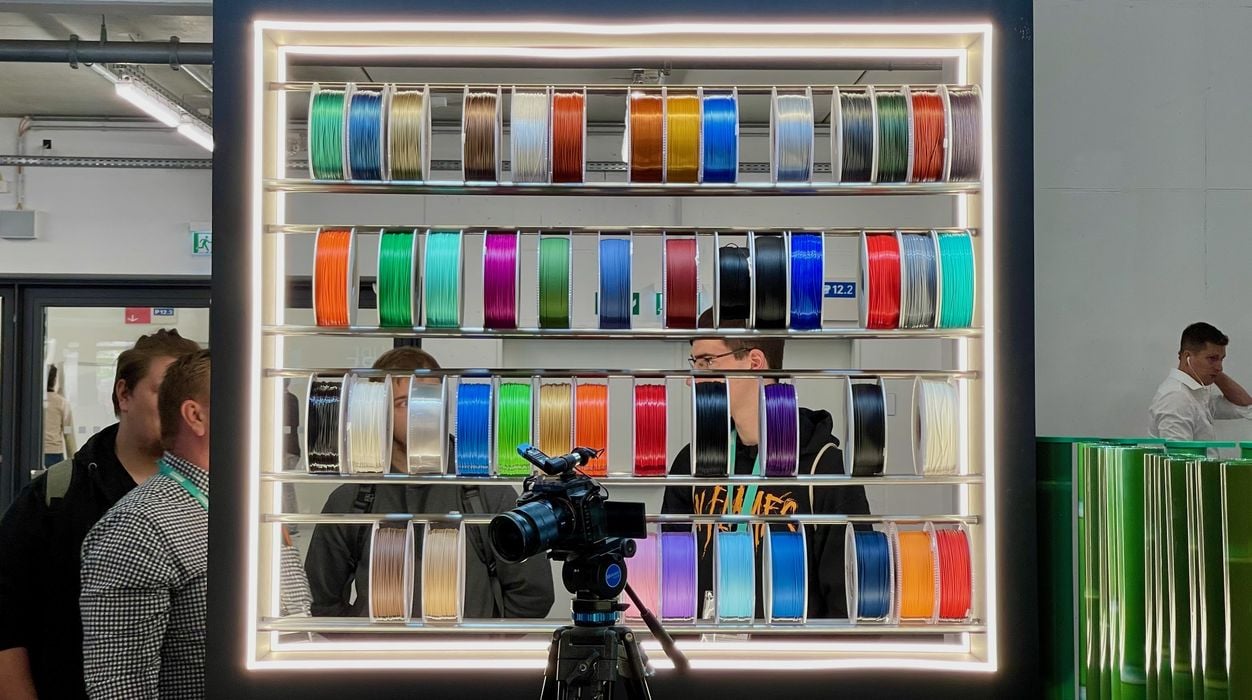
It may be that the era of proprietary materials might be ending.
Proprietary materials are a long-established method among 3D printer manufacturers. Technically, it means that a 3D printer is able to use only materials from the 3D printer manufacturer. This is accomplished through RFID chips to authorize material containers, or sometimes just the geometry of the containers.
There are some benefits to proprietary materials: since the equipment manufacturer knows the precise chemistry of the material, they can provide a finely tuned print profile that almost guarantees quality results. It also virtually eliminates work to tune the materials by the operator. That’s all good for the 3D printer operator.
There are also benefits to the equipment manufacturer: guaranteed revenue. For each printer sold, there will be a stream of materials sold for that device in years to come. Some manufacturers — but not all — raise their material prices to extract as much money as possible from their “monopoly” on materials for that device.
However, there’s a big negative to operators: the choice of materials is limited to only those products sold by the equipment manufacturer. Some manufacturers attempt to get around this limitation by providing a special mode that allows the equipment to operate with third-party materials, but often that is a degraded operator experience.
Another approach used by manufacturers is to establish a third-party material certification service, where they partner with materials providers to develop pre-made profiles for these products.
During AMS 2025 last week, I heard something interesting from a representative of a major auto manufacturer: the “razor blade business model for materials is dead”. They said the use of these systems “slows it all down”.
That was surprising, as I would have thought that major manufacturers would be highly interested in ensuring they have guaranteed part quality.
But no, it seems there has been another leap in additive manufacturing. These manufacturers are increasingly interested in using new and unique materials for their parts. Such materials can often provide a competitive advantage in their markets, and they (at least the larger and more AM-mature operations) are able to do their own print profile tuning to make those materials work.
The implication is that the proprietary materials provided might not keep up with what some large manufacturers desire, so they want to do their own.
I believe there will always be a space in the market for proprietary materials, as there will always be companies that value ease of use over cost and choice. However, with the statements made at the conference, it seems that there are an increasing number of large manufacturers willing to experiment with their own materials.