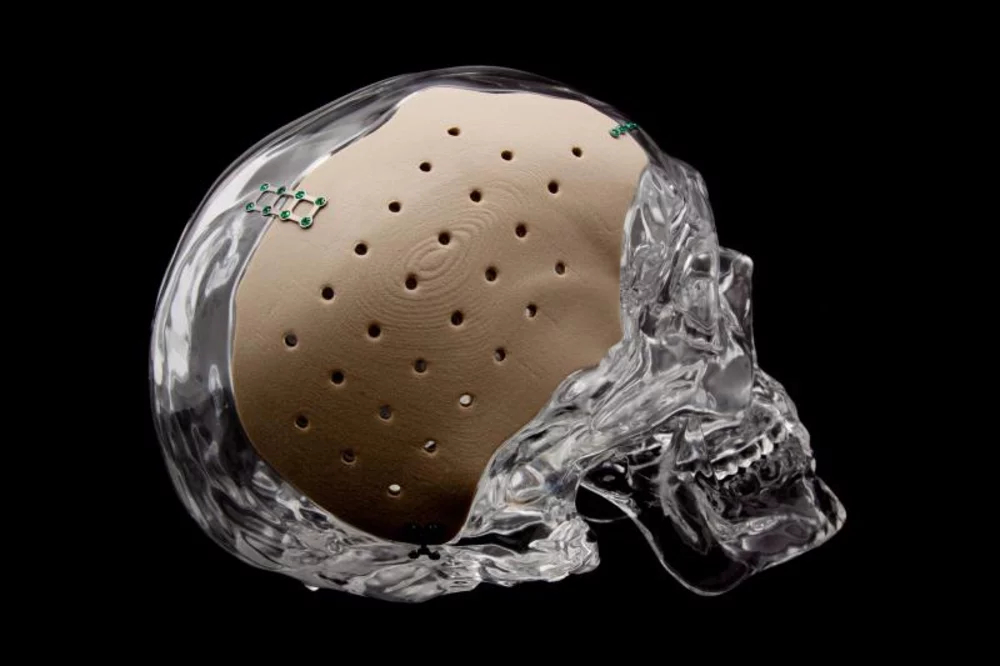
According to market research firm Markets and Markets, the 3D printing materials industry will be worth $1.4 billion by 2021.
In many ways, additive manufacturing (AM) is coming into its own in the industrial space and the key to unlocking its potential are the materials that it uses.
When it comes to mechanical properties, performance under high temperatures, and chemical resistance, there’s one family of polymers that rules them all: polyetherketone. One company in particular, Oxford Performance Materials (OPM), has built itself up on a foundation of polyetherketoneketone (PEKK) with its own PEKK material, dubbed OXPEKK.
So far, OXPEKK hasn’t steered OPM wrong, as the company has been enlisted to 3D print 600 components for Boeing’s space taxi, the Boeing CST-100 Starliner spacecraft. To learn more about this material and the company itself, ENGINEERING.com spoke with OPM CEO Scott DeFelice.
Building on the Power of PEKK
A semicrystalline polymer with a glass transition temperature of 162°C (323.6°F), PEKK is chemically resistant and exhibits good structural performance in high temperatures. For these attributes, PEKK has been used in industries as diverse as medicine, aerospace and oil and gas. PEKK can withstand the volatile chemicals of oil extraction and some of the extreme temperatures of an aircraft engine (though not top engine temperatures that can reach up to 2000°C). At the same time, the material is lighter and cheaper than aluminum, making it a cost-effective alternative in many of these high-performance industries.
According to DeFelice, OPM was founded as a materials science company in 2000 for the specific purpose of taking PEKK to market, though not initially intending it to be used in AM. Over the next seven years or so, the firm developed a wide range of processes and applications for PEKK. “If it’s melted or formed, we’ve probably done it and had a lot of exposure to it,” DeFelice said.
After selling the material in the biomedical, aerospace, semiconductor and oil and gas industries throughout the 2000s, DeFelice said that two industrial trends started to converge. In the mid-2000s, surgeons that had been using the company’s material in extruded form to machine spinal implants started asking OPM about the possibility of 3D printing PEKK. Meanwhile, as OPM sold PEKK as molded and extruded parts to the aerospace industry, the U.S. Air Force was exploring the concept of 3D printing with high-performance polymers for the F-35.
“Our material already had acceptance in these highly demanding markets, so the question we put to ourselves was, given our deep knowledge on material science, should we develop an AM technology? That’s what sent us down that road.”
Producing OXPEKK
“OXPEKK” is the brand name for OPM’s specialty PEKK material, while “OXFAB” and “OsteoFab” are the processes by which OPM manufactures components for the aerospace and biomedical industries, respectively. All of this falls under the umbrella of high-performance additive manufacturing, which OPM differentiates from other forms of industrial AM, due to the highly controlled method used for producing both the 3D printer-ready OXPEKK material and the additive parts for its customers.
Unlike 3D printer manufacturers that might start with a machine and then aim to develop a specific material powder for it, DeFelice described OPM as a materials science company. This gave the company a different perspective in developing OXPEKK for AM, as it explored the necessary additives and processing requirements to develop the material.
“[O]ne of the characteristics that distinguishes us from machine builders is that, to us, it all starts with basic physics, material science and polymer science,” DeFelice said. “We started with a pretty extensive set of experiments that took place over years to understand what in the material had to be to be right [for AM]. Details directly related to the process: how are you melting it, what fidelity do you have on the machines, what fidelity do you have on the laser, thermal controls, all of these very practical things. Once we had the fundamental material and fundamental process, we went down the road to optimize for structural performance and fidelity.”
With the processes and material developed, OPM acts as the part manufacturer for its clients as well. DeFelice does not see his company as a service provider, however. Instead, OPM aims to control its materials and processes to the extent necessary to serve the highly standardized industries of its clients.
“We’re truly a technology company,” DeFelice elaborated. “We don’t today sell the technology platform. Today we sell the end product. We go from the raw material to the side of a hospital bed with the implant and control all of the processes, technologies along that path. We go from the polymer reactor to the side of the aircraft, or spacecraft, and we do all of the activities along that path, from developing the material and the process, to making the part and managing the customer interface.
“In time, our model may evolve but what’s really important at this stage in any technology development is to ensure that we have complete intimacy with everything that’s happening, both from an IP perspective but also from technology optimization perspective.”
Read more at ENGINEERING.com