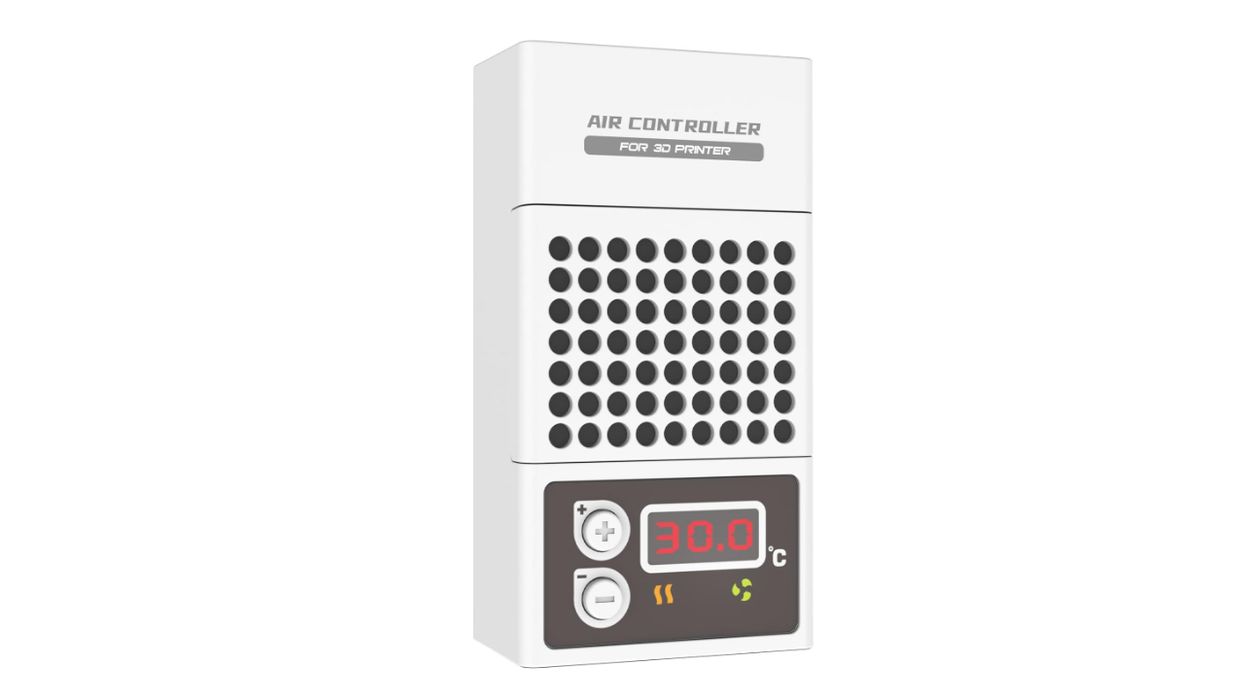
In my quest to find the most unusual 3D printing accessories, I found an interesting heating unit.
I found the “Mini Heater” on Amazon while looking for other 3D printing parts, and I realized it could be quite a useful addition for resin 3D printer operators.
But why would you need heat when resin 3D printing? Let me explain.
In MSLA or DLP 3D printing processes, the print plate is dipped into the resin vat, right to the bottom. There the light source shines through the bottom of the tank to selectively solidify some resin and attach it to the plate. This process repeats, adding more solid structure to the print as the job proceeds.
However, there’s something interesting happening between those layers. The print plate must be raised up, which not only makes space for the next layer, but also allows resin to flow in and replace the resin that was just solidified.
In order to do this the print is usually raised quite a bit higher than needed just for the next layer. That’s because the resin is somewhat viscous, and requires space and time to flow into the cavity formed when the plate rises.
Because of this there are parameters in resin 3D print jobs to specify the amount of time between layers. That’s not just waiting for waiting’s sake; instead it is the time required for resin to flow.
If the resin doesn’t flow sufficiently during that time, then the next layer might have missing or weak structure: there wasn’t resin to solidify. That could cause print failures or quality issues.
The answer is to lengthen the inter-layer time, which might mitigate the problem, but it can also slow down a print job immensely. Suppose you add three seconds to the layer time. On a 1000 layer job, that’s another 50 minutes of job time!
