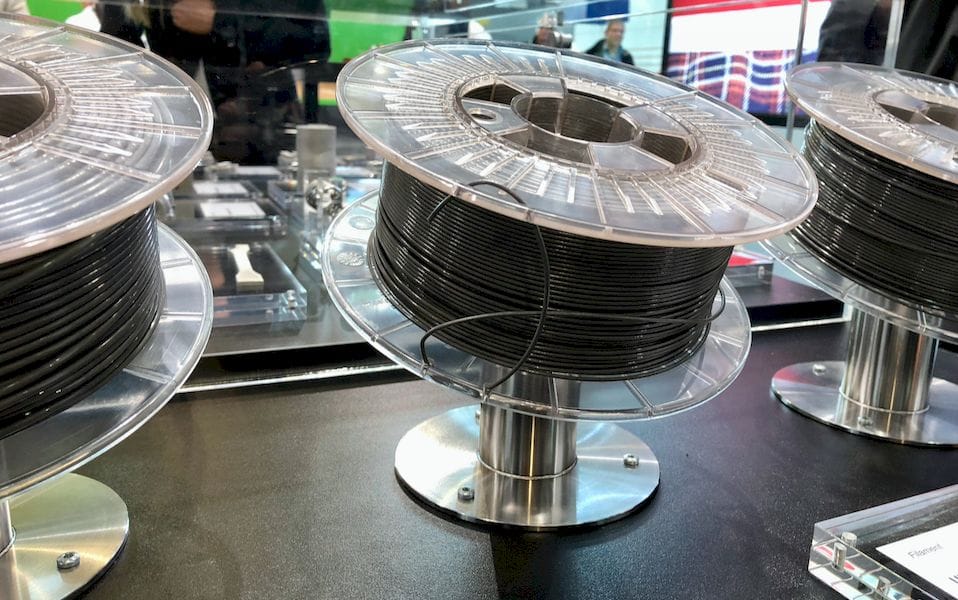
At FormNext we had occasion to visit BASF and came out very impressed.
There’s something interesting about talking to a very mature company in 3D printing, as a great deal of the players we interact with are startups, or have been around for at most ten years or so.
These “startups” are essentially still building their business and thus act in particular ways. Sometimes you see them acting very aggressively, sometimes desperately.
But then you run across a company like BASF.
We’ve written about them multiple times in the past year, so often that we even wrote a story about how many times we’ve been writing about them. It seems the chemical giant has been quietly observing the 3D print industry for some time, and after a series of experimental forays, has now pushed forward with a huge agenda in the space.
At FormNext the first item of note was simply the size of their exhibition stand. It was absolutely the largest size of any at the show, dominating the central portion of the main hall.
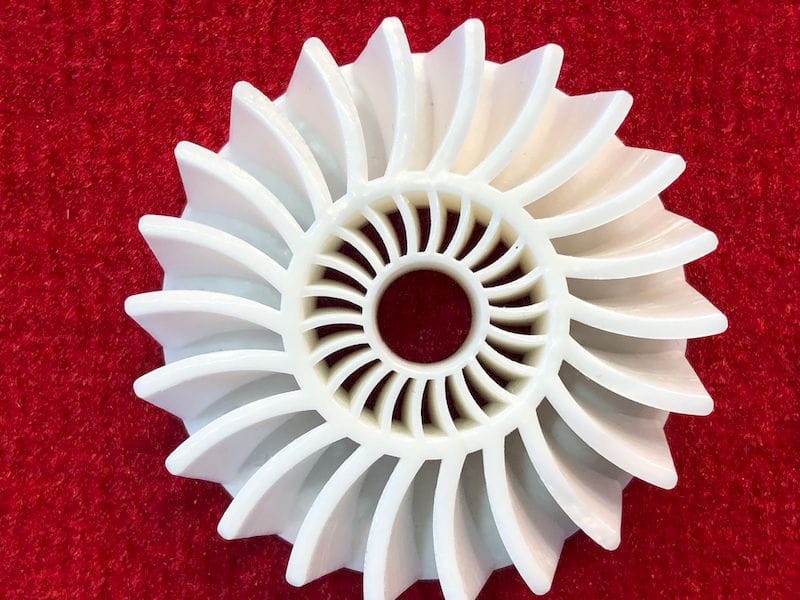
This is so utterly different from the startups, who typically begin one year with a small, poorly set up table, and slowly grow to a larger space in future years. No, BASF is already a gigantic company, ranked #94 in the world on one list I examined. Their revenue, USD$78B is likely more than every other 3D printing company combined, with the exception of HP, perhaps.
And now they’ve turned their attention squarely towards 3D printing.
In their booth we saw countless material types of all manner of equipment. They produce filaments powders, resins, photopolymers and pellets all suitable for 3D printing use by various types of machines and technologies.
They say they are “equipment agnostic”, and it is certainly true. They produce materials directly, but also provide “white label” materials for other companies to re-brand as their own.
