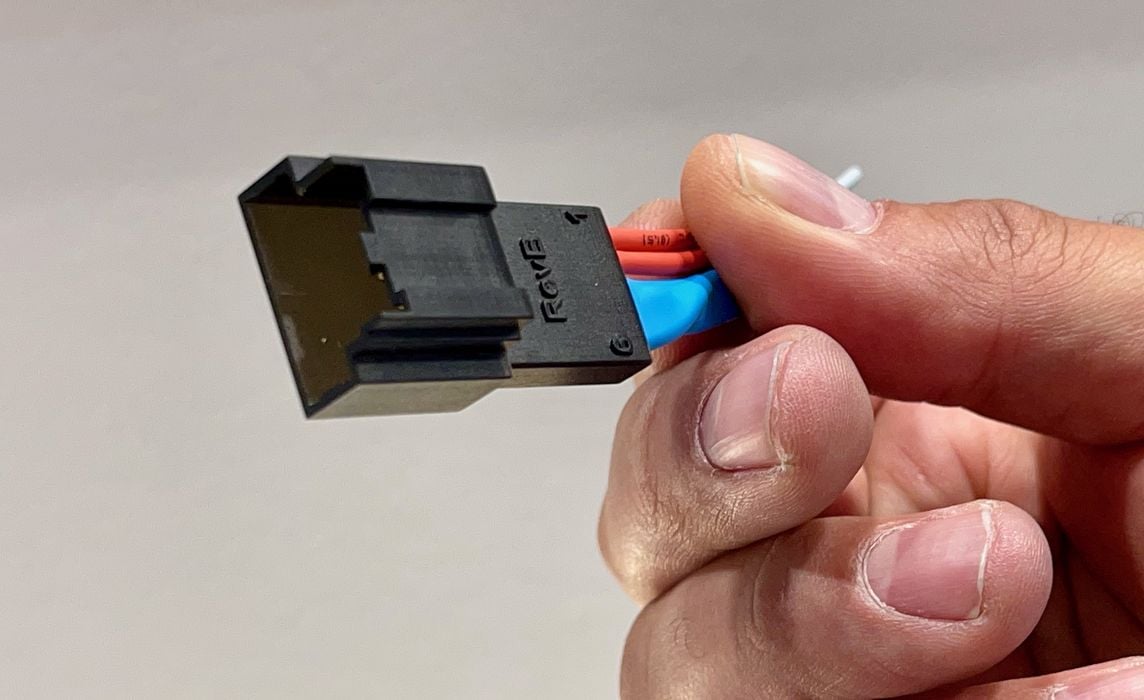
I had a chat with Axtra3D and learned the company has taken a step forward.
Axtra3D is a relatively new name on the 3D print scene, having emerged only two years ago. They landed in the market with a very unusual resin 3D printing process that attempts to combine the benefits of SLA and DLP resin 3D printing, while overcoming the disadvantages of both. They call it “Hybrid Photosynthesis”, or “HPS”.
It’s quite a unique system, where the perimeters of the models are printed with a laser to ensure smooth and precise surfaces, while the unseen interior is quickly printed with the DLP light engine. This permits very fast 3D printing, but retains the external accuracy of SLA.
For the first period they promoted their unique technology, which makes sense. Many 3D print companies take time to zero in on their target application market, and that seems to be what Axtra3D proceeded through in their first years.
Now, however, they seem very focused on applications. As companies used their technology they increasingly discover applications that are best suited for the unique 3D printing process.
I saw some of these applications, most of which are in the industrial or healthcare market.
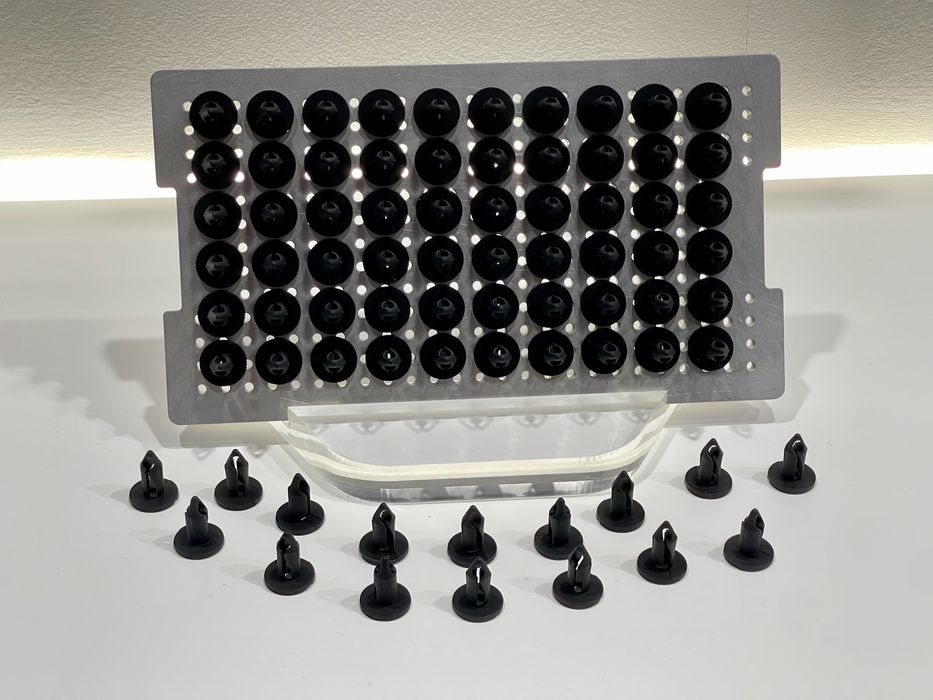
One was this automotive fastener. It was produced using Henkel’s Loctite 3843 resin, and cost only US$0.20 per part. This was achieved by batching together a series within a single print job. The job took only 93 minutes (showing the speed of the Axtra3D’s HPS), and that means less than two minutes per part. Axtra3D said their system can produce 720 of these per day, or over 21,000 per month.
