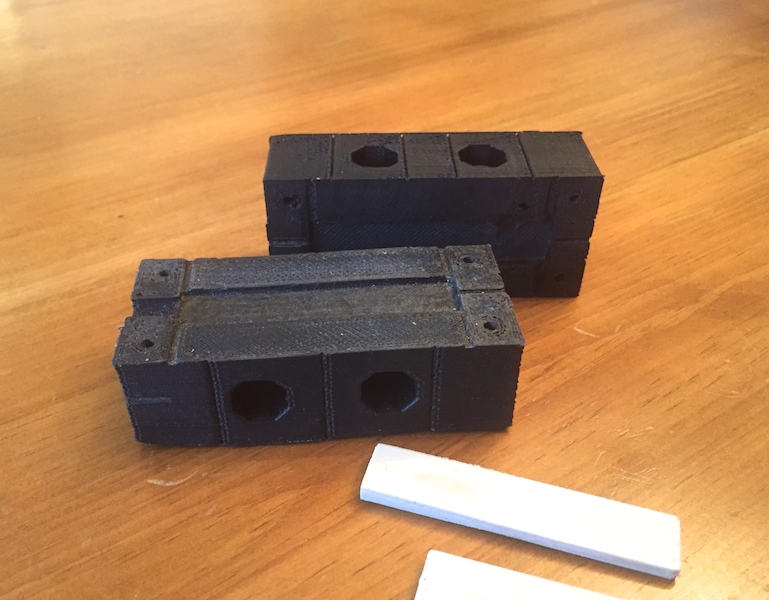
Yet another interesting 3D printer filament has been announced by Avante Technology: Injection Molding Grade Filament.
One of the oft-heard complaints about 3D printing is that of strength. “3D printed parts are nowhere near as strong as injection molded parts”, they say.
And that’s largely true. Typical 3D printing processes produce objects layer by layer, and while that’s an incredible advantage to create unusual geometries, it also introduces the challenge of layer adhesion. Layers, it turns out, are the weakest part of a 3D printed part; that’s where stress will likely break the part.
Injection molding overcomes this by simply not having any layers, as the liquid resin fills all portions of a mold uniformly. Thus, there is and always will be significant interest in injection molding.
But there’s one problem: injection molding can be expensive, as usually a pricey metal mold must be created before any injections can take place. In some cases, such molds can cost several tens of thousands of dollars each. Oh, did I mention that you might need to do several before you get it right?
So there’s a lot of motivation to be able to instantly (relatively speaking) 3D print molds for an injection process. The problem has been that materials typically used in 3D printing are too weak to withstand the higher pressures of injection molding or are of materials that would deform at injection temperatures.
Now Avante Technology attempts to overcome these with their new “FilaOneTM GRAY Advanced Composite Injection Molding Grade filament”.
According to their press release, the material was designed to achieve the following characteristics:
- Printable on specified desktop FDM printers costing less than $10,000.
- Able to with-stand the temperatures and pressures of injection molding process
- Surface of printed molds can be polished or textured
- Mold cavity surface supports use of off-the-shelf release agents
- Durable enough to handle the heat fluctuations of many injection molding cycles
And that’s the really interesting part: while a metal mold might be able to withstand injections almost forever, a plastic mold will certainly not. They will have a lifetime based on their strength and other characteristics.
Bob Zollo, CEO of Avante Technology, explained that the new filament works quite well:
After experimenting with our standard formula, which is good enough for printing simple tools, we created a variant that is optimized for improved surface proportion and longer mold life.
This material will enable makers and manufacturing engineers to quickly design short run tooling and produce dozens of parts quickly and cheaply using a broad range of conventional thermoplastics.
So that’s how it works: 3D print a mold, polish it and then use it on as many injections as you can. Then just 3D print another mold and repeat.
While you might think this is a more difficult approach, it will almost certainly be far less expensive than using the traditional metal mold approach, unless we’re talking about a large number of units. For short run injection molding, this could be a great way to start. Zollo explains further:
Our printed mold approach is ideal for molding 10 to 1,000 parts at a cost that is 50% to 90% cheaper than conventional methods. Our composite materials are developed and produced here in the USA. Why spend more money for off-shore tooling and wait a month, when you can start injection molding in days using our American made material?
This new filament is not yet available, but apparently will appear this November. It will be sold as a kit containing an adhesion sheet to ensure this unusual material can stick to your print surface, as well as a 500g spool of the filament, all for USD$299.
Via ProForma