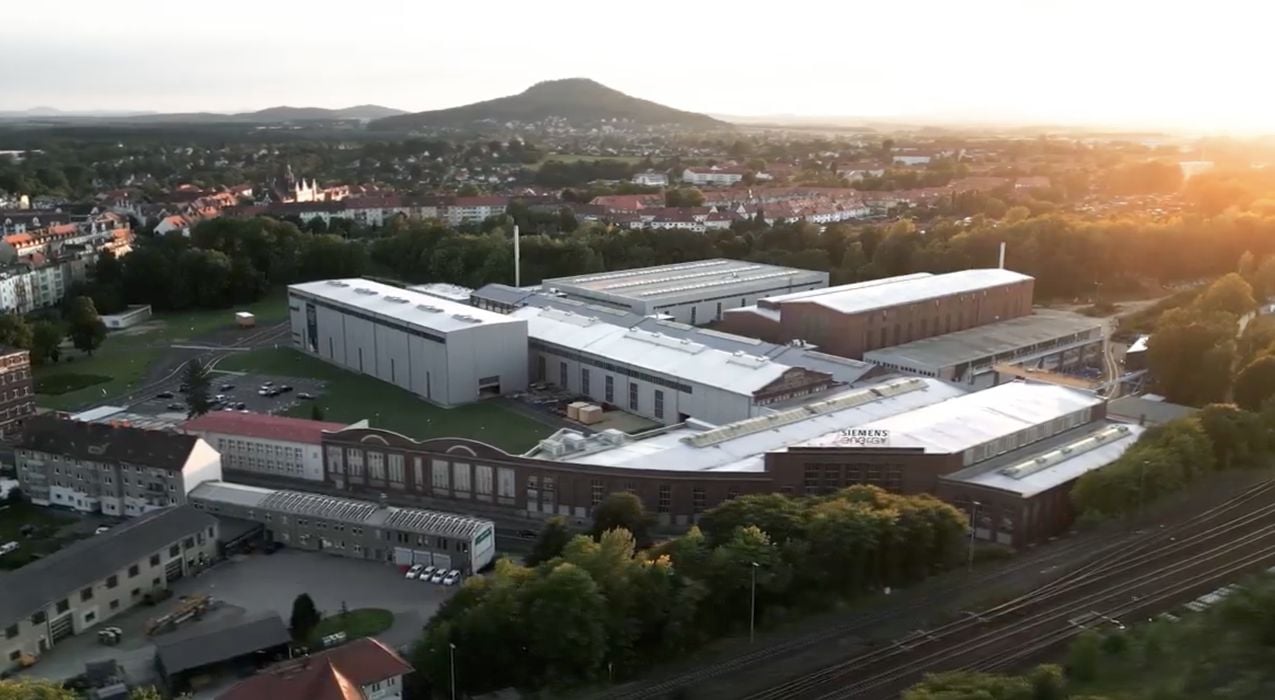
A small milestone in additive manufacturing was achieved by Siemens Energy this week.
The milestone was that Siemens Energy produced their 1000th 3D printed production guide vane for steam turbines.
The vanes have been produced by Siemens Energy using GERFERTEC technology. This German company produces wire arc additive manufacturing equipment (WAAM), which can very rapidly produce large metal objects in a wide variety of materials.
GERFERTEC’s metal 3D printers use a robotic motion system with either three or five axes of motion, depending on the system selected. Their largest device can produce metal objects up to a whopping 3000kg.
Siemens Energy turned to GERFERTEC several years ago when a crisis in supply chains threatened to sabotage their product delivery. This scenario happened to many companies in recent years, but here Siemens Energy decided to resolve the issue by bringing the manufacturing of the part in-house.
The part in question is a guide vane. In a steam turbine scenario, the guide vane is used to direct the flow of steam towards the rotors. By optimizing the geometry of the guide vane the maximum energy can be extracted from the steam as it turns the rotors.
It turns out there’s quite a science behind guide vanes, and that’s one of the features of Siemens Energy’s products. It’s certainly a very important component.
Siemens Energy was able to 3D print the required guide vanes in their own facility and short circuit the supply chain issues entirely. According to GERFERTEC they were the first company in the world to adopt WAAM technology for serial production.
Siemens Energy was satisfied with the results and continued using the WAAM approach to this day. Now they celebrate the production of their 1000th unit.
There are absolutely 3D printed applications where more than 1000 parts were produced. There are even some single job runs that can do so on particular equipment. However, the guide vanes in this story are quite large and that’s what makes this a unique milestone.
There are more than likely multiple applications of a similar nature buried within other large manufacturers that have not yet taken advantage of additive manufacturing techniques.
What are you waiting for?
Via LinkedIn (Hat tip to Benjamin)