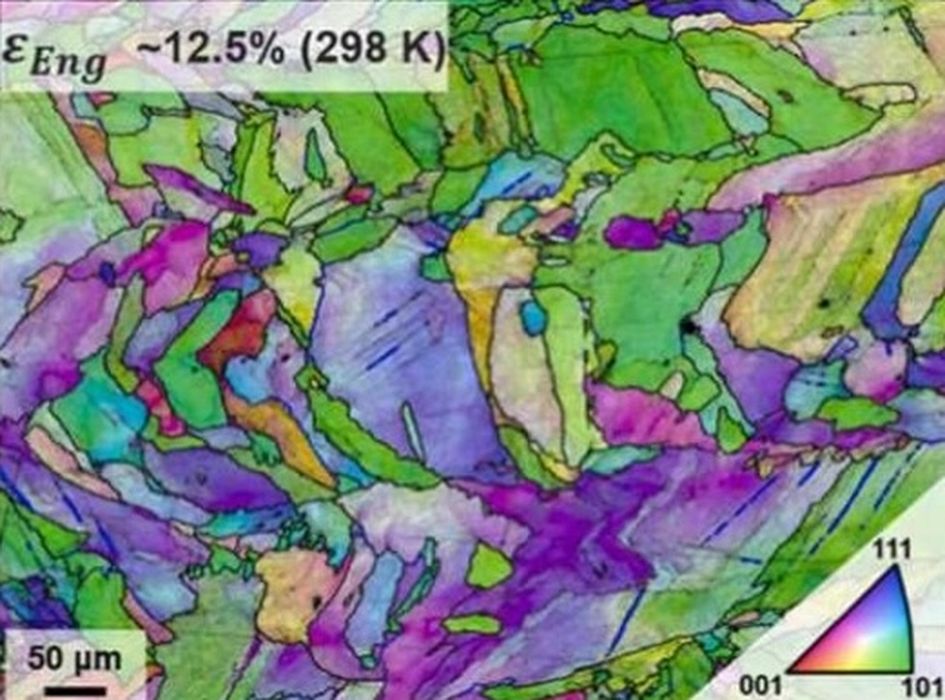
Researchers have developed a new 3D printable metal alloy that has exceptional cryogenic properties.
The research studied the cryogenic properties of a new alloy, carbon-doped CoCrFeMnNi high-entropy alloy (C-HEA), when 3D printed using the LBPF process. This is important because current metals used in LBPF are not necessarily good performers when exposed to extreme cold temperatures.
They found significantly increased yield strength and elongation compared to room temperature measurements. C-HEA demonstrates double the elongation at 77 K (liquid nitrogen temperature) compared to 298 K. The paper links these enhanced cryogenic properties to the presence of nano-sized carbides and the activation of deformation twinning at low temperatures, both of which contribute to delayed plastic instability and increased ductility and strength.
It seems that the added carbon contributes to the effect, leading to a higher density of geometrically necessary dislocations.
The researchers believe that this new carbon-doped C-HEA when printed using the LBPF process could have high potential in certain structural applications exposed to extreme cold temperatures.
There are several possible areas of application here.
One is aerospace, especially space exploration. These extreme environments can be quite hot, but also extremely cold. The enhanced cryogenic properties could also allow for advanced designs, such as weight-optimized, complex shapes achievable through LPBF, which is critical for fuel efficiency and structural integrity in aerospace applications.
Another is cryogenic storage and transport. LNG transport, for example, requires extreme cold and structural integrity at the same time. C-HEA could allow for improved safety and reliability in these systems.
Heavy machinery used in cold environments, such as mining, polar exploration, or even snow clearing operations, could benefit from lightweight parts that don’t break during cold exposure.
There’s also the possibility that C-HEA could lead to less intensive post-processing due to its resistance to cracking.
This is yet another example of how a seemingly straightforward materials development could lead to entirely new branches of 3D print applications. The more materials, the better.
Via Science Direct