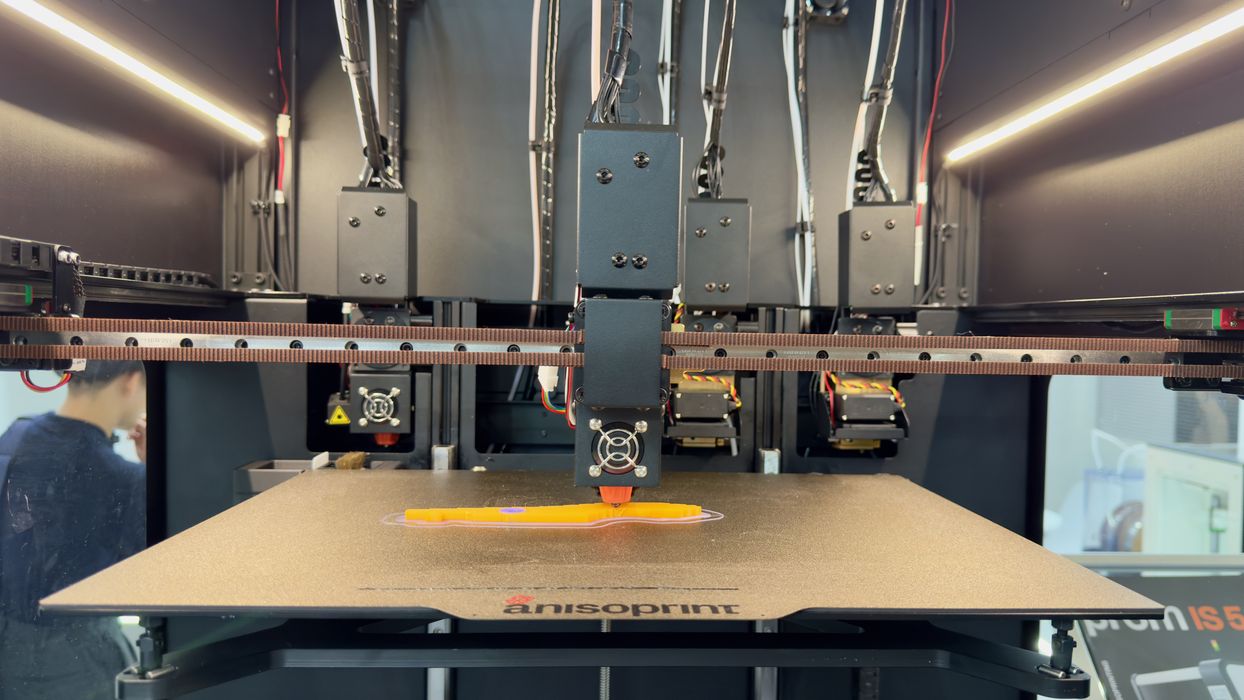
I had a look at Anisoprint’s Composer Nova, a continuous carbon fiber 3D printer.
Anisoprint is well-known as being one of the very few companies that produce continuous carbon fiber 3D printers. Instead of simply printing filament containing chopped-up carbon fiber bits, they literally extrude lengths of actual carbon fiber during