But it’s not just money and size they bring to the table: BASF, who have been in operation since 1865 (Yes, one hundred and fifty two years ago!) have had decades – or even a century – to develop a highly mature portfolio of thousands of different polymers, many of which are suitable for 3D printing applications.
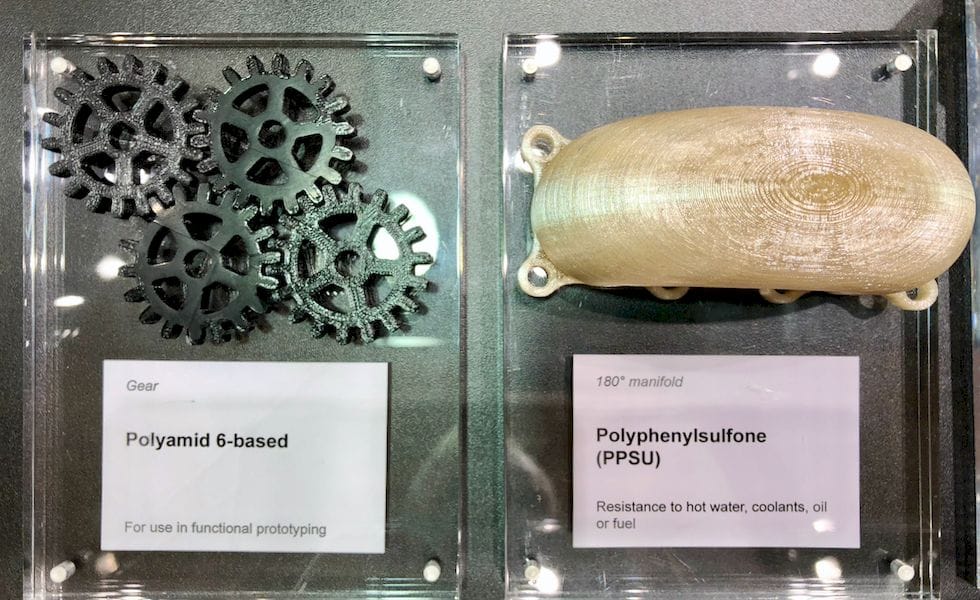
Their manufacturing capabilities are enormous and would dwarf the entire requirement for all 3D printing needs on this planet. They can make as much material as could ever be imagined by the industry.
Our discussions with BASF representatives indicated a very strong culture of working with clients to address their needs on a specific basis. They’re looking for partnerships now to deliver very particular solutions for unusual materials.
They can, for example, design a new thermoplastic that has resistance to flames and chemical attack. Whatever your needs, it is likely they can create something that fits your material profile.
We saw multiple examples of this at their display, including ceramic materials or reinforced thermoplastics.
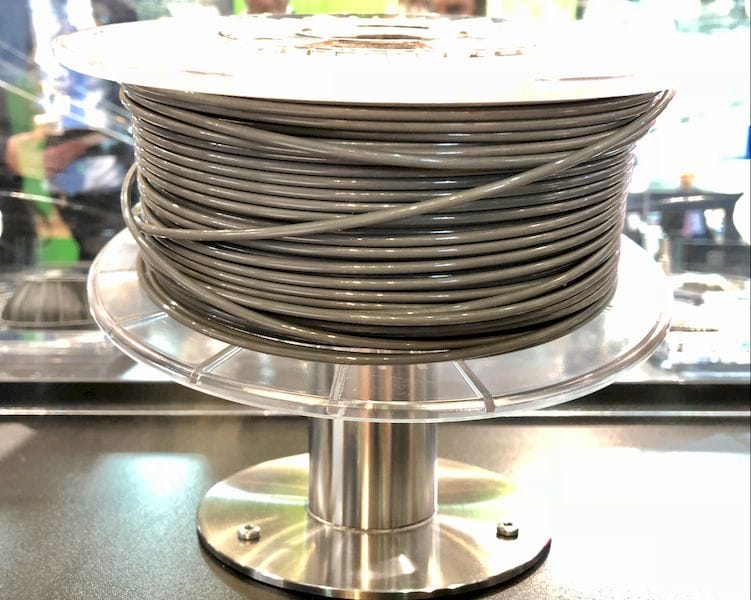
The metal-reinforced materials were most interesting. They’ve been able to produce a steel-reinforced polymer, shown here, that can be used by common desktop 3D printers to print “green” metal objects.
These green parts are then sintered in a precisely controlled furnace to bake out the polymer, leaving a nearly pure metal object. The ratio of steel to polymer in this particular material is about 80%, so you can expect to see a 20% decrease in volume of the green part during sintering, as seen here:
But what is most fascinating to me is that at this time in 3D printing history, there are multiple huge chemical companies directly working with 3D printer manufacturers to develop custom materials that are specifically designed for the technology.
Years ago the only materials one could use in most 3D printers were leftovers from other industries, like “ABS welding wire”. These worked, but not very well, as they were not designed for 3D printing by the chemical manufacturers.
From this point on, they will be.
Via BASF