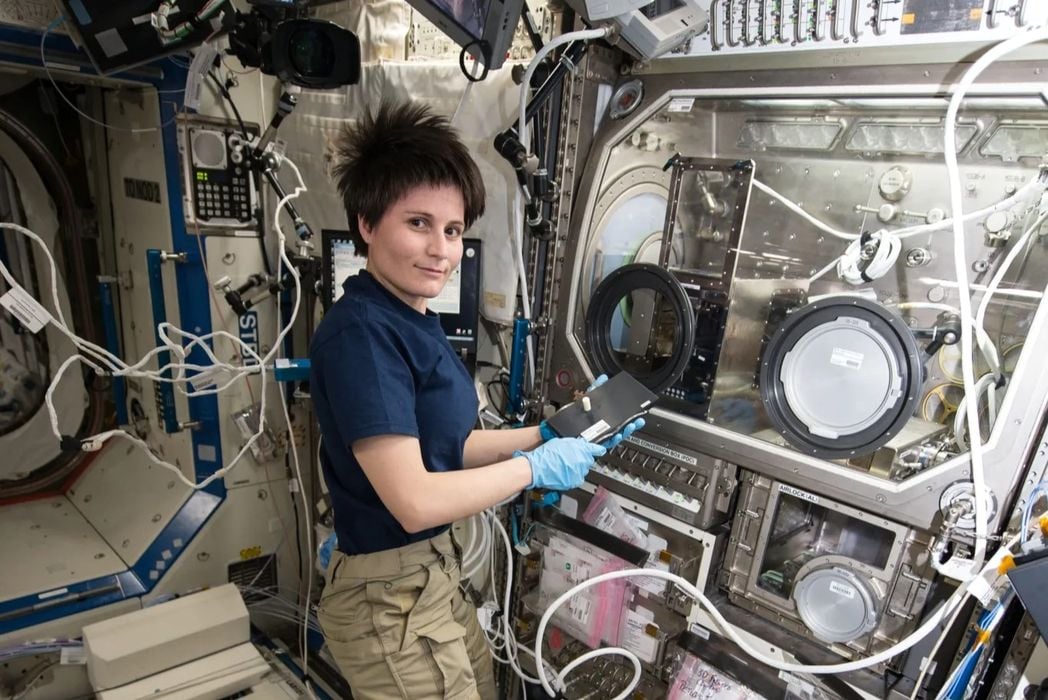
Understanding the challenges and benefits of 3D printing in space.
3D printing is no stranger to space-based applications. From complex rocket components to crushable structures for impact attenuation, there is a wealth of case studies one can draw from to highlight the advantages of sending components made with additive manufacturing (AM) into orbit and beyond the Moon.
But why stop there?
Given the advantages AM generally enjoys over traditional manufacturing methods – more complex geometries, better strength-to-weight ratios, less material consumption – why not send the 3D printers themselves into space and take it to the next level?
If we’re ever going to see space-based manufacturing become a reality, it will surely have to be additive. Before getting into why that is, it’s worth looking back on the history of 3D printing in space thus far.
A brief history of space-based 3D printing
It may come as a surprise that we’ve had 3D printers in space for over a decade now, with the first installation from Made in Space (now Redwire Space) aboard the International Space Station (ISS) dating all the way back to 2014. That was part of NASA’s In-Space Manufacturing (ISM) project, which included an examination of the effects of microgravity on the fused filament fabrication (FFF) process. Results show no significant differences between FFF parts produced in space and those printed on Earth.
Moreover, one of the parts printed on the ISS, a wrench, demonstrated that astronauts could use a 3D printer to create parts based on designs sent remotely from Earth. A second 3D printer, dubbed the Additive Manufacturing Facility (AMF), was installed to test components made from various materials, including engineered plastics. Beyond test parts, the AMF has also printed functional items, including an antenna part and an adaptor to hold a probe in an air outlet on the station’s oxygen generation system.
In 2019, astronauts aboard the ISS installed the ReFabricator, a 3D printer developed by Tethers Unlimited (now a subsidiary of Arka) designed to recycle waste plastic, including 3D printed items, into 3D printing filaments. The Made in Space Recycler was installed that same year to investigate which materials are most useful for recycling.
One of the most ambitious projects for 3D printing in space – Archinaut One – began in 2017 with Made in Space printing test parts inside a thermal vacuum chamber. The result was a Guinness World Record for the longest 3D printed non-assembled piece: a 37.7 m beam. This proof of concept led to a plan to build a 3D printer capable of operating in orbit that would be installed in a pod attached to the outside of the ISS. The pod would use a robotic arm to help fabricate, assemble and repair structures in space.
Made in Space won the NASA contract for Archinaut One in 2019 and the spacecraft passed its Critical Design Review in 2022. However, NASA announced in 2023 that it would conclude the project without proceeding to a flight demonstration and instead maintain the project data for unspecified future efforts.
Most recently, the European Space Agency (ESA) announced the successful deployment of the first metal 3D printer in space. Designed by Airbus Defence and Space SAS, the metal 3D printer produced its first test parts aboard the ISS just last year.
Challenges of 3D printing in space
Despite the overall positive results from investigations of space-based AM thus far, significant challenges remain. Few people understand this better than Gilles Bailet, an engineer and lecturer in space technology at the University of Glasgow. Bailet recently completed a series of tests on a 3D printer he designed specifically for in-space applications, riding the “vomit comet” to simulate a microgravity environment.
“You can’t just take an off-the-shelf 3D printer and add some ruggedized motors, a bit more glue in your screws and send that into space,” he explained. “You need to reinvent the way you do 3D printing.”
For Bailet, that reinvention includes swapping spools of filament for a granular material and a new type of extruder that can print in the vacuum of space as well as inside the ISS. There’s a tendency to think of 3D printing in space as happening exclusively in pressurized environments but, while that is challenging on its own, 3D printing in vacuum is considerably more difficult.
“There’s no air for convection to make the cooling rate of parts slow enough that they won’t delaminate or break,” Bailet explained. “This is a major constraint.” He also noted the significant temperature variations happening outside the ISS, where the thermometer can fluctuate between -150 C to over 100 C. Not an ideal environment for any manufacturing process, let alone one that depends so heavily on getting the temperature right.
In addition, as indicated above, there are challenges that come with 3D printing in microgravity, even inside a pressurized, temperature-controlled environment. Bailet noted that the pellets his printer uses as feedstock tend to clump together in microgravity, which can clog the extruder. For this reason, part of his testing on the vomit comet included varying print speeds. However, this led to an auspicious discovery that could actually increase the efficiency of his machine.
“We needed to find the optimum print speed, where you print as fast as you need using a minimal amount of energy. What we found was that you don’t need to run your feeding system continuously and instead you can run it so that you’re adding packets of pellets to the extruder, which is more energy efficient.”
Read the rest of this story at ENGINEERING.com