
Charles R. Goulding and Preeti Sulibhavi discuss how 3D printing can help accelerate and accommodate ADU and DADU construction.
The quest for affordable housing has developed its own lexicon.
Accessory dwelling units (ADUs) and detached accessory dwelling units (DADUs) have become increasingly popular options for adding affordable housing in high-cost markets. Often called granny flats, in-law suites or backyard cottages, ADUs and DADUs provide independent living spaces on the same lot as an existing single-family home.
ADUs are typically smaller, independent units with their own kitchen, bathroom and living area. Attached ADUs are connected to the main house, while DADUs are stand-alone structures. Both can expand housing options and make efficient use of residential lots without major redevelopment.
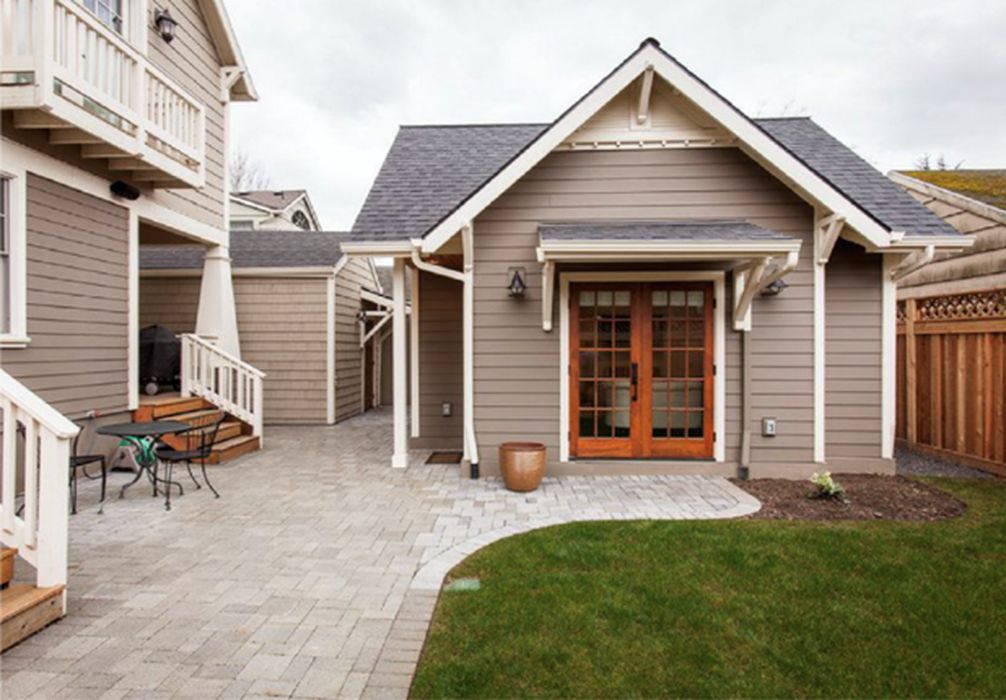
Opportunities for 3D Printing
Constructing affordable ADUs and DADUs poses challenges due to their small size. The reduced footprint limits space for contractors and can make it difficult to utilize traditional building methods. This is where 3D printing can provide transformative solutions.
For ADUs and DADUs, 3D printing can construct walls, floors, roofs and components of HVAC systems as prefabricated modules. The modules can be produced offsite, rapidly assembled on location, and finished to create high-quality affordable housing.
Complete Home Construction
Entire small homes can potentially be 3D printed to streamline ADU and DADU production. In 2022, Palari Group and Mighty Buildings opened a 3D printed backyard ADU in California using a light-weight polymer composite. The project demonstrated the viability of 3D printing ADU envelopes.
Other companies like ICON are 3D printing homes and buildings from concrete. Their Vulcan printer can construct core and shell housing in a matter of days. Such approaches may enable faster, lower-cost delivery of ADUs and DADUs with less disruption to neighborhoods.
