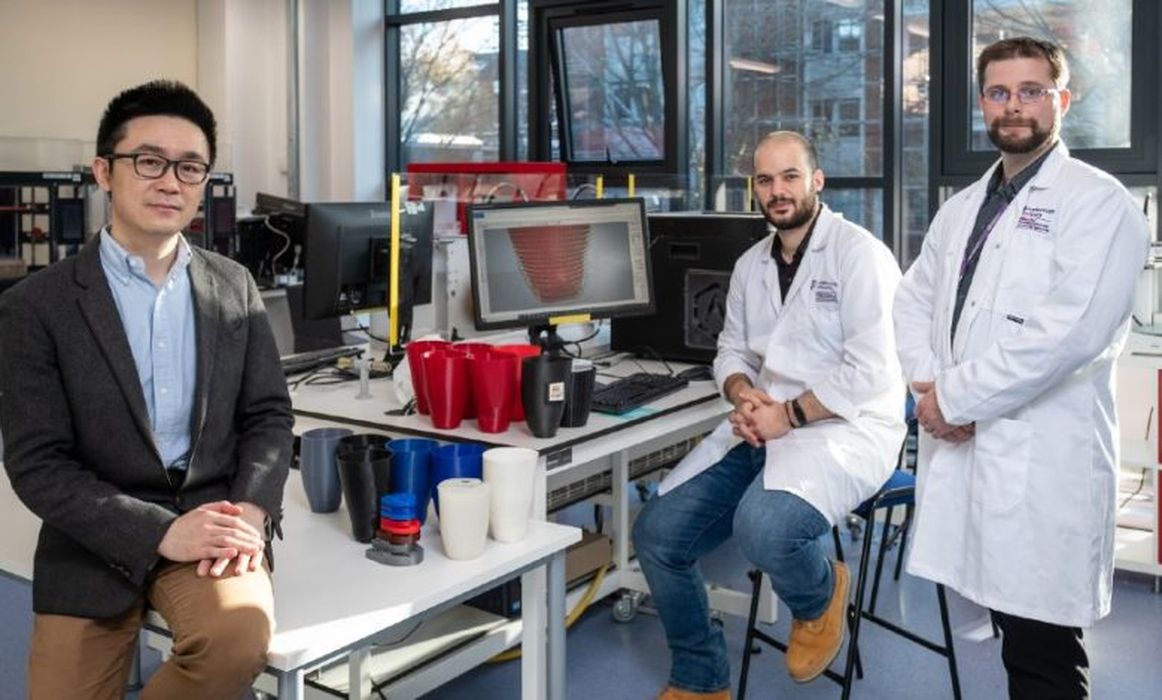
According to research at Loughborough University, led by Dr. Simin Li, the novel digital workflow significantly increases accessibility and production speed.
According to Loughborough University, lower limb prosthetic sockets could soon be printed in remote locations and even in users’ homes, thanks to 3D printing. Dr. Simin Li, a Senior Lecturer in Mechanics of Biomaterials, and a team of researchers in the School of Mechanical, Electrical, and Manufacturing Engineering have pioneered a fully digital design-to-manufacturing process that has the potential to revolutionize lower limb socket production by allowing printing outside of hospital settings.
Traditionally, the creation of a lower limb socket has been a time-consuming process, taking around three-to-six weeks. This method involves taking a cast of the limb, which serves as a mold for crafting a socket. The process necessitates visits to hospitals, relies heavily on labor-intensive skills and expertise, and often involves a trial-and-error approach. According to Dr Li, the resulting sockets are more akin to ‘works of art than medical devices’ and can lead to skin and stability issues if they do not fit perfectly. This process also has to be repeated frequently as sockets wear down quickly with use – being replaced every 3-6 months for adults and even more regularly for children.
The team’s method utilizes various technologies (including at least one system from Raise3D) and unique coding to create a socket through a fully digital process. By capturing a 3D scan of the user’s limb with a digital scanner and employing computer-aided design (CAD) software, a personalized design profile is generated, which can then be imported into a 3D printer for manufacturing. The result is a fully customized socket that can be produced in as little as eight hours, making the process significantly faster than current methods.
Unique about Dr. Li’s method is its potential to enable the 3D printing of sockets in remote locations and even in users’ homes. The digital scanning and 3D printing facilities can be deployed to different areas, including under-served regions and developing countries with limited access to healthcare. Lower limb prosthetic users could scan their limb, send the scan to a healthcare expert who can process the design remotely, and receive a customized design file in return. This file can then be used to conveniently print a socket in the user’s location – overcoming geographical barriers and transforming the way personalized medical devices are accessed and produced.
“By using a fully digital design-to-manufacturing workflow and additive manufacturing – or ‘3D printing’ as it’s commonly known – our entire process for creating a socket is quantitative and iterative, therefore, highly customizable, repeatable, and efficient. By using the innovative digital solution, healthcare professions can focus more of their valuable time with users and therefore, increase the accessibility for all and on-demand,” said Dr. Simin Li. “The ultimate goal for this project is to make the design and manufacturing process easier and more accessible for both the healthcare professions and user so that one day the prosthetic socket can be manufactured in local community areas, hospitals, and even in users’ homes on demand.”
The Loughborough University team has optimized its 3D printed socket designs through extensive testing in their in-house developed facilities, which involves subjecting printed prototypes to loads ranging from 6,000 to 16,000 Newtons, equivalent to 7-20 times body weight, depending on the user.
The team’s technique also allows them to increase design freedoms, meaning they can make regions on the socket harder or softer depending on the users’ needs – something Dr. Li hopes will improve comfort and further facilitate users’ participation in play, physical activity, and sports.
Read the rest of this story at VoxelMatters