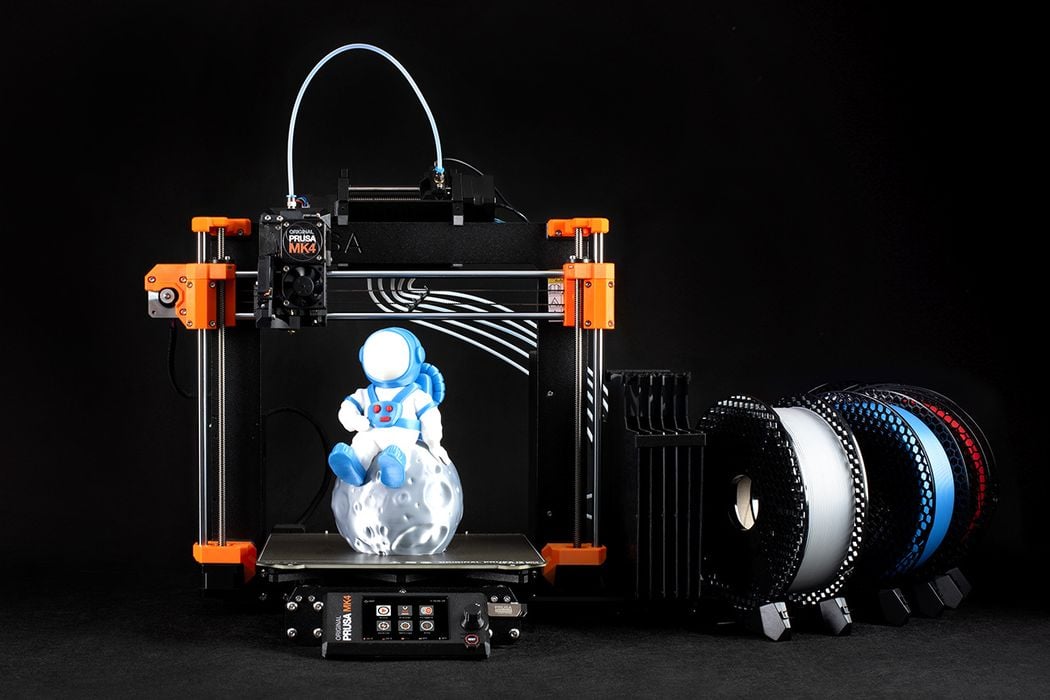
Prusa Research has published some interesting test results for their new MMU3 material switching accessory.
The “MMU” or Multi Material Unit, is an accessory that attaches to most of the company’s FFF desktop 3D printers. The current version is the MMU3, which is quite an improvement over the previous MMU2.
I tested the MMU2S some years ago, and found it was incredibly challenging to set up and use.
However, it seems that Prusa Research has been doing a considerable amount of listening to their community, and much of what they learned has been adopted into the design of the new MMU3. Here’s an example of the feedback they received:
“We realized that assembling the MMU required way too much patience to ensure everything was PERFECTLY aligned. This was never an issue with our 3D printers (as many people online say ‘the assembly kit just works’), so the situation with the MMU was somewhat unexpected – and the users voiced their frustration very strongly.”
The post describes the incredible amount of effort put in by Prusa Research’s MMU development team. They had to sift through staggering amounts of information from MMU2 operators, including not only direct feedback, but also threads, posts, images and other material publicly available.
All of this was then examined to determine a list of “things to fix”, which they then set about to do.
However, as they developed the MMU3 there was a considerable amount of testing required. This is far more challenging than would be on typical 3D printer hardware simply because MMU3 prints can take far more hours to complete. This implied a long series of lengthy tests that took many months.
That work paid off, however, as their seemingly good design suddenly stopped working. Their diagnosis revealed that the repeated inserts and retractions of filaments tends to wear down the extruder plate far faster than would be the case with a single extruder.
They came to realize that the extruder plate is actually a consumable that will require replacement periodically. To counteract this they’ve included a replacement plate that’s produced with HP’s MJF system. The material used is far more durable than the standard PETG part.
It’s also possible for operators to print their own replacement plate in PETG, but Prusa Research said it won’t last nearly as long.
The company also provided some statistics showing that the MMU3 is somewhat faster than competition multimaterial systems.
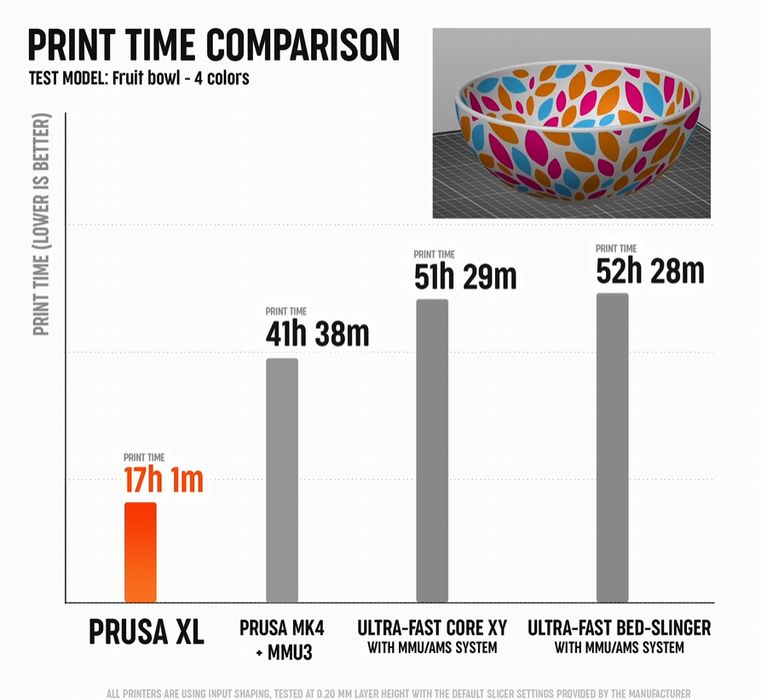
In the chart above we can see a MK4 equipped with a new MMU3 printing a fruit bowl 3D model in four colors. Note the times on these prints are very long – almost two days for the MK4, and over two days for the competition. Most likely the comparison machines are the Bambu Lab X1C and the Bambu Lab A1, although Prusa Research doesn’t say.
The Prusa XL also appears on the chart with a far lower print time for the same fruit bowl. This is because the XL has multiple toolheads, each able to handle a different color. That configuration means that there is no time required to swap filaments in a single extruder, so much time is saved.
Prusa Research also indicated that the MMU3 design wastes less material than competing systems, saying:
“Another thing the MMU3 unit enables is multi-material printing with manageable waste. Instead of cutting and flushing excessive amounts of filament, the MMU3 uses a compact, semi-hollow waste tower. The size of the wipe tower can be further reduced by using wipe-to-object or wipe-to-infill options which purge the leftover material in the nozzle – either way, you don’t have to worry about pieces of plastic piling next to your printer.”
The MMU3 is no doubt a great advance over the MMU2S, but that was absolutely required due to increasing competition, where there are now several companies offering multimaterial switching units with their desktop systems.
It’s a battle to provide the best balance of reliability, speed and cost, and the MMU3 looks like a good option — if you use Prusa Research equipment.
Via Prusa Research