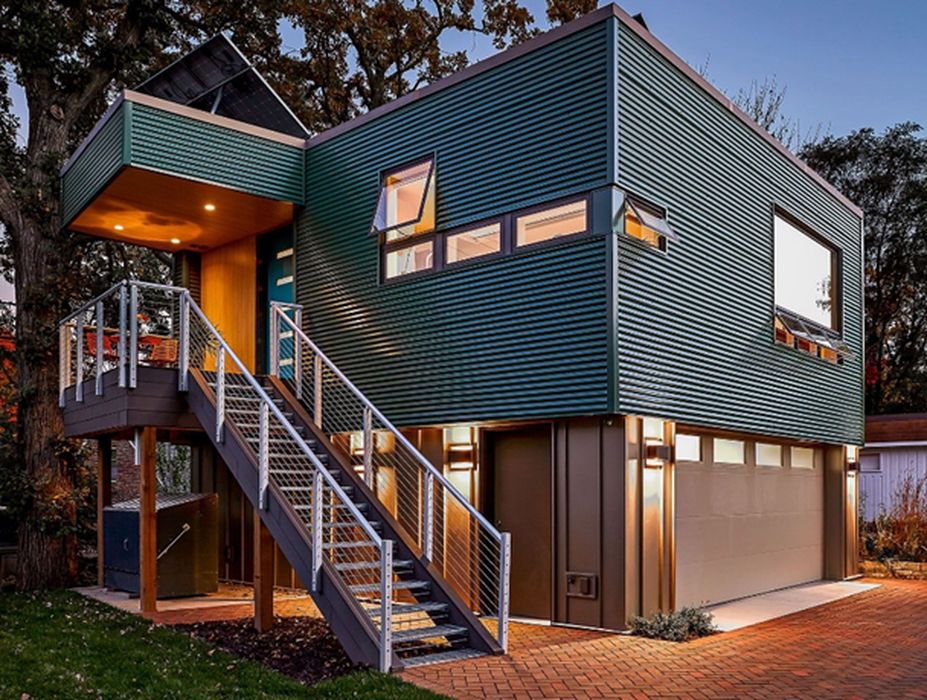
Interior Components
While whole-home 3D printing is still emerging, the technology is gaining traction for printing interiors. This allows customized ADU/DADU layouts paired with 3D printed bathrooms, kitchens, stairs, furniture and more.
For lighting and electrical, 3D printing enables customized light fixtures, lamp shades, switches, outlets and wiring covers. Companies like Electrical Alfresco offer 3D printed wall sconces and ceiling lights.
3D printing also allows on-demand faucets, shower heads, bathroom accessories and modular kitchen components. Sink manufacturer EOS recently partnered with additive manufacturer MakerBot to offer 3D printable faucets. Such products speed up installation and provide modern designs.
Beyond functional elements, 3D printing empowers unique furniture and decor. Design marketplace Houzz features stair balusters, table bases, flooring, art and other 3D printed interior products for stylish and space-saving ADU/DADU furnishings.
Scaled Production for Local Markets
For 3D printing to truly impact affordable housing, solutions must scale beyond one-off demonstration projects. ADU/DADU providers need reliable local sources for printed modules and components.
Some 3D construction companies like Mighty Buildings and ICON are developing micro-factories. These small facilities can serve metro areas with just-in-time production of standardized ADU/DADU modules, bathrooms, kitchens and interior kits customized for local building codes.
Such localized, mass-customized factories could make 3D printed ADUs/DADUs cost-competitive with conventional construction. If achieved, 3D printing would fundamentally disrupt the affordable housing landscape.
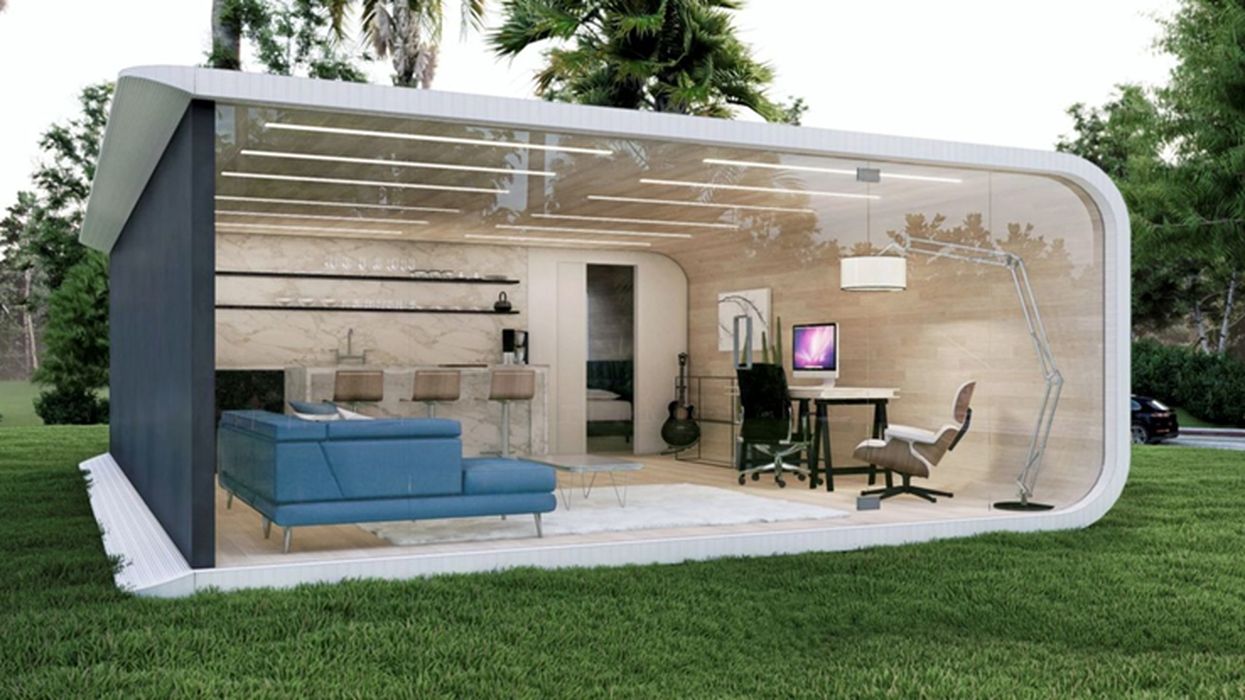
ADU/DADU Growth Creates Opportunity
The ADU/DADU market appears primed for 3D printing disruption. According to the Terner Center at UC Berkeley, the United States permitted approximately 87,500 ADUs between 2010-2019. Just five states—California, Florida, Oregon, Texas and Washington—accounted for over 70% of permitted units.
Recent years showed dramatic growth. U.S. ADU permits increased from less than 7,000 in 2016 to over 30,000 by 2019. States like California have pioneered ADU-friendly policies like standard permit templates, fee waivers and pre-approved designs. Oregon legalized “middle” housing options like duplexes, triplexes, and quads to encourage infill alongside ADUs.
Challenges to ADU/DADUs
This trend does not come without challenges. While interest is growing, ADUs and DADUs also face hurdles to mainstream adoption. One challenge is financial viability – constructing a small, detached unit can cost nearly as much per square foot as a full-sized home. This strains the rent versus construction budget economics, especially given tight lending conditions for ADUs.