printing. It works like this, as shown in their extruder diagram:
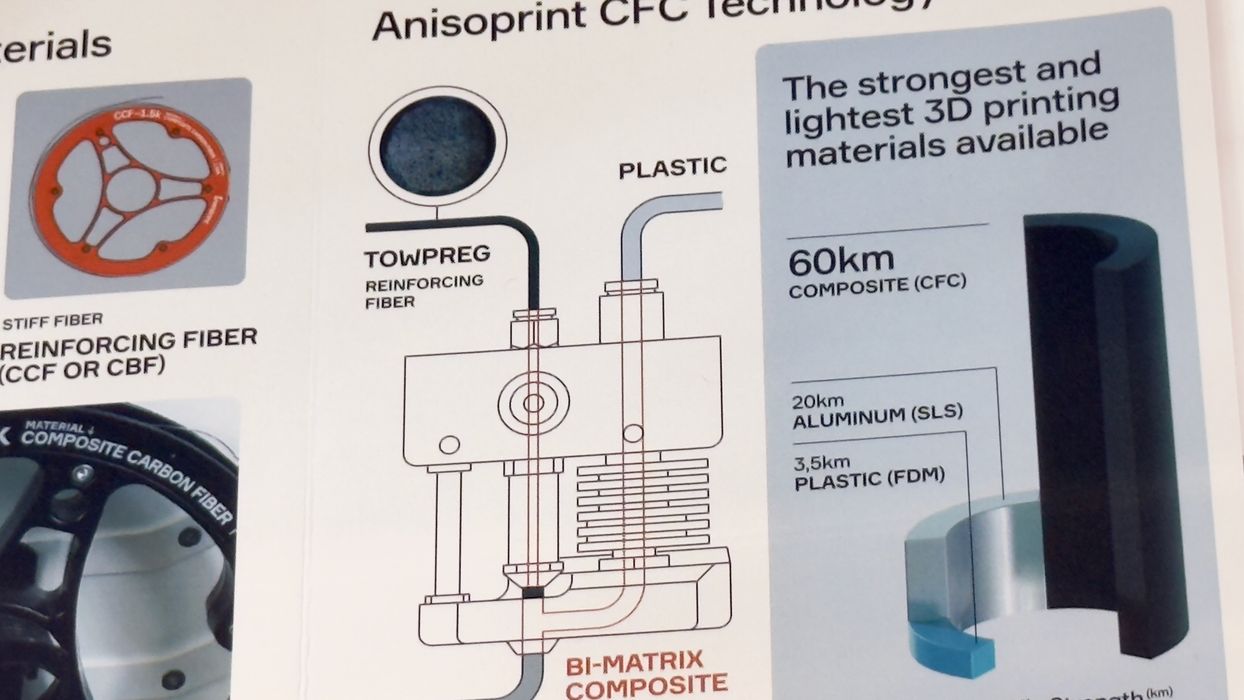
Strands of carbon fiber are laid down right with the polymer, layer by layer.
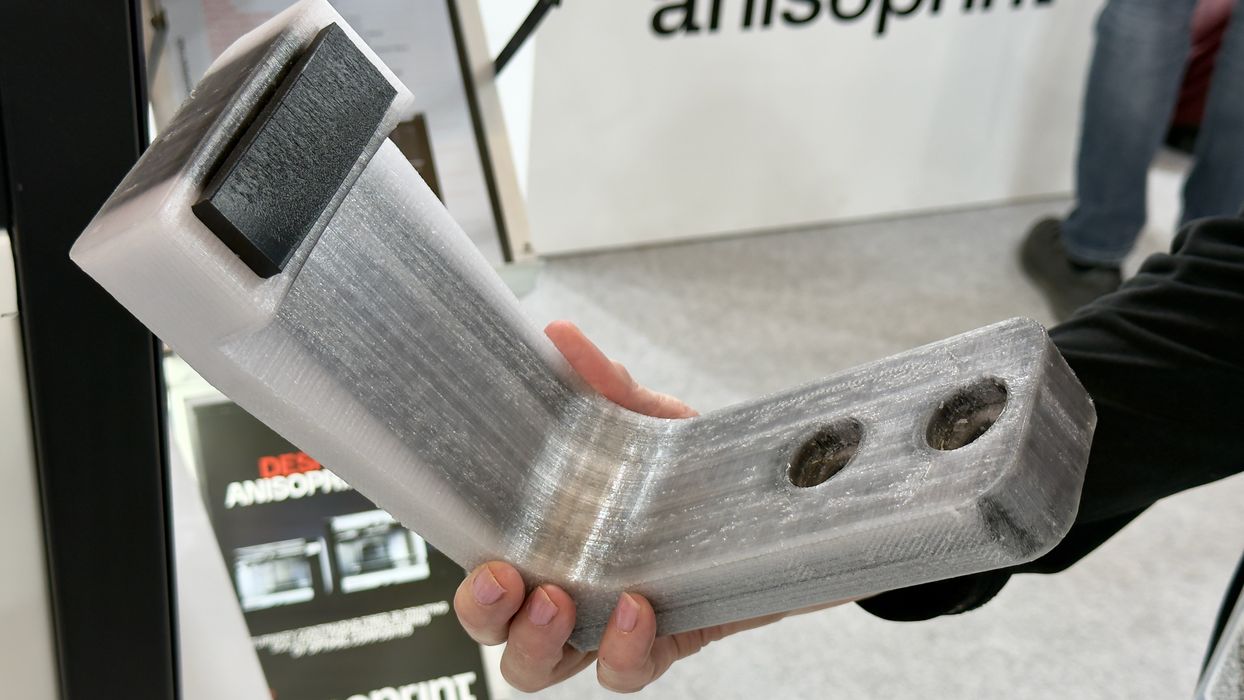
This produces extraordinarily strong parts, and they are quite lightweight, too. In low-temperature applications, they can often substitute for metal parts.