There is another answer: heating the resin. Like most fluids, resin tends to get more viscous when it is cold. When heated it loosens up and is far easier to flow.
For this reason many advanced commercial resin 3D printers include specific heating elements. They may even wait until specific temperatures are achieved before starting printing operations.
None of that appears on inexpensive desktop resin 3D printers, and that’s one of the many reasons resin 3D prints can fail: the resin was too cold and the operator didn’t compensate with extra layer delays.
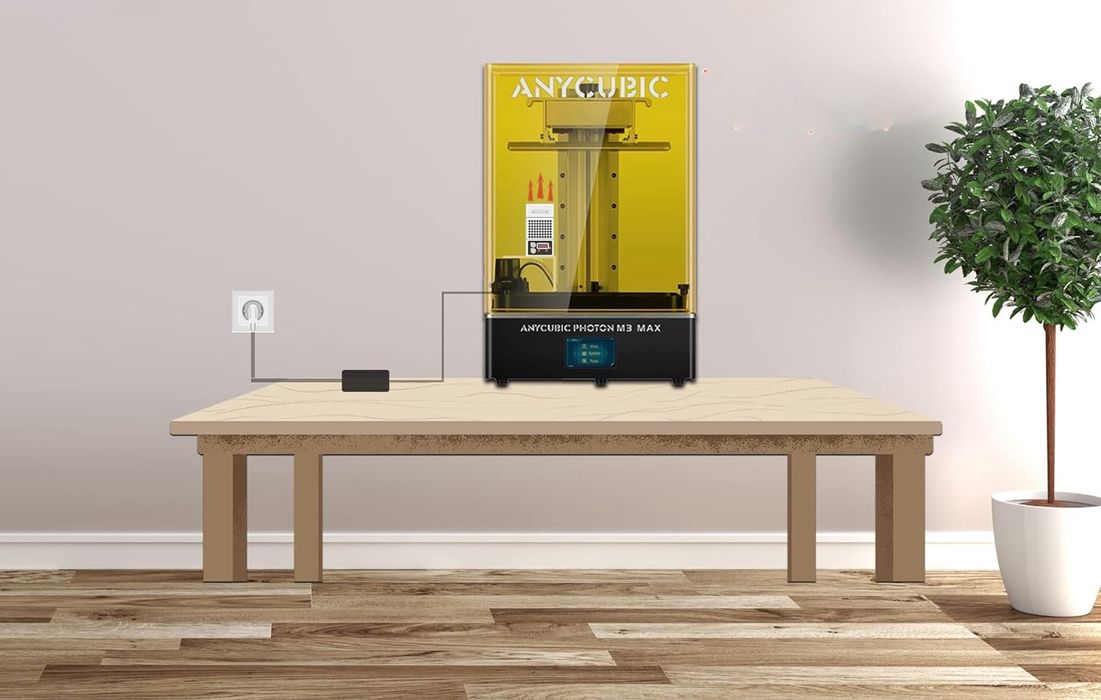
The Mini Heater might be able to help in these situations. It’s a small component that can be placed inside the build chamber of a desktop resin 3D printer.
The device includes a heater, circulating fan and filtration system. When the heater reaches the target temperature, the fan kicks in and blows hot air throughout the build chamber.
While doing so it is also filtering the air, which is also a good thing: resin emissions can be toxic and ventilation is always required. The filtration system reduces the need for that slightly and makes the situation a bit safer.
The device sucks air in from the middle, and blows the hot air upwards, away from the printing action. It appears that hot air would gradually collect at the top of the build chamber and work its way down as more hot air is produced. This suggests it might be a good idea to run this heater for a while before starting a job. While the air is heated quickly, that heat has to soak into the resin as well.
Heating resin is more useful when the resins are more viscous. There are certain resins that tend to be extra-viscous, typically ceramic resins that include a great deal of additives.
The Mini Heater is powered by an external power supply, so you’ll have to modify the lid to your resin 3D printer to accommodate a 5mm cable. The power rating is 55W, which is less than a hair dryer, but certainly sufficient to fairly quickly heating up a small build chamber.
If you’re having quality issues with your resin 3D printer, it might be due to a thermal issue that could be corrected with this accessory.
We’re an Amazon Associate and earn a small commission from qualifying purchases. Help support our 3D print news service by checking out this item!
Via Amazon