Additionally, neighbors sometimes oppose ADUs over concerns like parking, noise, privacy and neighborhood character. In Los Angeles, one study found nearly 60% of ADU projects faced neighbor objections. While cities are working to streamline permitting, Not in My Backyard (NIMBY) attitudes persist as barriers, where homeowners are faced with sharing their personal space with complete strangers.
While we have covered men’s sheds and she sheds, this involves more than just “hobbying” in one’s backyard and will introduce housing responsibilities and legal terms to the situation as well. And, there is the issue of defining what a “city” or metro-region is defined as in terms of ADU zoning regulations.
3D printing could help make ADUs more cost-effective by lowering material and labor costs for construction. However, financing and neighborhood acceptance issues will likely remain even with advanced building technologies. Overall, cities will need to balance existing homeowner rights with the need for more diverse, affordable housing options.
The Research & Development Tax Credit
The now permanent Research & Development Tax Credit (R&D) Tax Credit is available for companies developing new or improved products, processes and/ or software.
3D printing can help boost a company’s R&D Tax Credits. Wages for technical employees creating, testing and revising 3D printed prototypes can be included as a percentage of eligible time spent for the R&D Tax Credit. Similarly, when used as a method of improving a process, time spent integrating 3D printing hardware and software counts as an eligible activity. Lastly, when used for modeling and preproduction, the costs of filaments consumed during the development process may also be recovered.
Whether it is used for creating and testing prototypes or for final production, 3D printing is a great indicator that R&D Credit eligible activities are taking place. Companies implementing this technology at any point should consider taking advantage of R&D Tax Credits
Conclusion
These regulatory shifts are projected to continue. The U.S. Department of Housing and Urban Development aims to encourage ADU construction by developing model codes and providing technical assistance to local governments. If adoption grows, 3D printing could help cities accommodate accelerating demand.
Forward-thinking policies combined with advances in 3D printing technology may bring ADUs and DADUs to the mainstream while balancing homeowner rights as well. For cost-effective and sustainable affordable housing, the future could be printed.