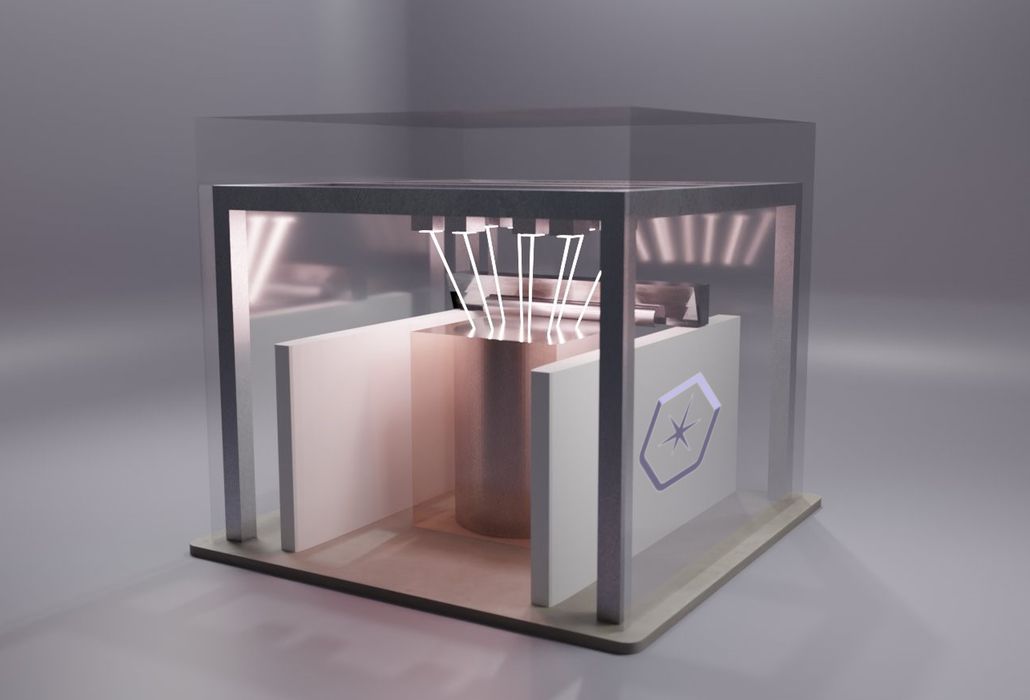
AddUp announced a major new project to develop a powerful metal 3D printing system: MASSIF.
“MASSIF” is an acronym for “Metal Additive System, Sustainable, Industrial, Eco-Friendly”, and that’s precisely what this project seems to be all about.
While MASSIF technology will be based on AddUp’s successful FormUp 350 tech, MASSIF is actually a consortium of the following partners:
- AddUp, the consortium leader, is designing the machine and building a prototype that integrates the technological building blocks of the process and production quality monitoring solutions.
- Cailabs develops laser beam shaping solutions to increase printing speed and thus machine productivity.
- ISP Systems develops a dynamic beam shaping solution to improve LASER beam focusing quality.
- Dassault Systèmes, which with the 3DEXPERIENCE® platform enables real data to be used to create virtual models that simulate products, processes and factory operations in the virtual twin experience, develops a data enhancement solution aimed at the efficient manufacture of certified critical parts
- Vistory, is developing a solution that guarantees the confidentiality and integrity of manufacturing data, protecting the creator’s industrial property and ensuring the traceability of operations.
- CETIM is contributing to the technological development of the prototype by carrying out tests on its FormUp multi-laser equipment, then integrating the final machine in its new Printing Bourges center, in order to validate the manufacturing parameters for different materials and produce the first demonstration parts for the various target markets.
The intent of the project is to build a new LPBF metal 3D printing system that offers both very large build volumes, as well as a number of efficiency features.
The maximum build volume envisioned is a whopping 1500 x 1500 x 2000 mm, with their first machine being “only” 750 x 750 x 1000 mm. This is 12X larger than current AddUp machines, which are typically sized for the industry.
AddUp said MASSIF systems would “increase productivity by 300%” and “reduce part cost by 50-70%”, but it’s not entirely clear how this is achieved. Some of the benefit would be simply through the larger build volume: more parts produced per job.
A very interesting item mentioned in AddUp’s press release is this:
“With less than 10% powder waste, this machine guarantees a more sustainable production process.”
Normally LBPF jobs generate a lot of unused powder, as only the model is solidified during printing. The rest of the powder is considered “used”. After sieving, this powder is eligible to be reused — but only in certain ratios with fresh powder. It seems that AddUp is able to reuse a majority of the powder, increasing efficiency and lowering material costs.
They say the machine “uses decarbonated energy”, and I don’t really understand this. Was the machine manufactured with decarbonated energy? Or does it required decarbonated energy? How is that any different from carbonized energy?
Why would AddUp enter this market? It seems to me that they have seen the success of several other large-format metal 3D printers, such as those from Nikon SLM Solutions, and may want a piece of the action. However, to do, you need products, and that’s where the MASSIF project comes in.
I’m interested to see more details on this ambitious project, which could result in a family of large-format metal 3D printers.
Via AddUp