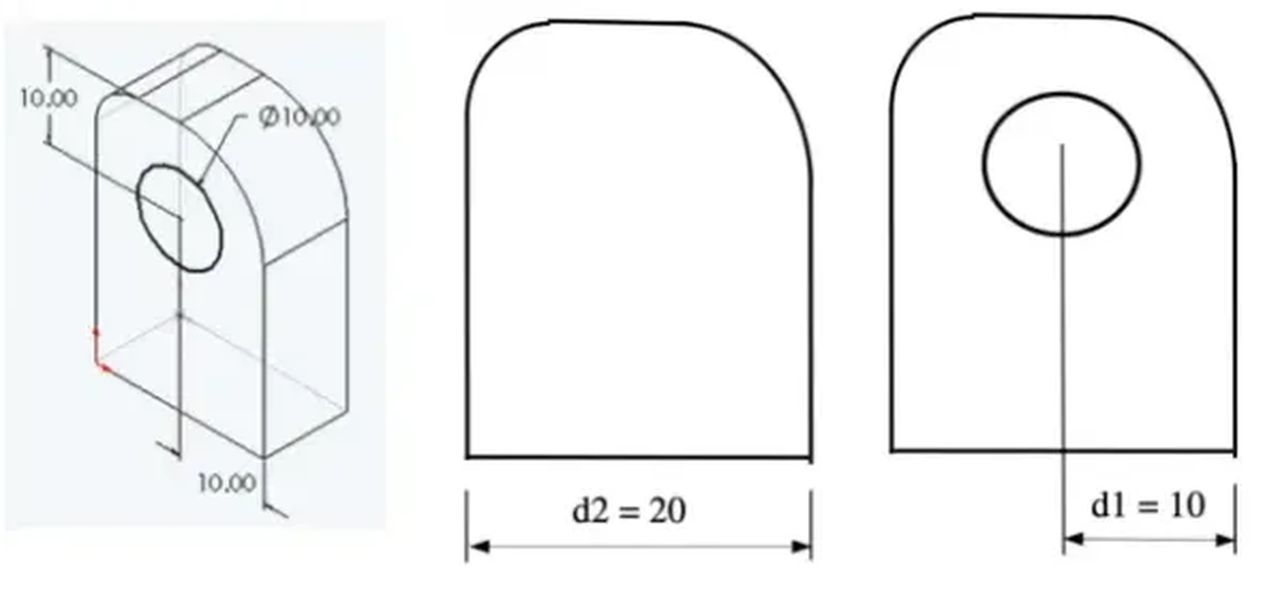
PTC made parametric modeling famous.
In computer-aided design (CAD), parametric modeling is a technique for creating and modifying drawings (2D) and models (3D) by specifying parameters. For example, with parametric modeling, you define a box with the parameters L for length, W for Width and H for height instead of using numbers. Parameters can be filled in with numbers or formulae. For example, for L (length), you could use L=2*W, making the length of the box twice the width. Parameters can define distance, angle, quantities, and more.
When you change a parameter, the entire model updates automatically to reflect the change.
Benefits of Parametric Modeling
- Capturing design intent: Using variables (instead of scalar values) in relationships or formulae can capture design intent, rules or standards. For example, a bend radius can be made twice the thickness of the sheet metal (R=2*T).
- Flexibility: It’s easy to make changes to a model after it has been created. You simply adjust the parameters and the model will update automatically. For example, if a client wants to see how it will look if all the ceilings in a high-rise are changed from 8 feet to 8.5 feet, the architect needn’t tear their hair out—if the height of the ceiling was defined with a single parameter, say H. The architect only has to make H equal to 8.5 feet in one place and all the floors in the building will immediately be at the new height. The architect would not have to manually change each ceiling height manually.
Disadvantages of Parametric Modeling
- Complexity: Parametric models can be more complex to create than traditional models, especially for beginners. Defining a model parametrically means more up-front work in the design. Users may protest having to use parametric design, especially on simple models. A complicated model will require significantly more effort than just plugging in numbers, especially if formulae are used.
- Constraint hell: Parameters first come into play when creating the sketch that will serve as the basis of a solid model, for example, the profile of an extrusion. A parametric modeler that requires a fully constrained model before the solid is created may put the user in “constraint hell,” a condition in which the user cannot find how the sketch is under- or overconstrained, and the modeling can go no further.
Read the rest of this story at ENGINEERING.com