At top you can see an electrical connector produced by one of Axtra3D’s customers. This item can be produced 72 per job, or about six minutes each at a cost of US$0.75. The production rate for this part could be up to 6480 per month.
Another example shown by Axtra3D was industrial molding. The idea is to 3D print a mold using HPS, and then use it with a traditional injection molding process.
The example shown printed a mold in BASF Ultracur3D RG 3280, which was then used for polypropylene injection. Two-sided molds were producible in only 99 seconds each throughput (for a two hour job), which could then each be used for repeated injections.
3D printed molds are never as durable as traditional metal molds, but Axtra3D reported that the molds they printed were able to withstand up to 300 shots of polypropylene at temperatures up to 300C. By the time the injections wear out the mold, new molds could have already been printed.
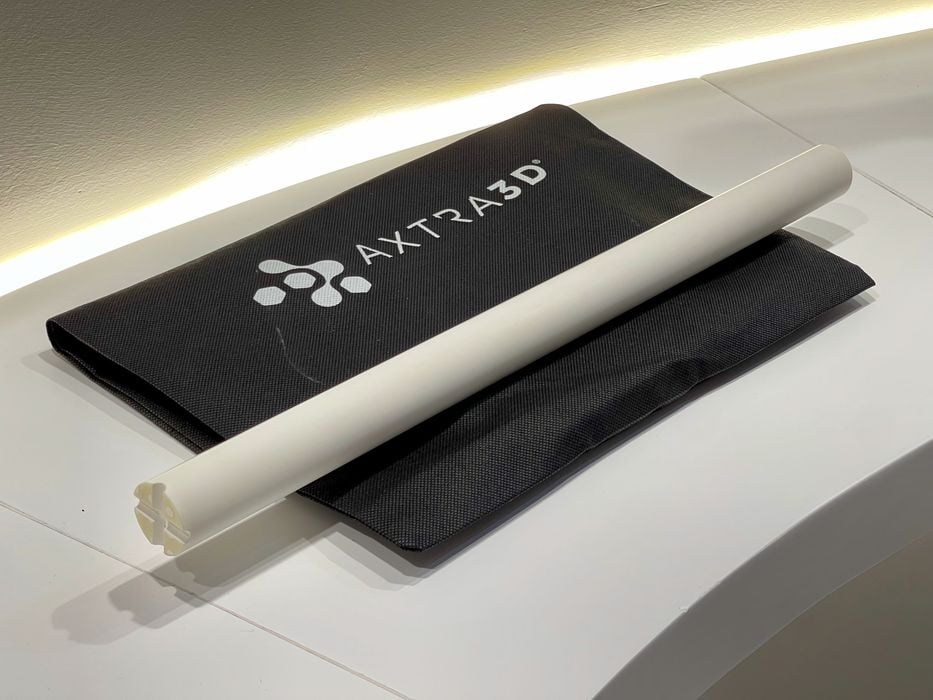
Finally, we have this innocuous 500mm ceramic rod, also made using HPS. While it doesn’t look so unusual, it turns out it has a 0.4mm hole all the way through the length of the rod. That’s a very impressive 3D print, as there aren’t many 3D print processes that could produce with that precision.
These examples show how HPS can be used for true end-use part production. While it might be possible to make the parts with lower per-unit costs with other manufacturing processes, the benefit here is that there is no tooling challenge: just print them.
This could make HPS systems ideal for low volume production or emergency backup when existing suppliers are unable to deliver on time.
To aid in their quest for new HPS applications, Axtra3D has smartly made arrangements with a number of resin providers. This creates a broader spectrum of materials that can be used by HPS, and opens the door to even more applications.
I believe Axtra3D is on the correct strategy here: focusing on applications is the best way to align with customers, and it should bring them further success in the future.
Via Axtra3D