The Composer Nova is an interesting machine with some unusual features. At the top, you can see the interior of the machine, and it sports four different toolheads. The Composer Nova is a toolchanger, whereby the machine picks up the correct extruder on the fly during print jobs. This allows the machine to print in up to four colors or materials.
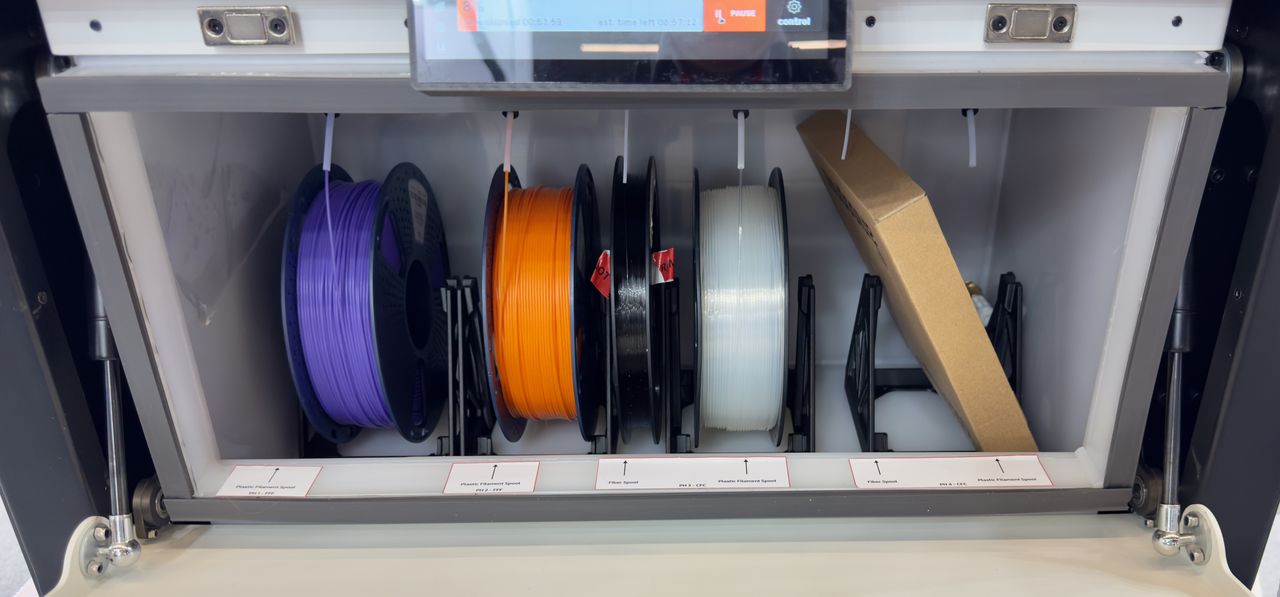
That’s not particularly unique, as several other machines have toolchanging capabilities. The difference here is that these toolheads can lay down carbon fiber strands.
Why do this? Why would you need to have more than one extruder putting out carbon fiber? The answer is that you can have two different diameters of carbon fiber — thick or thin.
Thicker is stronger and could be deployed in larger portions of a part, which the thinner carbon fiber might be used in more delicate areas or segments that have significant curves. The bottom line here is that you can get more carbon fiber into a part than you would with a single diameter option.
By having four toolheads, it would be possible to have a job that uses two colors and two fiber thicknesses. If color isn’t required, then one of the toolheads could be used for soluble support material. Another option might be to have two of each configuration for redundancy.
I asked how long a toolhead swap takes, and apparently only seconds. The switch is entirely mechanical, as the plunger expands when it hits the tool and grabs it. There’s a pin at the back that provides instant alignment.
There are advantages in using continuous carbon fiber, but perhaps even more when you have options to use multiple diameters of carbon fiber.
Via Anisoprint